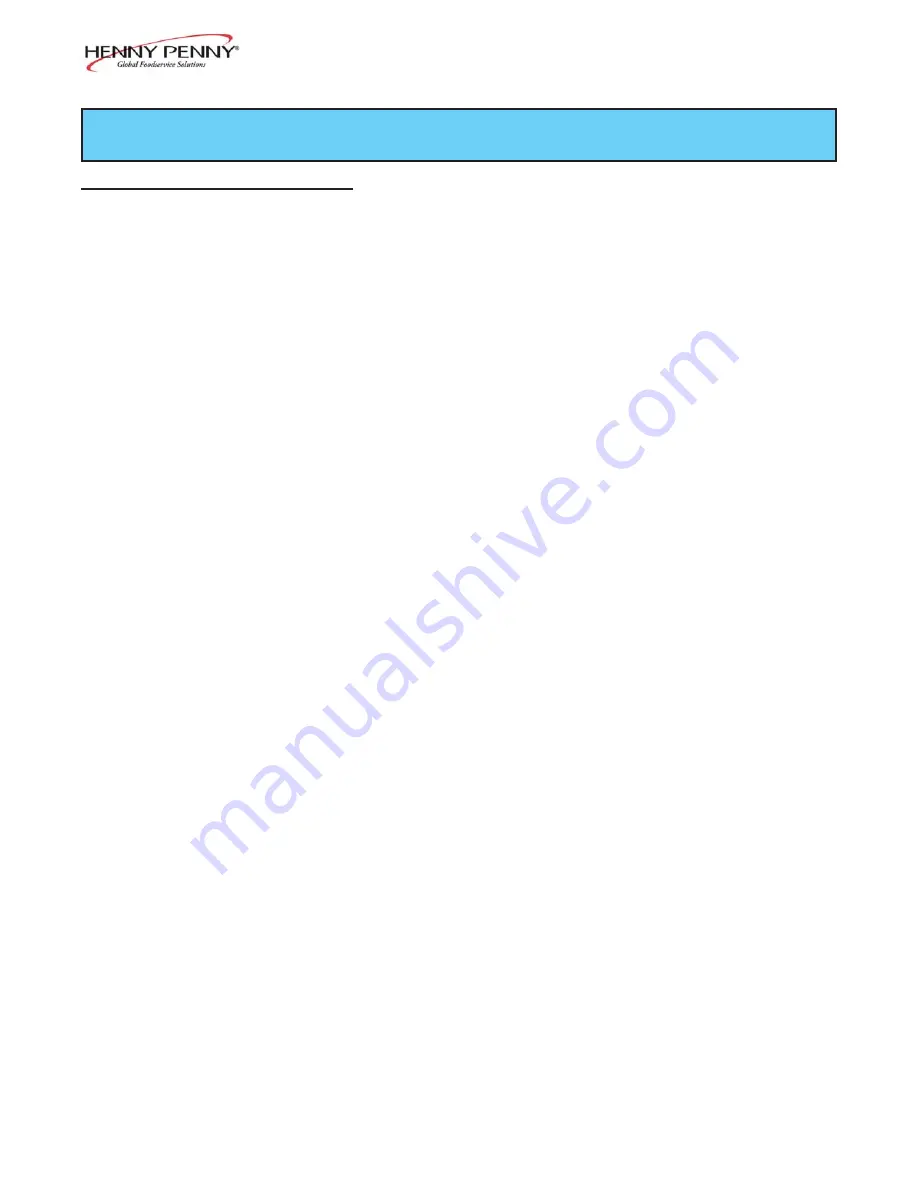
Model OFE- 290
3-1. OPERATING COMPONENTS
POWER/PUMP Switch
A three way switch with center OFF position; move the switch to
the position marked POWER to operate the fryer; move the switch
to the position marked PUMP to operate the filter pump; certain
conditions must be met prior to operation of the filter pump; these
conditions are covered later in this section
Frypot
This reservoir holds the cooking shortening, and is designed to
accommodate the heat exchanger, 6 head of product and an
adequate cold zone for collection of cracklings
Carrier
This stainless steel carrier consists of five racks which contain
the food product during and after frying
Drain Valve
A two-way ball valve, normally in the closed position; turn the
handle to drain the shortening from the frypot into the filter drain
pan
Drain Interlock Switch
A microswitch that provides protection for the frypot in the event an
operator inadvertently drains the shortening from the frypot while
the main switch is in the POWER position; the switch is designed to
automatically shut off the heat when the drain valve is opened
Shortening Mixing System
A shortening mixing capability to help ensure shortening is properly
mixed to prevent an accumulation of moisture and hence boiling
action in the pot; the filter pump is activated by the controls, at
preset intervals, to mix the shortening
Lid Latch
A mechanical catch on the front of the lid which engages a bracket
on the front of the frypot, when lid is lowered
Air Valve
Pumps air into the shortening, periodically, to keep the shortening at
a uniform temperature; this only functions when the unit has been
sitting idle for a period of time, and when heating upfrom a cold
start
403
3-1
SECTION 3. OPERATION