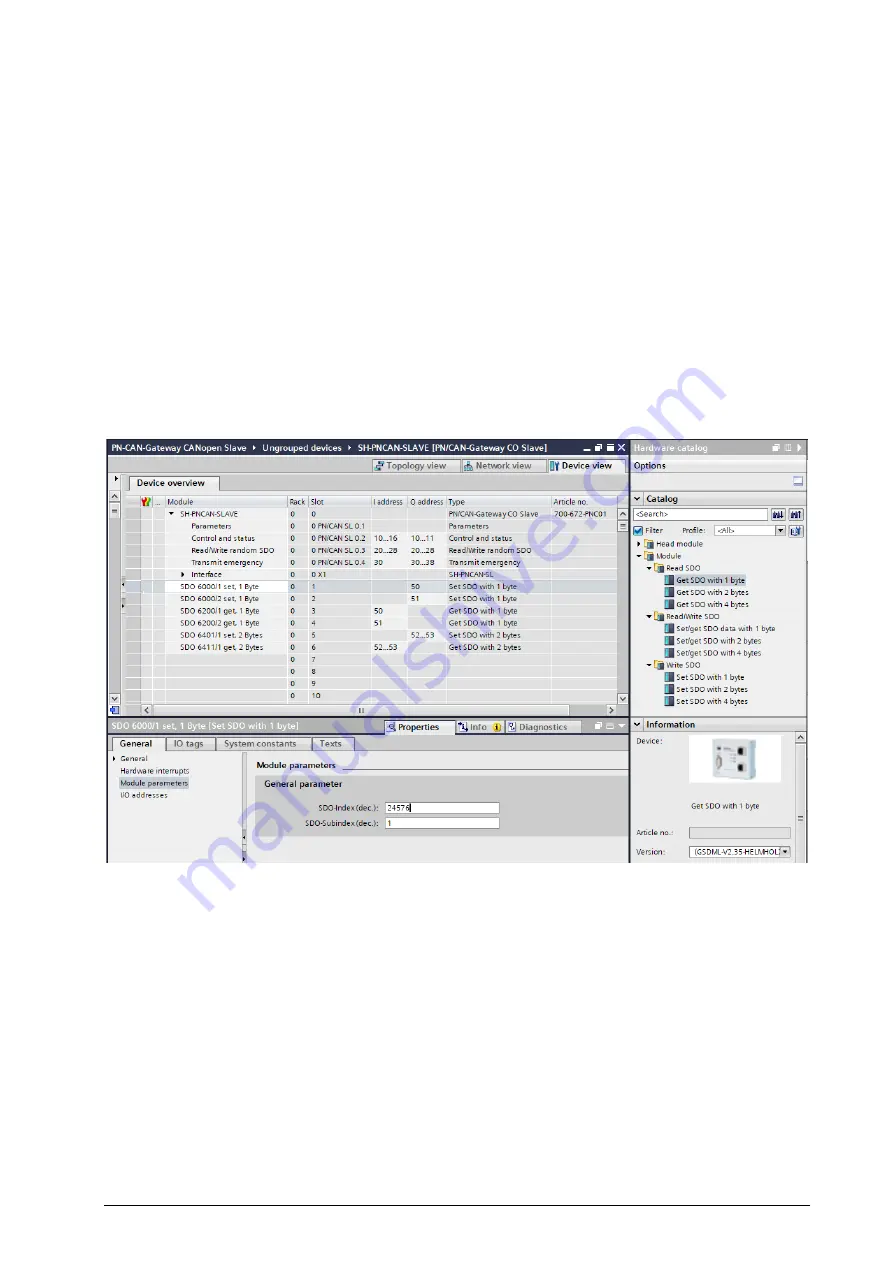
PN/CAN Gateway, PROFINET/CANopen Slave | Version 2 | 1/26/2021
24
Device Node-ID:
Node-ID under which the PN/CAN-Gateway on the CAN bus is active as a device.
When using a DCF file, this parameter must be set to 0, the Node-ID is supplied in the DCF file.
On PLC-Stop performs device reset:
If the PLC goes into Stop, the PN/CAN Gateway data is set to the
initial state and restarted. The values of the SDOs that have not been stored in the Flash are reset to
the state of the EDS/DCF file.
6.2.3
Configuration
The data of the SDOs defined by the EDS or DCF file in the PN/CAN Gateway can now be exchanged
with the PLC. For each SDO or subindex of an SDO a module with the correct data size of the SDO
(1, 2 or 4 bytes) must be inserted in the configuration. In the parameters of the module the SDO index
(number) and the subindex are specified. The index must be specified decimal in the PROFINET
configuration, even if it is usually specified in hexadecimal in CANopen (6000
hex
24576
dec
).
Depending on the access type of the defined SDO you have to choose if the SDO value should be read
from the PN/CAN Gateway ("Read SDO"), written to the PN/CAN Gateway ("Write SDO") or both
("Read/Write SDO").
For the EDS example "DS401_IO_Slave_Vxx.eds" the input SDO 6000 must be described from the PLC
since these are readable values from the point of view of the CANopen network (inputs). The SDO
6200 can be read by the PLC since these are writable values from the point of view of the CANopen
network (outputs).