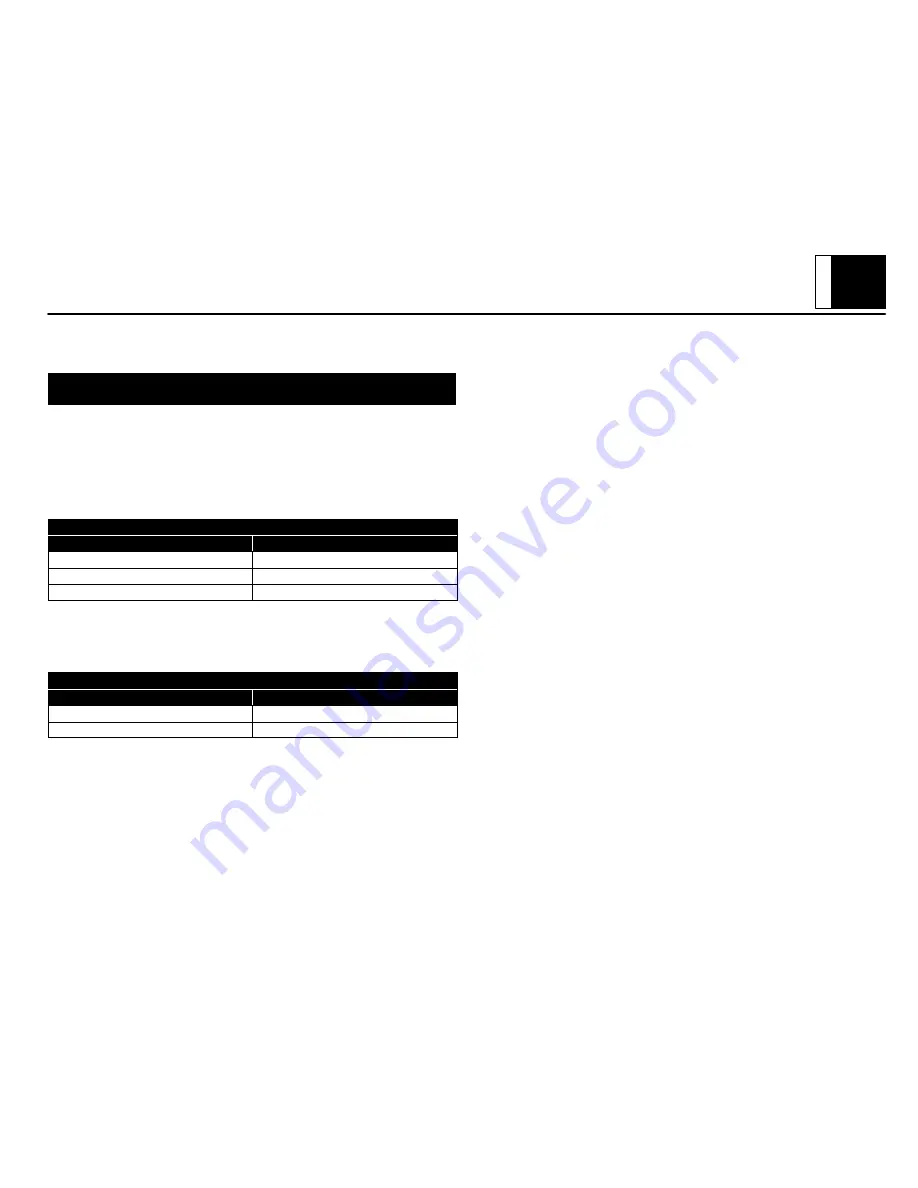
PA
G
E
11
P32/42 C
HASSIS
P32/42 Rev. 12/98
If the body builder installs wheel covers on the vehicle, vented covers must be used. The
minimum vent area is to be the greater of 34 in.2 or 90% of the original vehicle’s wheel
vent zone. Air flow through the wheel vent and cover vent must be direct.
Section 12 – Electrical Battery and Battery Cables
The vehicle battery should be located and positioned to make use of the existing battery
cables. If the battery requires relocation and longer cables are required, a proportionate-
ly larger gauge wire must be used. If in relocating the battery the negative ground cable
is attached to frame rail, a cable of similar gauge be provided between the frame rail and
the engine. This is required due to the heavy electrical loads imposed by the starting
circuit. To ensure proper operation of the battery cables the following chart on length,
gauge and materials must be strictly adhered to:
Combined Length of Positive and Negative
Cable Gauge
Cable in Inches (Copper)
4
66
2
107
0
170
If the battery requires relocation in the engine compartment, the OEM supplied genera-
tor with flat-compensated regulator must be replaced with a generator with temperature
compensated regulator to regulate system voltage compatible with underhood battery
temperatures.
Underhood Battery Location
OEM Part No.
Substitute Part No.
10480170 (105 A)
10480168 (105 A)
10480267 (124 A)
10480255 (124 A)
If the battery is relocated in the engine compartment without replacing generator as
stated above, it will effect the battery life and will be reduced by 50% of the average bat-
tery life.
Battery Installation
The battery and cable installation, provided by the body upfitter, must comply with the
following guidelines. Non-compliance may result in a failure of the vehicle electrical com-
ponent system, the shutdown of the engine, loss of backup brake system, loss of ABS
braking control, and the possibility of fire.
D
The cables must not contact any sharp edge(s), in either the normal (stored) or
slid (maintenance) position (school bus application).
D
The cables must not be bent in a radius of smaller than 10 times the cable
diameter. Insulation failure can occur if this happens.
D
The cable must be supported by clips spaced at a distance of not more than 450
mm. In this clipping, they shall not have a free movement that will allow rubbing
on any vehicle component, either fixed or moveable.
D
All clips used must be of the rubber-lined type, not rubber dipped.
D
Do not splice the battery cables. Cable modifications can result in vehicle starting
problems and loss of other key systems.
D
The cables must be clipped to the battery tray such that the cable pull loads are
not transferred into the battery posts due to slide tray movement. Failure to do
so can result in loose terminals, poor starting and battery failure. Battery acid
leakage could result around posts not properly relieved of strain.
D
The cable attachments at the battery terminal must not cause undue strain at
these connections. There should be no sharp bends in the cables adjacent to the
connections. The cables should be routed down from the terminals rather than
horizontally from the terminals to prevent a lever action that may loosen
connections. Terminal corrosion inhibitors and other coatings should not be
applied to the sealed electrical contact areas. Terminal torque of the sealed
terminal shall be 10/20 N-M freedom, 14/20 N-M linehaul.
D
Mounting Base (Tray):
The tray should be of substantial material (minimum 1.75 mm thick or sufficiently
reinforced) to resist flexing and cracking. The tray must provide firm, continuous
support of the battery and not amplify vibration levels. There must be no
protrusions or projections in the tray or mountings that would damage the battery.
Cantilevered mountings are not recommended and the tray should be mounted
flat so as not to aggravate electrolyte spillage or lead fatigue. A rounded lip of
adequate height to ensure stiffness and retention should be provided around the
perimeter of the tray. With the battery mounted in a vehicle, a static force of 22
kg applied to a 6.54 sq. cm. area at any corner should not move the battery any
more than .25 mm.
D
Freedom Battery:
The hold-down must be able to prevent the battery movement relative to the
mounting base or hold-down. Torque at the battery hold-down shall be 15/20 N-m
(133-177 lbs.-in) at the base clamp or 2.3/4.5 N-m (20-40 lbs.-in.) at the top bar.
A bottom hold-down centrally located at the sides of the battery is recommended.
D
Linehaul Battery:
A tight, secure hold-down is essential. Hold-down brackets must retain the
battery at a 22G-3 millisecond shock loading. A top hold-down should be spaced
Summary of Contents for P32
Page 32: ...PAGE 32 P32 42 CHASSIS P32 42 Rev 12 98 P 30032 Auto Apply Park Brake Harness Ground...
Page 33: ...PAGE 33 P32 42 CHASSIS P32 42 Rev 12 98 P 30000 Instrument Cluster Location...
Page 35: ...PAGE 35 P32 42 CHASSIS P32 42 Rev 12 98 P 30000 Chassis Data...
Page 36: ...PAGE 36 P32 42 CHASSIS P32 42 Rev 12 98 P 30032 Taperleaf Suspension...
Page 37: ...PAGE 37 P32 42 CHASSIS P32 42 Rev 12 98 P 30042 Gas Engine 5 7L V8 Option L31...
Page 38: ...PAGE 38 P32 42 CHASSIS P32 42 Rev 12 98 P 30042 Gas Engine 4 3L V6 Option L35...
Page 39: ...PAGE 39 P32 42 CHASSIS P32 42 Rev 12 98 P 30032 Gas Engine 7 4L V8 Option L29...
Page 40: ...PAGE 40 P32 42 CHASSIS P32 42 Rev 12 98 P 30032 Diesel Engine 6 5L Turbo Ho Option L65...
Page 41: ...PAGE 41 P32 42 CHASSIS P32 42 Rev 12 98 P 30042 Diesel Engine 6 5L HO Option L57...
Page 43: ...PAGE 43 P32 42 CHASSIS P32 42 Rev 12 98 P 30042 Air Conditioning Fittings...
Page 44: ...PAGE 44 P32 42 CHASSIS P32 42 Rev 12 98 P 30042 Air Conditioning Compressor Locations...
Page 45: ...PAGE 45 P32 42 CHASSIS P32 42 Rev 12 98 P 300 32 42 Fuel Filler Neck...
Page 46: ...PAGE 46 P32 42 CHASSIS P32 42 Rev 12 98 P 30000 Fuel Tank Arrangement...
Page 47: ...PAGE 47 P32 42 CHASSIS P32 42 Rev 12 98 P 30000 Temporary Fuel Tank Arrangement...
Page 48: ...PAGE 48 P32 42 CHASSIS P32 42 Rev 12 98 P 30000 Center High Mounted Stop Lamp CHMSL...
Page 49: ...PAGE 49 P32 42 CHASSIS P32 42 Rev 12 98 P 300 32 42 Lamp Mounting P 30032 P 30042...
Page 50: ...PAGE 50 P32 42 CHASSIS P32 42 Rev 12 98 P 300 32 42 Instrument Panel Cut Out...