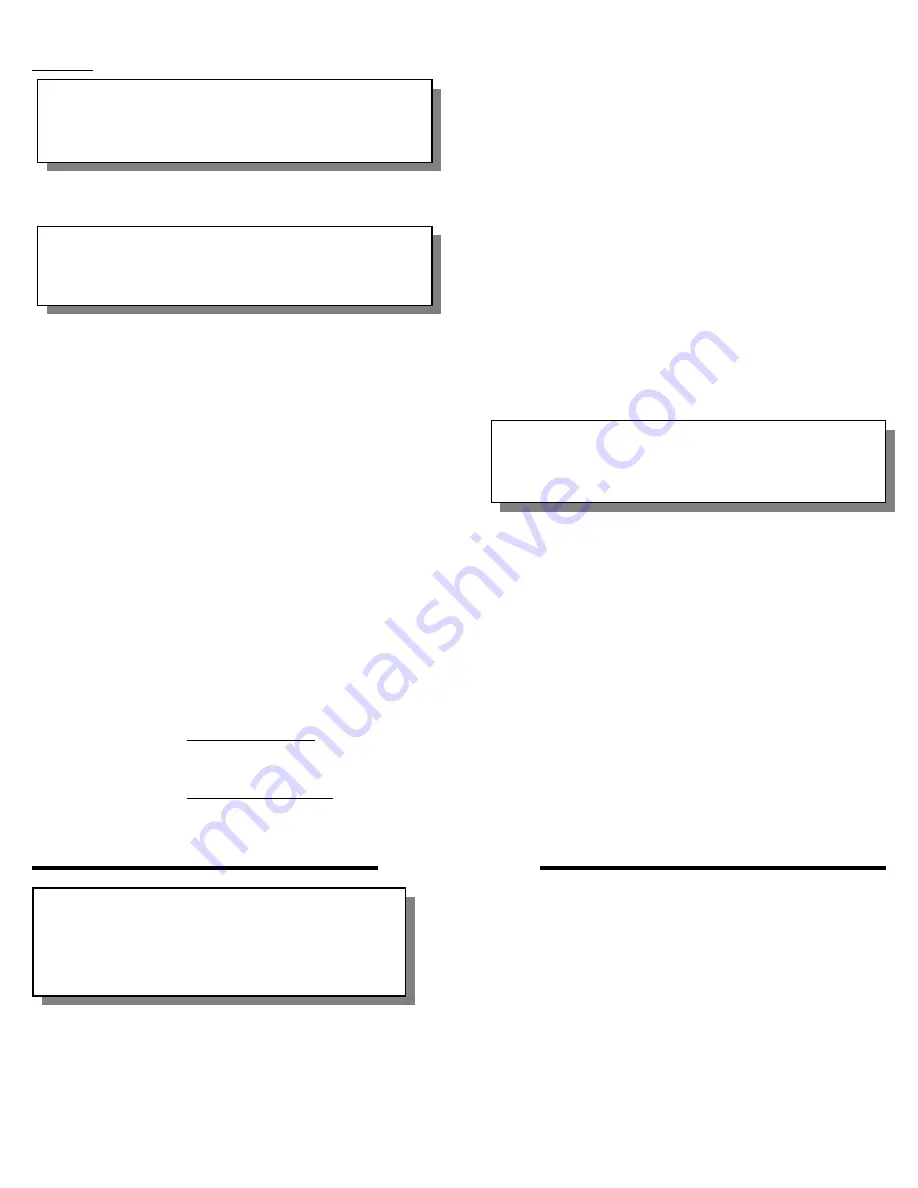
Insulation
Wiring
to
the
heater
should
be
permanently
installed
in
metallic
or
non
‐
metallic
electrical
grade
conduit
in
accordance
with
all
applicable
electrical
codes,
and
should
include
a
grounding
conductor
if
non
‐
metallic
conduit
is
used.
3
WARNING
Surfaces
of
the
heater
pipe
extending
beyond
the
user’s
vessel
may
be
extremely
hot.
Avoid
contact
to
prevent
personnel
injury
or
fire.
Field
supply
wiring
must
be
rated
for
600Vac.
Use
copper
conductors.
The
electrical
installation
should
include
a
service
disconnect
switch
in
sight
of
the
heater,
as
well
as
branch
circuit
over
‐
current
protection
and
over
‐
temperature
protection
(if
a
remote
control
panel
was
not
provided
with
the
heater).
The
customer
may
prefer
to
insulate
the
flange
or
pipe
at
the
tank
for
personnel
safety
and
energy
conservation.
WARNING
Do
not
insulate
the
terminal
enclosure
or
the
first
2”
of
the
pipe.
Dangerous
over
‐
heating
of
the
terminal
box
wiring
could result
.
Where
thermocouple
extension
wire
is
required
between
the
heater
and
control
panel,
verify
it
is
connected
with
proper
polarity
as
shown
on
the
wiring
diagram.
Failure
to
do
so
may
result
in
an
uncontrolled
heater.
Refer
to
the
wiring
diagram
for
the
required
wire
type.
Shielded
wire
is
recommended
to
reduce
signal
interference.
The
heating
elements
are
provided
with
a
“cold
section”
where
stainless
steel
bussing
is
used
to
connect
to
the
heating
coils.
This
area
must
be
packed
with
insulation
to
prevent
over
‐
temperature
of
the
terminal
enclosure.
Refer
to
warning
above.
Use
care
when
making
connections
to
the
heating
element
to
avoid
breaking
the
end
ceramic.
Electrical
Instructions
The
potentially
high
operating
and
ambient
temperatures
of
Pipe
Insert
Heaters
require
field
wiring
to
the
heater
to
be
carefully
matched
to
the
application
to
avoid
serious
injury
or
damage
to
the
equipment.
The
wiring
must
be
de
‐
rated
for
the
expected
terminal
box
temperature.
If
the
cold
section
of
the
heater
is
properly
insulated,
90
o
C
minimum
wire
may
be
used.
Refer
to
the
National
Electrical
Code.
WARNING
Retighten
all
electrical
connections
that
may
have
loosened
during
shipment.
Failure
to
do
so
may
result
in
damage
to
the
heater
or
risk
of
fire.
Confirm
all
unused
conduit
holes
in
the
terminal
box
are
sealed
with
plugs
suitable
for
the
heater
environment.
Attach
a
ground
conductor
to
the
mounting
screw
for
the
heater
in
the
terminal
box
or
by
other
appropriate
means
per
NEC
Article
250.
The
size
and
type
of
incoming
field
wiring
will
depend
upon
the
heater
terminal
box
temperature.
The
terminal
box
temperature
is
a
function
of
the
maximum
outlet
temperature,
heater
current
draw
per
conductor,
number
of
conductors
per
conduit,
and
wire
insulation
rating.
Field
supplied
conductors
must
be
sized
for
at
least
125%
of
the
circuit
current.
Be
sure
the
terminal
box
cover
is
properly
installed
at
all
times
to
ensure
personnel
protection.
Also,
contaminants
can
create
leakage,
(shock)
hazards,
permanent
heater
damage
or
failure
and
should
be
avoided.
To
calculate
the
circuit
current
(in
amps):
It
is
recommended
to
perform
an
insulation
resistance
test
prior
to
energizing
the
equipment.
If
the
value
is
less
than
1
Meg
ohm
using
a
500Vdc
or
similar
tester,
refer
to
Maintenance
and
Troubleshooting
sections.
KW
x
1000
Single
phase
Line
current
Line
Voltage
KW
x
1000
Three
phase
Line
current
1.732
x
Line
Voltage
OPERATION
During
initial
heating,
it
is
recommended
to
slowly
ramp
up
the
process
set
point
and
inspect
the
heating
system
for
problems.
DO
NOT
operate
heaters
at
voltages
in
excess
of
that
marked
on
the
heater.
Excess
voltage
can
shorten
heater
life
or
overload
the
branch
circuit
wiring.
DO
NOT
operate
heaters
at
pipe
temperatures
higher
than
the
recommended
maximum.
Excess
temperatures
can
cause
premature
failure.
Generally,
pipe
materials
are
limited
to
the
following
maximum
temperatures.
WARNING
DO
NOT
TURN
ON
HEATING
ELEMENTS
UNTIL
TANK
IS
COMPLETELY
FULL
OF
FLUID.
Permanent
damage
may
result
if
elements
are
energized
and
the
heater
is
not
completely
submerged.
To
operate
this
heater,
ensure
the
tank
is
completely
filled
with
liquid,
and
energize
the
main
supply
disconnect.
Set
the
controlling
device
to
the
desired
temperature.