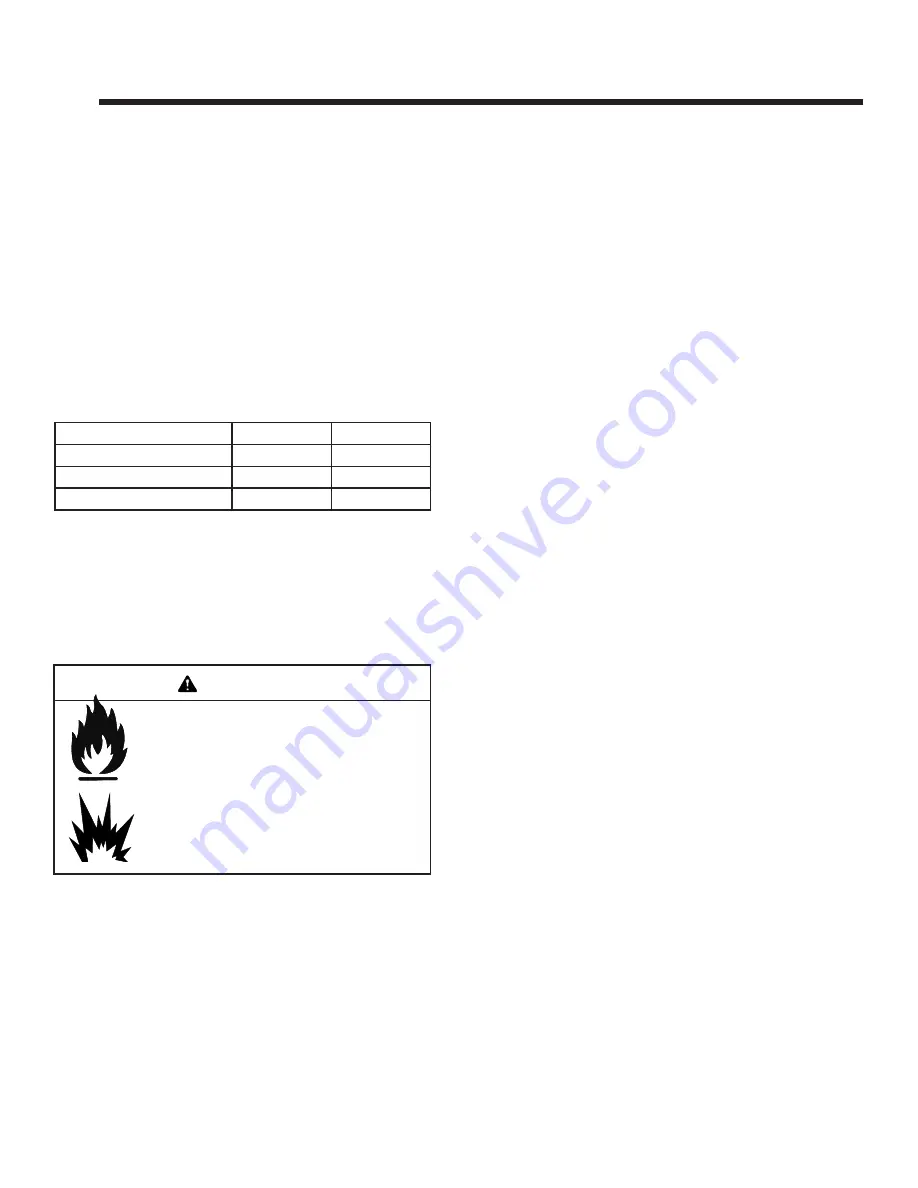
Heatilator • NDI30-C, NDI30-SP, NDI35-C, NDI35-SP, NDI30-SPFK, NDI35-SPFK • 2226-901 Rev. K • 11/12
26
A. Fuel Conversion
• Make sure the appliance is compatible with available gas
types.
• Conversions must be made by a qualifi ed technician
(NFI certifi ed or factory-trained) using Hearth & Home
Technologies specifi ed and approved parts.
B. Gas Pressure
• Optimum appliance performance requires proper input
pressures.
• Gas line sizing requirements will be determined in ANSI
Z223.1 National Fuel Gas Code in the USA and CAN/
CGA B149 in Canada.
• Pressure requirements are:
C. Gas Connection
• Refer to Reference Section 14 for location of gas line
access in appliance.
• Gas line may be run through knockout(s) provided.
• The gap between supply piping and gas access hole may
be caulked with caulk with a minimum of 300ºF continuous
exposure rating or stuffed with non-combustible, unfaced
insulation to prevent cold air infi ltration.
• Ensure that gas line does not come in contact with outer
wrap of the appliance. Follow local codes.
• Pipe incoming gas line into valve compartment.
• Connect incoming gas line to the 1/2 in. (13 mm)
connection on manual shutoff valve.
WARNING! Risk of Fire/Explosion! Support control
when attaching pipe to prevent bending gas line.
• A small amount of air will be in the gas supply lines.
WARNING! Risk of Fire/Explosion! Gas build-up during
line purge could ignite.
• Purge should be performed by technician certifi ed by
NFI or factory-trained.
• Ensure adequate ventilation.
• Ensure there are no ignition sources such as sparks
or open fl ames.
Light the appliance. It will take a short time for air to purge
from lines. When purging is complete the appliance will
light and operate normally.
WARNING! Risk of Fire, Explosion or Asphyxiation!
Check all fi ttings and connections with a non-corrosive
commercially available leak-check solution. DO NOT use
open fl ame. Fittings and connections could have loos-
ened during shipping and handling.
WARNING! Risk of Fire! DO NOT change valve settings.
This valve has been preset at the factory.
WARNING! Risk of Fire/Explosion! High pressure will
damage valve. Low pressure may cause explosion.
• Verify inlet pressures. Verify minimum pressures when
other household gas appliances are operating.
• Install regulator upstream of valve if line pressure is
greater than 1/2 psig.
9
9
Gas Information
Note:
Have the gas supply line installed in accordance with
local codes, if any. If not, follow ANSI 223.1. Installation
should be done by a qualifi ed installer approved and/or
licensed as required by the locality. (In the Commonwealth
of Massachusetts installation must be performed by a
licensed plumber or gas fi tter).
Note:
A listed (and Commonwealth of Massachusetts ap-
proved) 1/2 inch (13 mm) T-handle manual shut-off valve
and fl exible gas connector are connected to the 1/2 inch
(13 mm) control valve inlet.
• If substituting for these components, please consult
local codes for compliance.
D. High Altitude Installations
NOTICE: If the heating value of the gas has been reduced,
these rules do not apply. Check with your local gas utility
or authorities having jurisdiction.
When installing above 2000 feet elevation:
• In the USA: Reduce burner orifi ce 4% for each 1000 feet
above 2000 feet.
• In the CANADA: Reduce burner orifi ce 10% for elevations
between 2000 feet and 4500 feet. Above 4500 feet,
consult local gas utility.
Fire Risk.
Explosion Hazard.
High pressure will damage valve.
• Disconnect gas supply piping BEFORE
pressure testing gas line at test pressures
above 1/2 psig.
• Close the manual shutoff valve BEFORE
pressure testing gas line at test pressures
equal to or less than 1/2 psig.
WARNING
Gas Pressure
Natural Gas
Propane
Minimum inlet pressure
5.0 in. w.c.
11.0 in. w.c.
Maximum inlet pressure
10.0 in. w.c.
13.0 in. w.c.
Manifold pressure
3.5 in. w.c.
10.0 in. w.c.