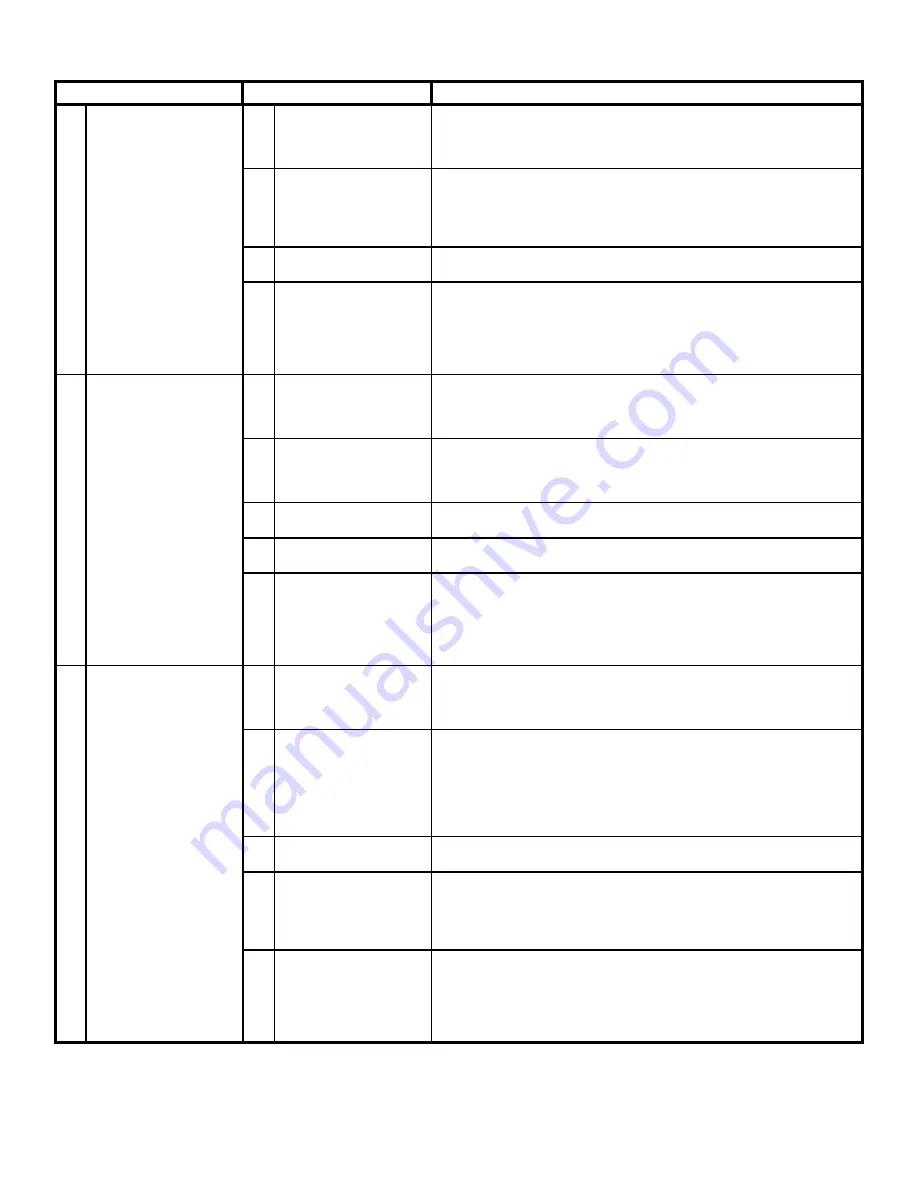
36
Heatilator • Novus BV-Mesh • 4031-553 Rev F • 11/07
B. Intelli
fi
re Ignition System
Symptom
Possible Causes
Corrective Actions
1.
The ignitor/module makes
noise, but no spark.
A.
Incorrect wiring.
Verify “S” wire (white) for sensor and “I” wire (orange) for ignitor are
connected to the correct terminals on the module and the pilot assembly.
Reversed wires at the module may cause the system to make a sparking
noise, but the spark may not be present at pilot hood.
B.
Loose connections or
electrical shorts in the
wiring.
Verify there are no loose connections or electrical shorts in wiring from
module to pilot assembly. The rod closest to the pilot hood should be ignitor.
Verify connections underneath pilot assembly are tight; also verify the
connections are not grounding out to the metal chassis, pilot burner, pilot
enclosure, mesh screen if present, or any other metal object.
C.
Ignitor gap is too large.
Verify gap of ignitor to pilot hood. The gap should be approximately .17 in. or
1/8 in.
D.
Faulty module.
Turn ON/OFF rocker switch or wall switch to OFF position. Remove ignitor
wire “I” from module. Place ON/OFF rocker switch or wall switch in ON
position. Hold ground wire about 3/16 in. away from “I” terminal on module. If
there is no spark at “I” terminal, module must be replaced. If there is a spark
at “I” terminal, module is
fi
ne. Inspect pilot assembly for shorted sparker wire
or cracked insulator around electrode.
2.
Pilots won’t light, there is
no noise or spark.
A.
Transformer installed
incorrectly.
Verify that transformer is installed and plugged into module. Check voltage of
transformer under load at space connection on module with ON/OFF switch
in ON position. Acceptable readings of a good transformer are between 3.2
and 2.8 volts AC.
B.
A shorted or loose
connection in wiring
con
fi
guration or wiring
harness.
Remove and reinstall the wiring harness that plugs into module. Verify there is
a tight
fi
t. Verify pilot assembly wiring to module. Remove and verify continuity
of each wire in wiring harness.
C.
Improper wall switch
wiring.
Verify wall switch is wired correctly.
D.
Module not grounded.
Verify black ground wire from module wire harness is grounded to metal
chassis of appliance.
E.
Faulty module.
Turn ON/OFF rocker switch or wall switch to OFF position. Remove ignitor
wire “I” from module. Place ON/OFF rocker switch or wall switch in ON
position. Hold ground wire about 3/16 in. away from “I” terminal on module. If
there is no spark at “I” terminal module must be replaced. If there is a spark at
“I” terminal, module is
fi
ne. Inspect pilot assembly for shorted sparker wire or
cracked insulator around electrode.
3.
Pilot lights but continues
to spark, and main burner
will not ignite. (If the pilot
continues to spark after
the pilot
fl
ame has been
lit,
fl
ame recti
fi
cation has
not occurred.)
A.
A shorted or loose
connection in sensor rod.
Verify all connections to wiring diagram in manual. Verify connections
underneath pilot assembly are tight. Verify connections are not grounding out
to metal chassis, pilot burner, pilot enclosure or screen if present, or any other
metal object.
B.
Poor
fl
ame recti
fi
cation or
contaminated sensor rod.
Verify
fl
ame is engul
fi
ng sensor rod. If the pilot assembly does not have a
ground strap, consider installing one to increase
fl
ame recti
fi
cation. Verify
correct pilot ori
fi
ce is installed and inlet gas speci
fi
cations are met. Flame
carries recti
fi
cation current, not the gas. If
fl
ame lifts from pilot hood, the
circuit is broken. A wrong ori
fi
ce or too high an inlet pressure can cause pilot
fl
ame to lift. The sensor rod may be contaminated. Clean sensor rod with
emery cloth.
C.
Module is not grounded.
Verify that module is securely grounded to metal chassis of appliance. Verify
that the wire harness is
fi
rmly connected to module.
D.
Damaged pilot assembly
or dirty sensor rod.
Verify that ceramic insulator around the sensor rod is not cracked, damaged,
or loose. Verify connection from sensor rod to white sensor wire. Clean
sensor rod with emery cloth to remove any contaminants that may have
accumulated on sensor rod. Verify continuity with a multimeter with ohms set
at lowest range.
E.
Faulty module.
Turn ON/OFF rocker switch or wall switch to OFF position. Remove ignitor
wire “I” from module. Place ON/OFF rocker switch or wall switch in ON
position. Hold ground wire about 3/16 in. away from “I” terminal on module. If
there is no spark at “I” terminal, module must be replaced. If there is a spark
at “I” terminal, module is
fi
ne. Inspect pilot assembly for shorted sparker wire
or cracked insulator around electrode.
Summary of Contents for NB3630M
Page 41: ...Heatilator Novus BV Mesh 4031 553 Rev F 11 07 41 This page intentionally left blank...
Page 64: ...64 Heatilator Novus BV Mesh 4031 553 Rev F 11 07 This page intentionally left blank...
Page 65: ...Heatilator Novus BV Mesh 4031 553 Rev F 11 07 65 This page intentionally left blank...
Page 66: ...66 Heatilator Novus BV Mesh 4031 553 Rev F 11 07 This page intentionally left blank...