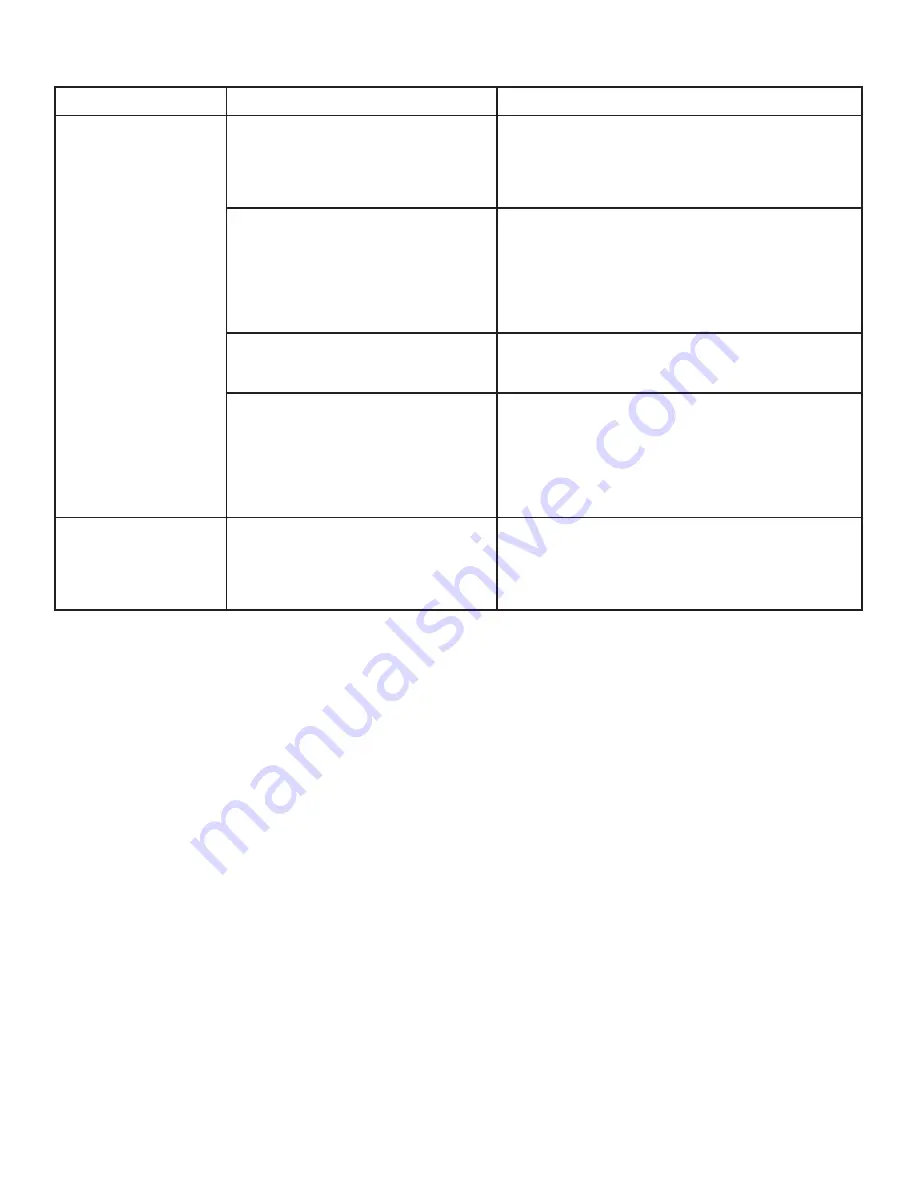
Heatilator • GDST4336I, GDFL4136I, GDCR4136I, GDCL4136I • 2129-900 Rev. W • 12/15
64
Intelli
fi
re Ignition System - (continued)
Symptom
Possible Cause
Corrective Action
4. Pilot lights but contin-
ues to spark, and main
burner will not ignite.
(If the pilot continues
to spark after the
pilot
fl
ame has been lit,
fl
ame recti
fi
cation has
not occurred.)
a. A shorted or loose connection in
fl
ame
sensing rod.
Verify all connections to wiring diagram in manual. Verify
connections underneath pilot assembly are tight. Verify
connections are not grounding out to metal chassis, pilot
burner, pilot enclosure or screen if present, or any other
metal object.
b. Poor
fl
ame recti
fi
cation or contaminated
fl
ame sensing rod.
With
fi
xed glass assembly in place, verify that
fl
ame is en-
gul
fi
ng
fl
ame sensing rod on left side of pilot hood. Flame
sensing rod should glow shortly after ignition. Verify cor-
rect pilot ori
fi
ce is installed and gas inlet is set to pressure
speci
fi
cations. Clean
fl
ame sensing rod with emery cloth to
remove any contaminants that may have accumulated on
fl
ame sensing rod.
c. Module is not grounded.
Verify module is securely grounded to metal chassis of
appliance. Verify that wire harness is
fi
rmly connected to
the module.
d. Damaged pilot assembly or contami-
nated
fl
ame sensing rod.
Verify that ceramic insulator around the
fl
ame sensing
rod is not cracked, damaged, or loose. Verify connection
from
fl
ame sensing rod to white sensor wire. Clean
fl
ame
sensing rod with emery cloth to remove any contaminants
that may have accumulated on
fl
ame sensing rod. Verify
continuity with a multimeter with ohms set at lowest range.
Replace pilot if any damage is detected.
e. Module.
Turn ON/OFF rocker switch or wall switch to OFF position.
Remove ignitor wire “I” from module. Place ON/OFF rocker
switch or wall switch in ON position. If there is no spark at
“I” terminal module must be replaced. If there is a spark at
“I” terminal, module is
fi
ne.