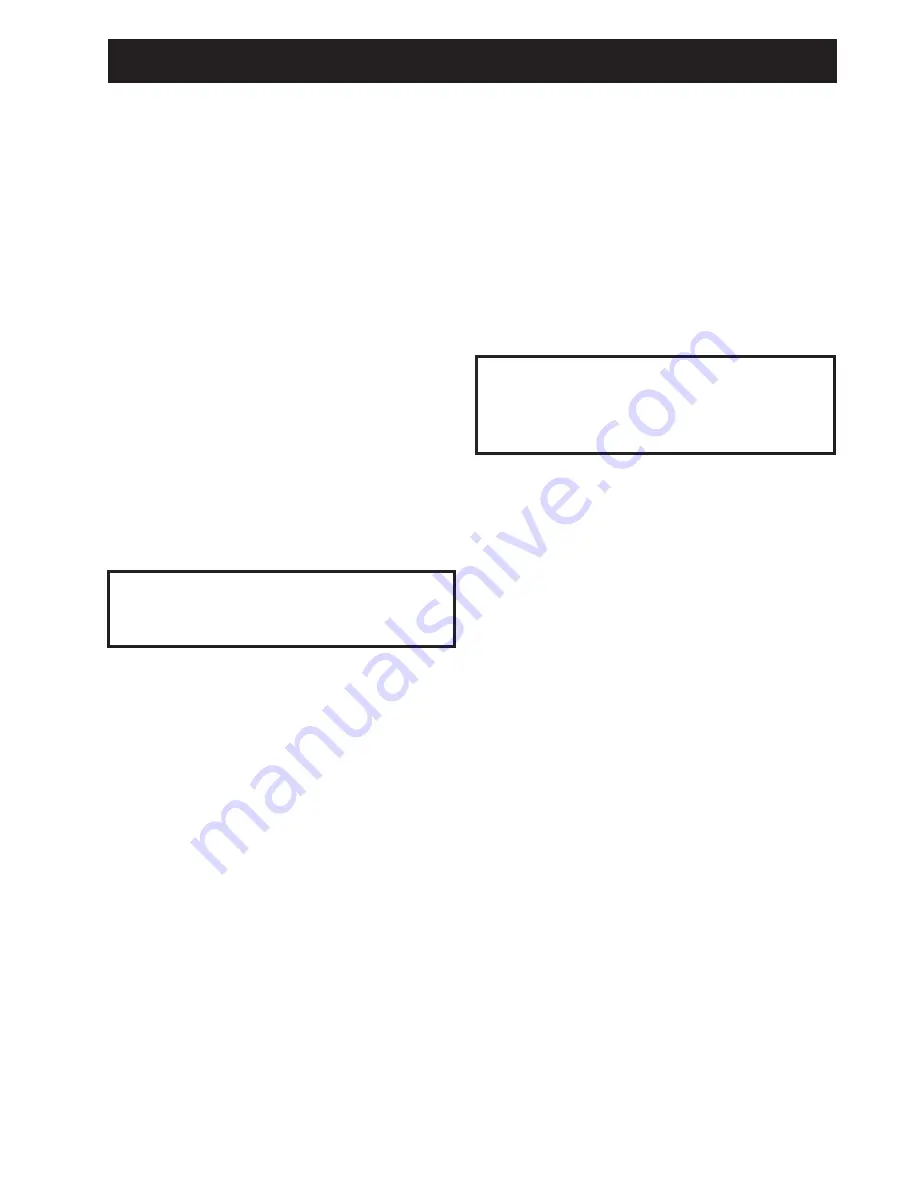
9
Leak Detection
After all lines are connected, the entire system must be
leak tested. The complete system should be pressurized
to not more than 150 psig with refrigerant and dry
nitrogen. The use of an electronic type of leak detector
is highly recommended because of its greater sensitivity
to small leaks. As a further check, it is recommended
that this pressure be held for a minimum of 12 hours and
then rechecked. For a satisfactory installation, the system
must be leak tight.
Within the last several years, manufacturers have
developed fluorescent dye leak detection systems for
use with refrigerants. These dyes mix with the lubricant
and, when exposed to an ultraviolet light “fluoresce,”
indicate the location of leaks. Copeland has tested and
approved the Rigid “System Safe” dye and found it to be
compatible with the compressor materials in systems.
Evacuation
CAUTION: Do not use the refrigeration compressor
to evacuate the system. Do not start the compressor
while it is in a vacuum.
It is of the utmost importance that proper system
evacuation and leak detection procedures be employed.
Copeland recommends a minimum evacuation to 500
microns. In addition, a vacuum decay test is strongly
recommended to assure there is not a large pressure
differential between the system and vacuum pump. Good
evacuation processes include frequent vacuum pump oil
changes and large diameter, short hose connections to
both high and low sides of the system preferably using
bronze braided hose.
A good, deep vacuum pump should be connected to both
the low and high side evacuation valves with copper
tube or high vacuum hoses (1/4” ID minimum). If the
compressor has service valves, they should remain
closed. A deep vacuum gauge capable of registering
pressure in microns should be attached to the system for
pressure readings.
Leak Detection And Evacuation
A shut-off valve between the gauge connection and
vacuum pump should be provided to allow the system
pressure to be checked after evacuation. Do not turn off
vacuum pump when connected to an evacuated system
before closing shut-off valve.
The vacuum pump should be operated until a pressure of
1,500 microns absolute pressure is reached – at which time
the vacuum should be broken with the refrigerant to be
used in the system through a drier until the system pressure
rises above “0” psig.
Note: Refrigerant used during evacuation can not be
vented. Reclaim all used refrigerant. EPA regulations are
constantly being updated. Ensure your procedures follow
correct regulations.
Repeat this operation a second time.
Open the compressor’s service valves and evacuate the
entire system to 500 microns absolute pressure.
Raise the pressure to 2 psig with the refrigerant and
remove the vacuum pump.