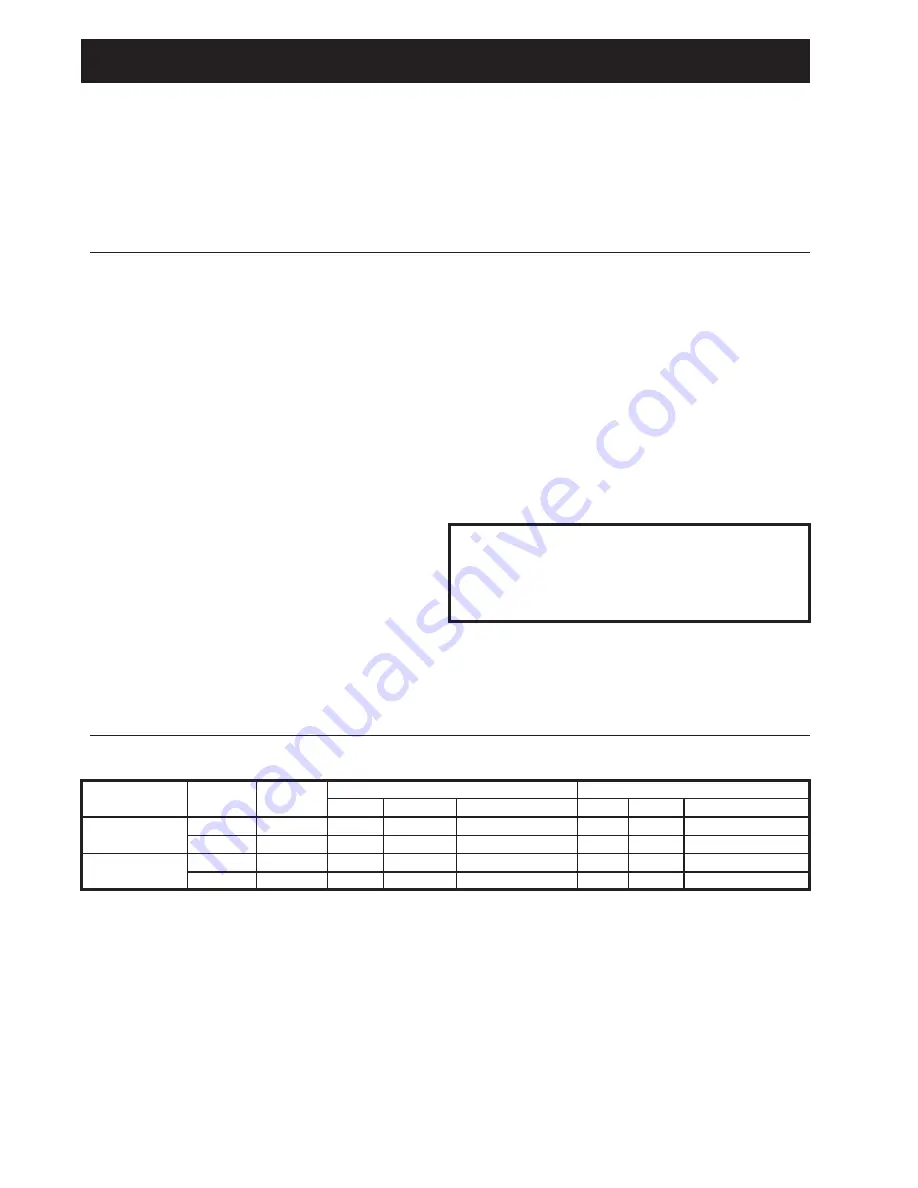
6
The system as supplied by Bohn/Heatcraft, was thoroughly
cleaned and dehydrated at the factory. Foreign matter may enter
the system by way of the evaporator to condensing unit piping.
Therefore, care must be used during installation of the piping
to prevent entrance of foreign matter. Install all refrigeration
system components in accordance with applicable local and
The following procedures should be followed:
(a) Do not leave dehydrated compressors or filter-driers on
condensing units open to the atmosphere any longer
than is absolutely necessary.
(b) Use only refrigeration grade (ACR) copper tubing,
properly sealed against contamination.
(c) Suction lines should slope 1/4” per 10 feet
towards the compressor (in direction of flow).
(d) Suitable P-type oil traps should be located at the
base of each suction riser to enhance oil return to
the compressor.
(e) For desired method of superheat measurement, a
pressure tap should be installed in each evaporator
suction line in the proximity of the expansion valve
bulb.
(f) When brazing refrigerant lines, an inert gas should
be passed through the line at low pressure to pre-
vent scaling and oxidation inside the tubing. Dry
nitrogen is preferred.
(g) Use only a suitable silver solder alloy on suction and
liquid lines.
Refrigeration Piping And Line Sizing
national codes and in conformance with good practice required
for the proper operation of the system. The interconnecting pipe
size is not necessarily the same size as the stub-out on the con-
densing unit or the evaporator.
(h) Limit the soldering paste of flux to the minimum re-
quired to prevent contamination of the solder joint
internally. Flux only the male portion of the connection,
never the female. After brazing, remove excess flux.
(i) Remove temperature sensor attached to suction
line on Beacon II systems before brazing of the
solder joint internally. Flux only the male portion of
the connection – never the female. After brazing,
remove excess flux.
(j) Wrap expansion valves with wet rags during brazing to
the liquid line.
CAUTION: If the temperature gets too high, these components
may be damaged. Heat absorbing compounds or wet rags must
be used to protect the expansion valve when brazing to the
refrigerant piping/line connections, and the suction line sensor
must be removed per above instructions.
(k) Do not use “bull head” tees. This will cause oil return
problems and can cause poor performance.
(l) If isolation valves are installed at the evaporator,
full port ball valves should be used.
Refrigeration Piping And Line Sizing
The remote precharged circuits are provided with a factory
holding charge of R-404A on the soda chiller, and dry
nitrogen on the ice machine. The system charge is located in
the appropriate drink and ice machines. Schrader valve fittings
Table 3. Recommended Line Size In Equivalent Lengths for R-448A/R-449A
Model Room Max.
Max. Suction Line Liquid Line
Riser
25’
50’
Plus 50’
25’
50’
Plus 50’
Freezer
5/8”
5/8”
7/8”
Consult Factory
3/8”
3/8”
Consult Factory
Cooler
5/8”
5/8”
7/8”
Consult Factory
3/8”
3/8”
Consult Factory
Freezer
5/8”
5/8”
7/8”
Consult Factory
3/8”
3/8”
Consult Factory
Cooler
5/8”
7/8”
7/8”
Consult Factory
3/8”
3/8”
Consult Factory
Remote Precharged Circuits
are provided for liquid line charging at the condensing unit.
Consult the appropriate drink and ice machine manufacturers for
details on installation of precharged lines.
MAC8X
MAC7X