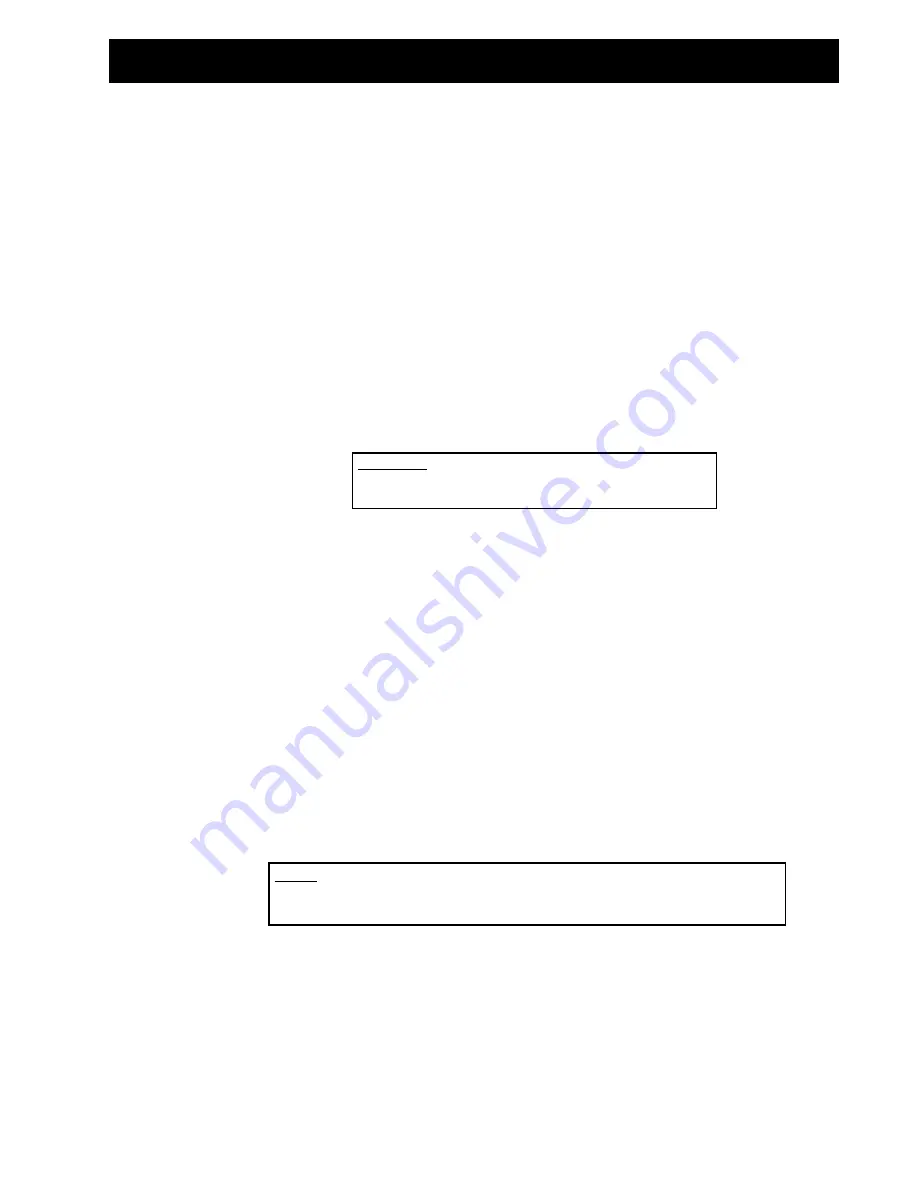
11
Leak Detection And Evacuation
Leak Testing
After all lines are connected, the entire system must be leak tested. The complete system should be
pressurized to not more than 150 PSIG with refrigerant and dry nitrogen. The use of an electronic type
of leak detector is highly recommended because of its greater sensitivity to small leaks. As a further
check, it is recommended that this pressure be held for a minimum of 12 hours and then rechecked. For a
satisfactory installation, the system must be leak tight.
Leak detection can be carried out in the conventional manner. If HCFC or CFC tracer gas is used, care must
be taken to completely remove all traces of the gas prior to introducing HFC’s. Electronic leak detectors
are now available that will sense HFC’s. This is considered preferable since it removes the possibility of
chlorine remaining in the system after leak testing with HCFC’s and/or HCFC’s. There is a view that even
small quantities of chlorine may act as a catalyst encouraging copper plating and/or corrosion and should
therefore be avoided.
Within the last several years, manufacturers have developed fluorescent dye leak detection systems
for use with refrigerants. These dyes mix with the lubricant and, when exposed to an ultraviolet light,
fluoresce to indicate the location of leaks. Copeland has tested and approved the Rigid “System Safe” dye
and found it to be compatible with the compressor materials in systems.
Evacuation
CAUTION:
Do not use the refrigeration compressor
to evacuate the system. Do not start the
compressor while it is in a vacuum.
Due to the smaller molecule size of HFC’s, they will tend to leak more readily than CFC. Consequently, it
is of the utmost importance that proper system evacuation and leak detection procedures be employed.
Copeland recommends a minimum evacuation to 500 microns. In addition, a vacuum decay test is strongly
recommended to assure there is not a large pressure differential between the system and vacuum pump.
Good evacuation processes include frequent vacuum pump oil changes and large diameter, short hose
connections to both high and low sides of the system preferably using bronze braided hose.
A good, deep vacuum pump should be connected to both the low and high side evacuation valves with
copper tube or high vacuum hoses (1/4” ID minimum). If the compressor has service valves, they should
remain closed. A deep vacuum gauge capable of registering pressure in microns should be attached to the
system for pressure readings.
A shut-off valve between the gauge connection and vacuum pump should be provided to allow the
system pressure to be checked after evacuation. Do not turn off vacuum pump when connected to an
evacuated system before closing shut-off valve.
The vacuum pump should be operated until a pressure of 1,500 microns absolute pressure is reached – at
which time the vacuum should be broken with the refrigerant to be used in the system through a drier
until the system pressure rises above “0” psig.
NOTE:
Refrigerant used during evacuation can not be vented.
Reclaim all used refrigerant. EPA regulations are constantly
being updated. Ensure your procedures follow correct regulations.
Repeat this operation a second time.
Open the compressor’s service valves and evacuate the entire system to 500 microns absolute pressure.
Raise the pressure to 2 psig with the refrigerant and remove the vacuum pump.
Summary of Contents for FlexPack H-IM-FP
Page 16: ...16 Preventive Maintenance...
Page 17: ...17 Preventive Maintenance...
Page 22: ...22 Notes...
Page 23: ...23 Notes...