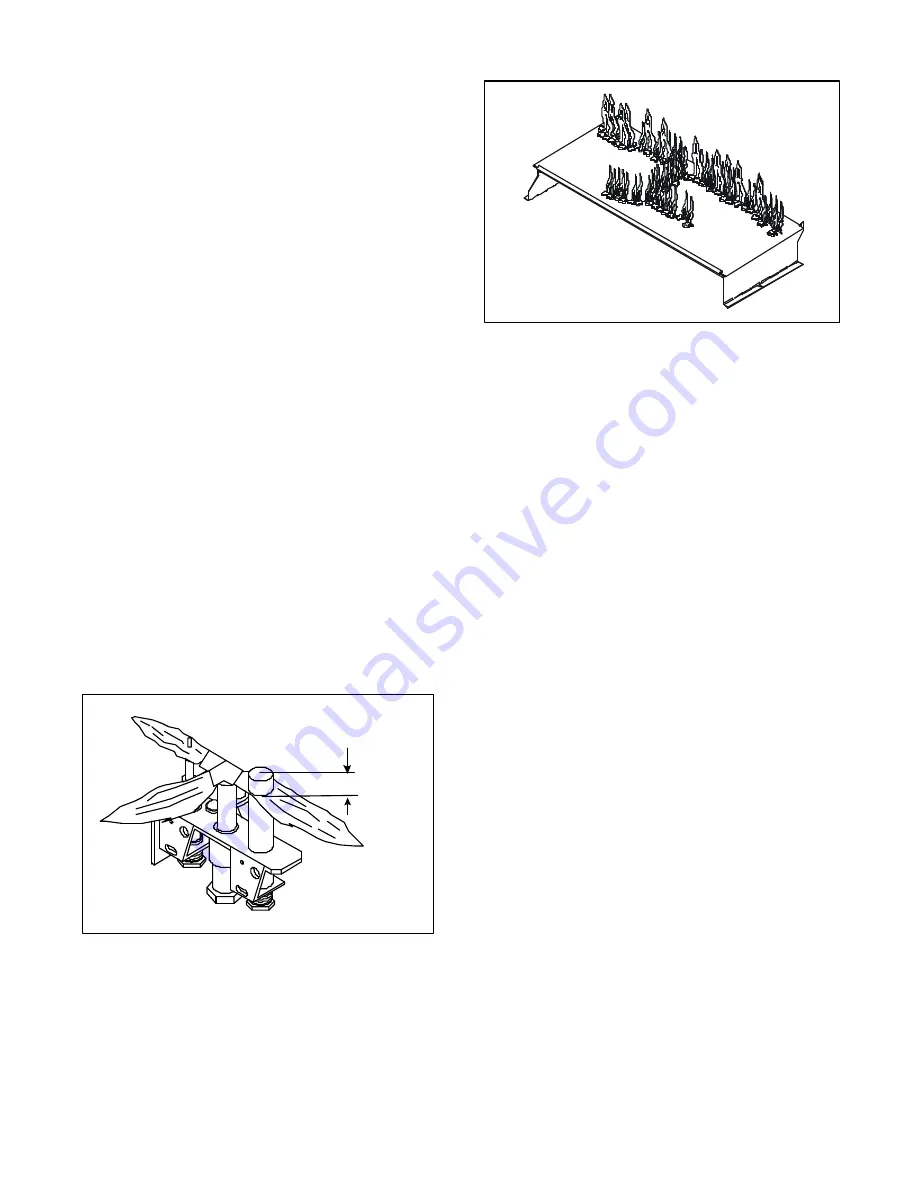
21
1.8 INSTALLER TESTING
The space heater must be tested and be operating ac-
cording to manufacturers specifications prior to the in-
staller leaving the site. Note: the tips of the flames
should never hit the top of the firebox after the unit has
warmed up. Please contact your dealer or a qualified
service person to replace injector or adjust valve.
Upon completing the gas line connection, a small
amount of air will be in the lines. When first lighting the
pilot light, it will take a few minutes for the lines to
purge themselves of this air. Once the purging is com-
plete, the pilot and burner will light and operate as indi-
cated in the Lighting Instructions.
Subsequent lightings of the appliance will not require
such purging.
CAUTION: DURING THE INITIAL PURGING AND
SUBSEQUENT LIGHTINGS, NEVER ALLOW THE
GAS VALVE CONTROL KNOB TO REMAIN DE-
PRESSED IN THE "PILOT" POSITION WITHOUT
PUSHING THE RED IGNITOR BUTTON AT LEAST
ONCE EVERY SECOND.
Follow the Safety Information and Lighting Instructions
pages of this manual to light the appliance.
To obtain proper operation, it is imperative that the pi-
lot and main burner flame characteristics are steady,
not lifting or floating. Typically, the top 3/8-inch (9.5mm)
at the pilot generator should be engulfed in the pilot
flame. (Figure 29)
FIGURE 29.
FIGURE 30.
Standing Pilot
3/8" (9.5mm)
2.0 OPERATING INSTRUCTIONS
This appliance is a balanced flue heater and is designed
to operate with all combustion air being siphoned from
the outside of the building and all exhaust gases ex-
pelled to the outside of the building.
WARNING: THIS UNIT IS NOT FOR USE WITH SOLID
FUEL.
The control system for this model is a millivolt type. It
consists of a gas control valve/variable regulator, a stand-
ing pilot assembly, a thermopile/thermocouple assem-
bly, a piezo ignitor, an ON/OFF rocker switch and a safety
high temperature limit switch. The controls are located
in the lower compartment behind the lower door, and ac-
cess is gained by lifting the door up. See Figure 1.
WARNING: DO NOT CONNECT 220-240 VAC TO THE
GAS CONTROL VALVE OR CONTROL WIRING SYS-
TEM OF THIS UNIT.
The gas control system is wired so the thermopile, when
heated with the pilot light, will provide approximately 350
to 500 millivolts. This activates the gas control valve. See
Figure 31 for appliance wiring diagram.
Additionally, a high temperature limit switch is wired to
ground and will shut-off the pilot and burner should a
high surface temperature condition occur. The pilot and
main burner must be re-lit when the heater cools. See
Figure 31.
When lit for the first time, the appliance will emit a slight
odor for an hour or two. This is due to paint and lubri-
cants used in the manufacturing process. Additionally,
for the first few minutes after each lighting, vapor may
condense and fog the glass and the flames may be blue.
After a few minutes this moisture will disappear and within
15-30 minutes the flames should become yellow.
The heater may produce a noise, caused from metal
expansion and contraction as it heats up and cools down.
This noise is similar to one that a furnace or heat duct
may produce and does not affect the operation or lon-
gevity of the heater.
Burner flame patterns are shown in Figure 29.
Follow Section 3.5 TROUBLESHOOTING for adjusting
the appliance to operate properly.