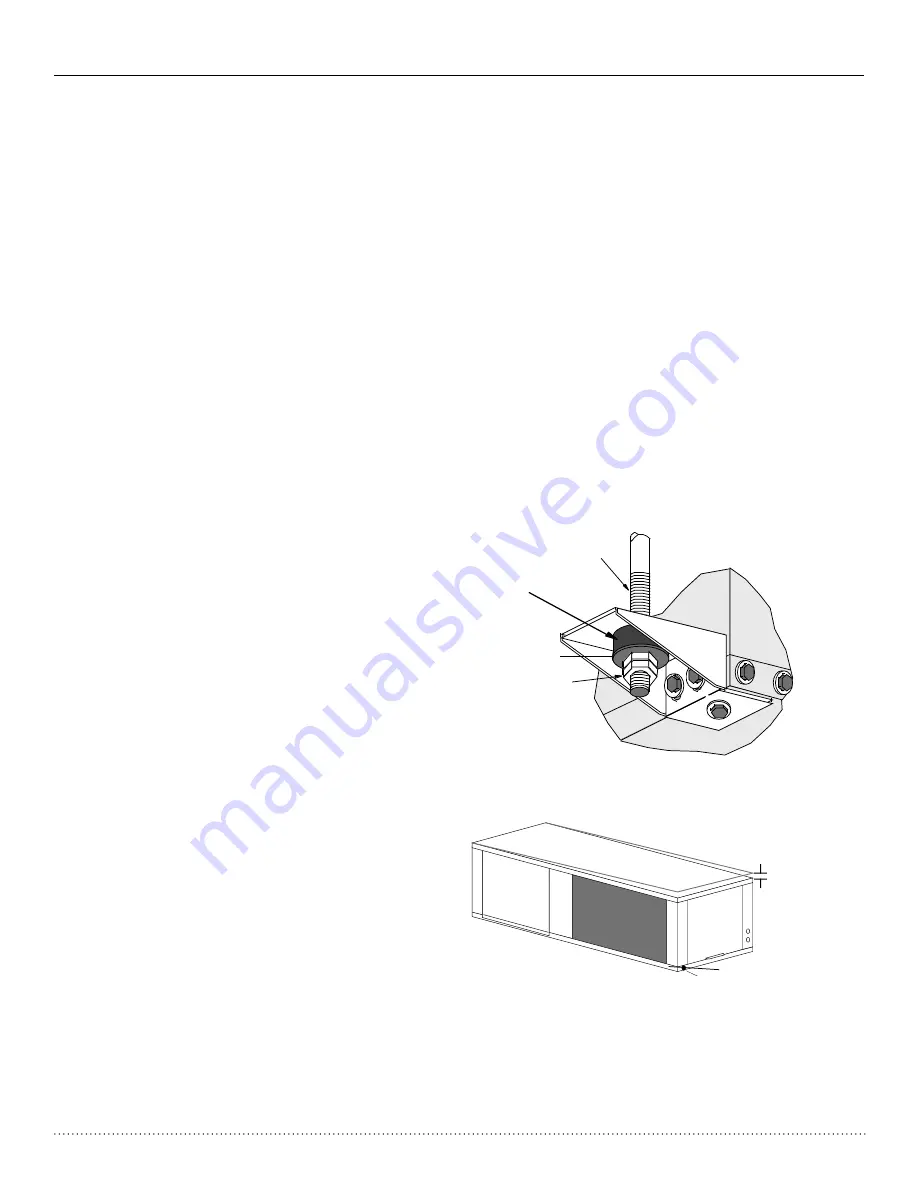
5
Installation, Operation & Maintenance
HTV/HTD/HTH SERIES
Heat Controller, Inc.
General Information
Mounting Horizontal Units
Horizontal units have hanger kits pre-installed from the factory
as shown in Figure 1. Figure 3 shows a typical horizontal unit
installation.
Horizontal heat pumps are typically suspended above a ceiling or
within a soffi t using fi eld supplied, threaded rods sized to support
the weight of the unit.
Use four (4) fi eld supplied threaded rods and factory provided
vibration isolators to suspend the unit. Hang the unit clear of the
fl oor slab above and support the unit by the mounting bracket
assemblies only. DO NOT attach the unit fl ush with the fl oor slab
above.
Pitch the unit toward the drain as shown in Figure 2 to improve
the condensate drainage. On small units (less than 8.8kW) ensure
that unit pitch does not cause condensate leaks inside the
cabinet.
Drain
Connection
1/4” (6.4mm) pitch
per foot for drainage
Figure 1: Hanger Bracket
Figure 2: Horizontal Unit Pitch
Horizontal Unit Location
Units are not designed for outdoor installation. Locate the unit in
an INDOOR area that allows enough space for service personnel
to perform typical maintenance or repairs without removing unit
from the ceiling. Horizontal units are typically installed above a
false ceiling or in a ceiling plenum. Never install units in areas
subject to freezing or where humidity levels could cause cabinet
condensation (such as unconditioned spaces subject to 100%
outside air). Consideration should be given to access for easy
removal of the fi lter and access panels. Provide suffi cient room to
make water, electrical, and duct connection(s).
If the unit is located in a confi ned space, such as a closet,
provisions must be made for return air to freely enter the space
by means of a louvered door, etc. Any access panel screws that
would be diffi cult to remove after the unit is installed should
be removed prior to setting the unit. Refer to Figure 3 for an
illustration of a typical installation. Refer to unit specifi cations
catalog for dimensional data.
Conform to the following guidelines when selecting
unit location:
1. Provide a hinged access door in concealed-spline or plaster
ceilings. Provide removable ceiling tiles in T-bar or lay-in
ceilings. Refer to horizontal unit dimensions for specifi c
series and model in unit specifi cations catalog. Size the
access opening to accommodate the service technician
during the removal or replacement of the compressor and
the removal or installation of the unit itself.
2. Provide access to hanger brackets, water valves and fi ttings.
Provide screwdriver clearance to access panels, discharge
collars and all electrical connections.
3. DO NOT obstruct the space beneath the unit with piping,
electrical cables and other items that prohibit future removal
of components or the unit itself.
4. Use a manual portable jack/lift to lift and support the weight
of the unit during installation and servicing.
The installation of water source heat pump units and all
associated components, parts and accessories which make
up the installation shall be in accordance with the regulations
of ALL authorities having jurisdiction and MUST conform to
all applicable codes. It is the responsibility of the installing
contractor to determine and comply with ALL applicable codes
and regulations.
>PP@7KUHDGHG
5RGE\RWKHUV
9LEUDWLRQ,VRODWRU
IDFWRU\VXSSOLHG
:DVKHU
E\RWKHUV
'RXEOH+H[1XWV
E\RWKHUV
Summary of Contents for HTD Series
Page 48: ...01 2013 97B00 97B00...