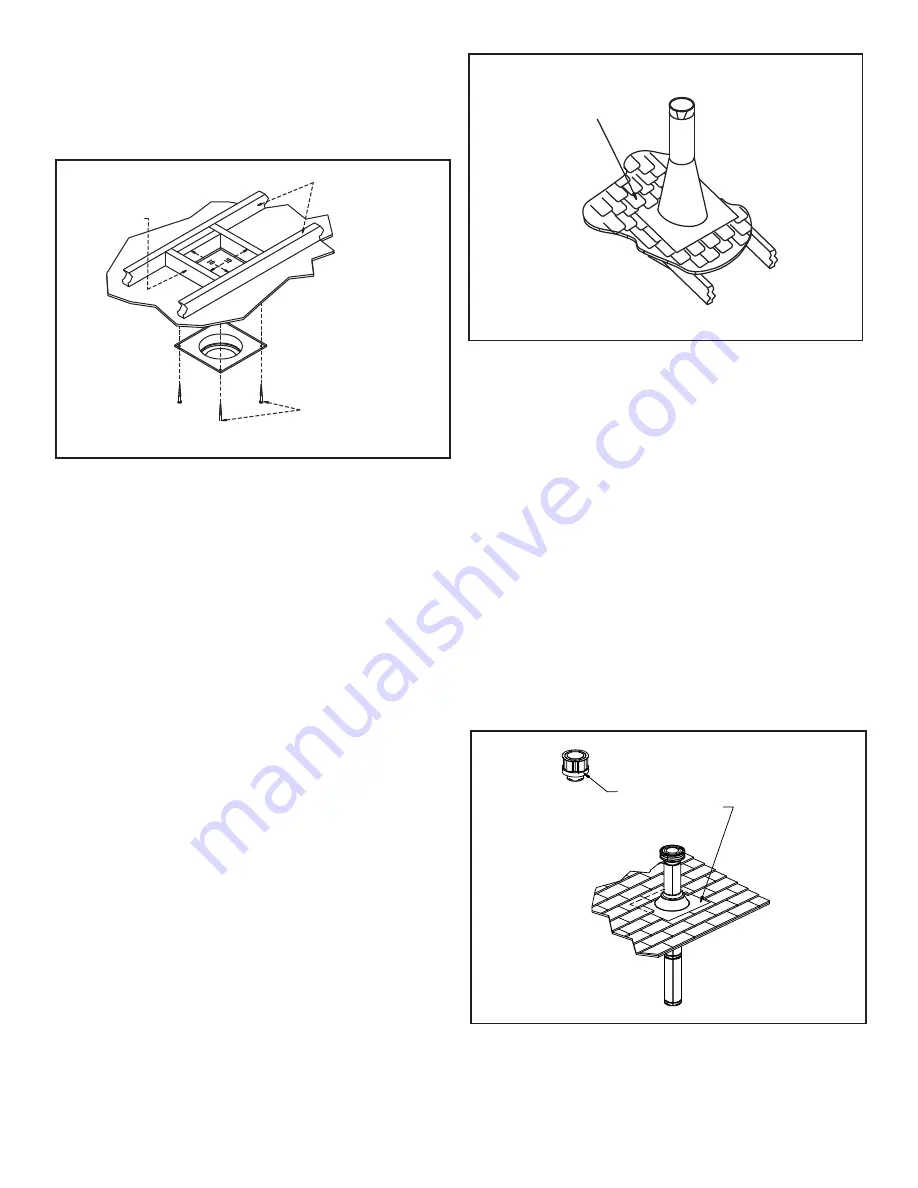
16
Heat & Glo • Tiara Petite B • 7026-101 Rev. N • 10/11
Step 4.
Assemble the desired lengths of pipe and elbows necessary
to reach from the appliance up through the round support
box. Ensure that all pipe and elbow connections are in their
fully twist-locked position. Assemble as instructed.
Step 5.
Cut a hole in the roof centered on the small drill hole placed in
the roof in Step 2. The hole should be of sufficient size to meet
the minimum requirements for clearance to combustibles, as
specified. Continue to assemble lengths of pipe and elbows
necessary to reach from the ceiling support box/wall thimble
up through the roof line. Galvanized pipe and elbows may
be utilized in the attic, as well as above the roofline. The
galvanized finish is desirable above the roofline, due to its
higher corrosion resistance.
NOTE:
(1
) If an offset is necessary in the attic to avoid obstructions,
it is important to support the vent pipe every 3 ft.
(914mm) to avoid excessive stress on the elbows, and
possible separation. Wall straps are available for this
purpose
, Figure 5.12
, page 15.
(2) Whenever possible, use 45° elbows, instead of 90°
elbows. The 45° elbow offers less restriction to the flow
of flue gases and intake air.
Step 7.
Continue to assemble pipe sections until the height of the
vent (before adding the termination cap) meets the minimum
code requirements as outlined in the current CAN/CGA-
B149 Installation Codes (in Canada), the National Fuel
Gas Code NFPA 54/ANSI Z223.1 (in USA), or local codes.
Note that for steep roof pitches, the vent height must be
increased. See roof pitch table (
Figure 4.3
, on page 8). In
high wind conditions, nearby trees adjoining rooflines, steep
pitched roofs, and other similar factors can result in poor
draft, or down drafting. In these cases increasing the vent
height or switching to the high wind termination cap may
solve this problem.
Step 3.
To install the round support box/wall thimble cover in a flat
ceiling, cut a 10 in. (254mm) square hole in the ceiling,
centered on the hole drilled in Step 2. Frame the hole as
shown in
Figure 5.13
.
Framing
1 - 1/2 in. (38mm) Long
Wood Screws
Ceiling
Joists
Figure 5.13
Shingles overlap on
top edge of flashing
CAP AND STORM
COLLAR NOT SHOWN
FOR CLARITY
Figure 5.14
Step 8.
Slip the storm collar over the pipe, and push it down to the
top of the flashing (
Figure 5.15
). Use non-hardening sealant
above and below the joint between the storm collar and the
pipe.
Step 6.
Slip the flashing over the pipe section(s) protruding through
the roof. Secure the base of the flashing to the roof with
roofing nails. Ensure the roofing material overlaps the top
edge of the flashing as shown in
Figure 5.14
. Verify that the
chimney is the required height above the roof. See roof pitch
table,
Figure 4.3,
on page 8.
Optional High Wind Termination Cap
Secure Flashing with Non-Hardening
Sealant and Roofing Nails
Figure 5.15