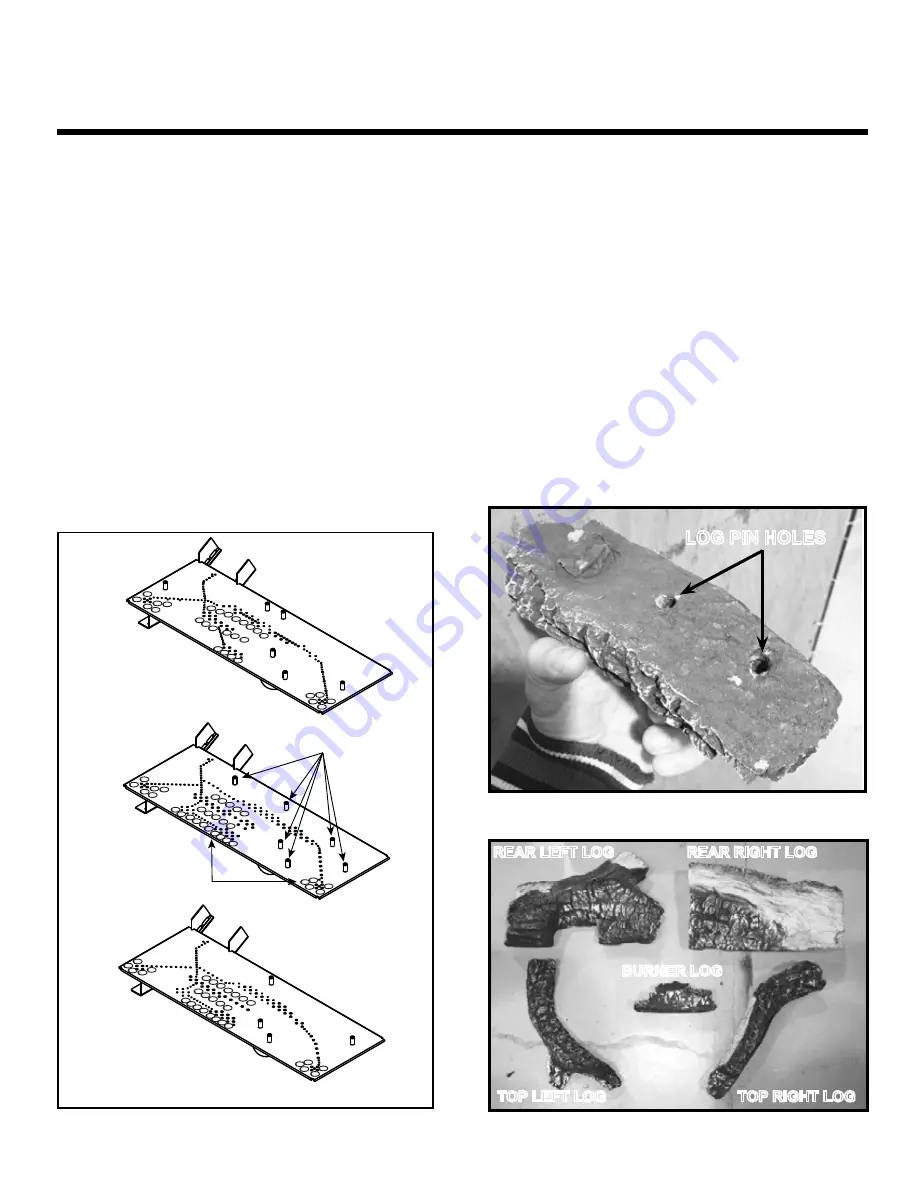
61
Heat & Glo • SL-5, SL-7, SL-9 Installation Manual • 2392-980 Rev. L • 6/17
Log Set Assembly: LOGS-SL5, LOGS-SL7, LOGS-SL9
Models: SL-5, SL-7, SL-9
LOG PLACEMENT
INSTRUCTIONS
Overview
These are common log instructions for the SL-5, SL-7,
and SL-9 models. All three models use the same num
-
ber of components, which are scaled up or down in size,
depending on the model of fireplace installed. Each size
log set consists of five logs.
*The photos shown in these instructions depict an SL-7.
Log Pins
The overall size and location of the burner assembly with-
in the firebox is very similar between all sizes. However,
each burner top has different burner ports and log pin
configurations. See Figure 1 for log pin locations.
The log pins, along with the indentations in the Hearth
components, will aid in correctly positioning the two rear
logs and small burner log. The indentations in the hearths
are shown in Figure 4.
SL-5
SL-7
SL-9
LOG PINS
EMBERS
Figure 1. Log Pin and Glowing Ember Locations
CAUTION:
Logs are fragile, handle with care.
Install Logs
Figure 2. Example of Log Pin Holes
Figure 3. Log Assembly Components
Log Placement Tips
• The rear left log, rear right log and small burner
log utilize holes in the bottom side of the logs
that correspond to the locator pins on the burner.
Reference Figure 1 and Figure 2.
Additionally, the rear left log and rear right log are
located by visually aligning the bottom edge of the
log with the indentations in the left and right hearth
components. See Figure 4.
• Top left and top right logs, which lay across the rear
left and rear right logs, utilize the “indentations” in the
rear left and rear right logs for proper placement. See
Figure 6.
REAR RIGHT LOG
REAR LEFT LOG
BURNER LOG
TOP LEFT LOG
TOP RIGHT LOG
LOG PIN HOLES
Note:
The bottom surface of the left and right rear logs is
intended to be flat. If excess material/flashing or debris is
present on the bottom surface of these logs, it should be
removed. Removal will ensure that the logs are stable on
the burner and adjacent hearth components.