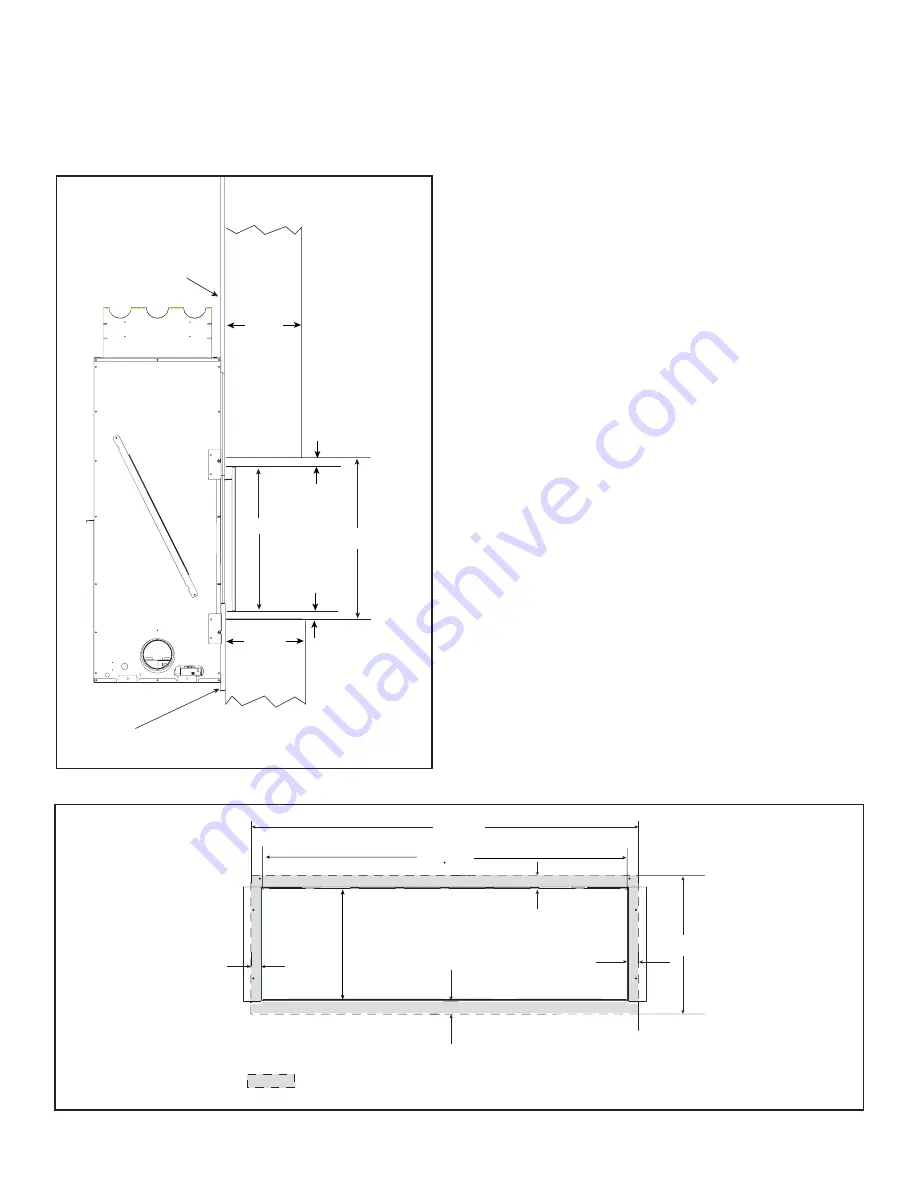
Heat & Glo • RED60 • 2159-900 Rev. B • 12/09
72
Figure 13.11 Noncombustible Surface Finishing Material 0-4 Inches Thick-Inside Fit Method
The mesh decorative front is approved for inside fi t ap-
plications. Non-combustible fi nishing materials up to 4
inches thick can be installed around the Mesh front (left,
right, top, and bottom). See Figure 13.10.
Figure 13.10 Inside Fit Method
Non-Combustible Finish Materials
0 Inches to 4 Inches Thick-Inside Fit Method
1/2 IN. THICK
WALL SHEATHING
0-4 IN.
20-1/2 IN.
0- 4 IN.
1/2 IN.
1/2 IN.
19-1/2 IN.
DRYWALL OR
EQUIVALENT (1/2 IN.)
1-11/16 IN.
1-11/16 IN.
20-1/2 IN.
1-3/8 IN.
1-3/8 IN.
65-1/2 IN.
FIREPLACE VIEWING AREA
= CLEARANCE FROM VIEWING AREA TO NON-COMBUSTIBLE FINISHING MATERIAL
(INSIDE FIT METHOD)
17-1/8 IN.
62-3/4 IN.
Ensure that no non-combustible fi nish materials are in-
stalled within 1-11/16 inches of top and bottom and 1-3/8
inches from right and left sides of fi replace opening. This
will ensure adequate clearance for required mesh front.
See Figure 13.11.
Refer to Section 1.E and 1.F of this manual for defi nition
and qualifi cations and defi nition of non-combustible and
combustible materials.