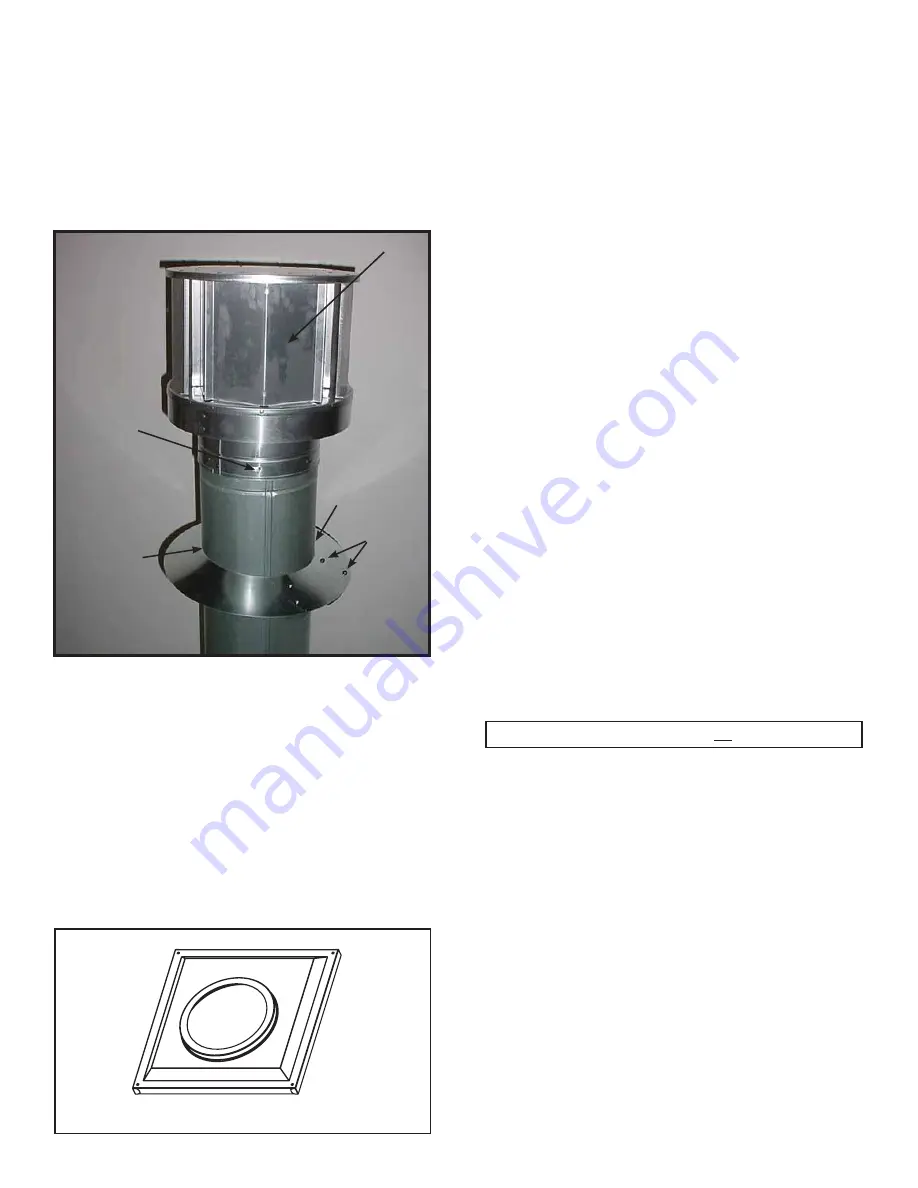
Heat & Glo • BE-41C / LP, BE-41IPIC / LP • 2105-900 Rev. P • 6/09
45
SCREWS
CAULK
STORM
COLLAR
(1 of 3)
Figure 10.18
Figure 10.18
TERMINATION CAP
I. Install Vertical Termination Cap
• Attach the vertical termination cap by sliding the inner
collar of the cap into the inner
fl
ue of the pipe section
while placing the outer collar of the cap over the outer
fl
ue of the pipe section.
• Secure the cap by driving three self-tapping screws
(supplied) through the pilot holes in the outer collar of the
cap into the outer
fl
ue of the pipe (see Figure 10.18).
J. Install Decorative Wall Components (SLP
only)
A decorative wall thimble can be installed on wall through
which the vent passes. The decorative wall thimble is used
to cover the wall shield
fi
restop.
• Slide the decorative wall thimble over the last section of
horizontal pipe before connecting the termination cap to
the pipe.
•
Once the pipe section and the termination cap have been
connected, slide the wall thimble up to the interior wall
surface and attach with screws provided. See Figure
10.19.
Important Notice:
Heat shields may not be
fi
eld constructed.
K. Heat Shield Requirements for Horizontal
Termination
WARNING! Risk of Fire! To prevent overheating and fi re,
heat shields must extend through the entire wall thick-
ness.
• DO NOT remove the heat shields attached to the
wall shield fi restop and the horizontal termination cap
(shown in Figure 10.20).
• Heat shields must overlap 1-1/2 in. (38 mm) mini-
mum.
There are two sections of the heat shield. One section
is factory-attached to the wall shield
fi
restop. The other
section is factory-attached to the cap. See Figure 10.20.
If the wall thickness does not allow the required 1-1/2 in.
(38 mm) heat shield overlap when installed, an extended
heat shield must be used.
• If the wall thickness is less than 4 in./102 mm (DVP)
or 4-3/8 in./ 111 mm (SLP), the heat shields on the cap
and wall shield
fi
restop must be trimmed. A minimum
1-1/2 in. (38 mm) overlap MUST be maintained.
• Use an extended heat shield if the
fi
nished wall thickness
is greater than 7-1/4 in. (184 mm).
• The extended heat shield may need to be cut to length
maintaining suf
fi
cient length for a 1-1/2 in. (38 mm)
overlap between heat shields.
• Attach the extended heat shield to either of the existing
heat shields using the screws supplied with the extended
heat shield. Refer to vent components diagrams in the
back of this manual.
• Rest the small leg on the extended heat shield on top
of the pipe section to properly space it from the pipe
section.
Figure 10.19 Wall Thimble