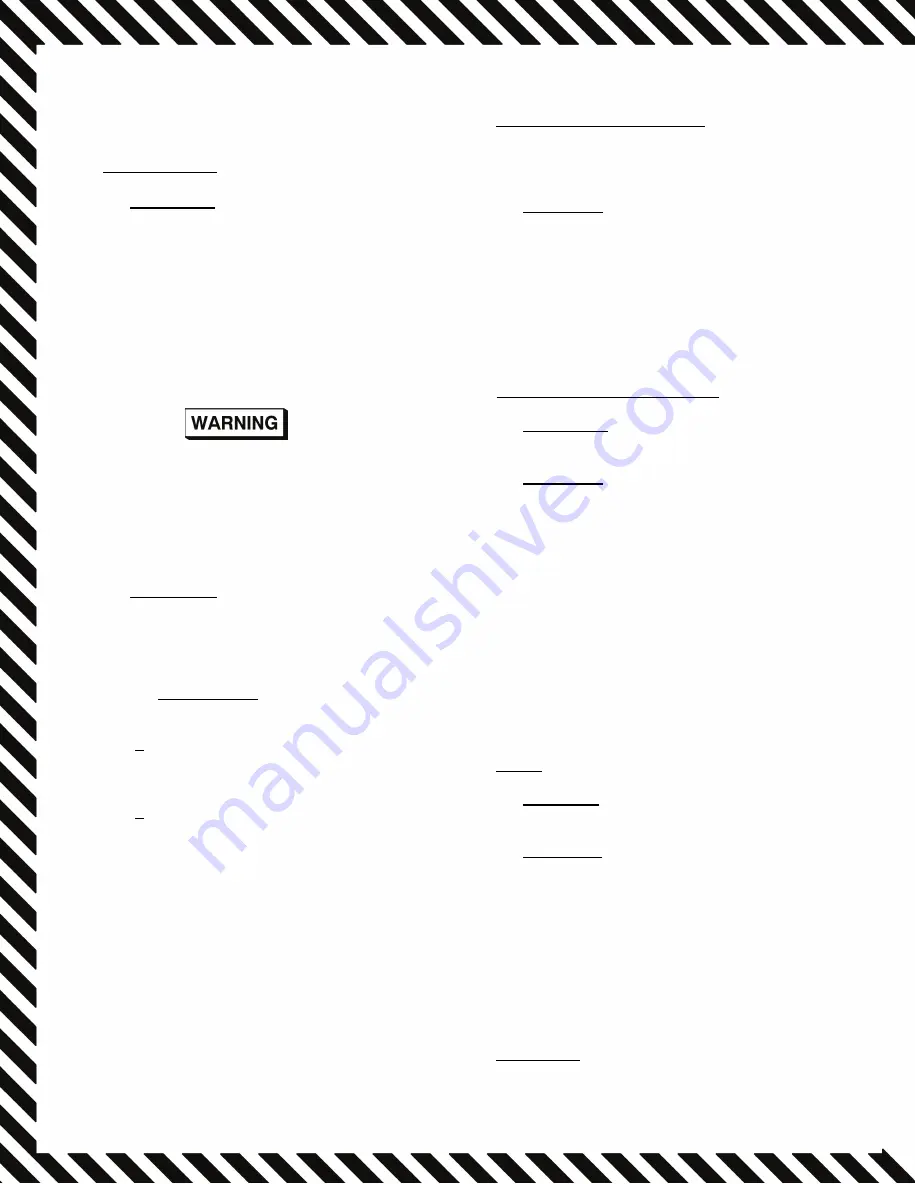
system, such as a severed driveshaft, causing the tail
rotor to lose power.
a. Powered Flight.
(1) Indications:
(a)
Abnormal vibrations.
(b)
Pedal input has no effect on helicopter
trim.
(c)
Nose of the helicopter turns to the right
(left sideslip).
(d)
Left roll of the fuselage along the longitu-
dinal axis.
Degree of roll and sideslip may be varied by
varying throttle and/or collective (At airspeeds
below 40 knots in powered
fl
ight, the sideslip
may become uncontrollable, and the helicopter
will begin to spin on the vertical axis. Autorota-
tion may be the only option).
(2) Procedures.
(a)
Continue powered
fl
ight, if possible, to a
suitable landing area at or above minimum rate of de-
scent airspeed.
(b)
AUTOROTATE when landing area is
reached.
1
If a run-on landing is possible, complete
autorotation with a touchdown airspeed as required for
directional control.
2
If a run-on landing is not possible, start
to decelerate from about 75 feet altitude, so that for-
ward ground speed is at a minimum when the helicopter
reaches 10 to 20 feet. Execute touchdown with a rapid
collective pull just prior to touchdown in a level attitude
with minimum ground speed.
b.
Deleted.
9-20. FIXED PITCH SETTINGS.
This is a malfunc-
tion involving a loss of control resulting in a
fi
xed pitch
setting. Whether the nose of the helicopter yaws left or
right is dependent upon the amount of pedal applied at
the time of the malfunction. Regardless of pedal setting
at the time of malfunction, a varying amount of tail rotor
thrust will be delivered at all times during
fl
ight.
a. Reduced power (low torque).
(1)
Indications: The nose of the helicopter will
turn right when power is applied.
(2) Procedure:
(a)
If helicopter control can be maintained in
powered
fl
ight, the best solution is to maintain control
with power and accomplish a run-on landing as soon as
practicable.
(b)
If helicopter control cannot be main-
tained, close the throttle immediately and accomplish
an autorotational landing.
b. Increased power (high torque).
(1) Indications:
The nose of the helicopter will
turn left when power is reduced.
(2) Procedure:
(a)
Maintain control with power and air-
speed. (Between 40 and 70 knots.)
(b)
If needed, reduce engine RPM manually
to 98%.
(c)
Continue powered
fl
ight to a suitable
landing area where a run-on landing can be accom-
plished.
(d)
Execute a run-on landing with power and
a touchdown speed which will minimize sideslip. Use
throttle and collective, as necessary, to control sideslip
and heading.
c. Hover.
(1) Indication:
Helicopter heading cannot be
controlled with pedals.
(2) Procedure.
(a)
Fixed pedal - Land.
(b)
Loss of tail rotor thrust - Perform hovering
autorotation.
9-21. LOSS OF TAIL ROTOR COMPONENTS.
The
severity of this situation is dependent upon the amount
of weight lost. Any loss of this nature will result in a
forward center of gravity shift, requiring aft cyclic.
a. Indications:
9-8 Change 14
TM 55-1520-228-10
Summary of Contents for OH-58A
Page 2: ......
Page 5: ......
Page 6: ......
Page 10: ......
Page 12: ......
Page 18: ......
Page 19: ......
Page 20: ......
Page 21: ......
Page 22: ......
Page 23: ......
Page 24: ......
Page 26: ......
Page 28: ......
Page 30: ......
Page 32: ......
Page 34: ......
Page 53: ...TM 55 1520 228 10 Change 13 2 11 Figure 2 5 Principal Dimensions Sheet 1 of 2 ...
Page 56: ...TM 55 1520 228 10 Figure 2 7 Float Gear Equipped Helicopter 2 14 ...
Page 57: ...TM 55 1520 228 10 Figure 2 8 Locking Devices for Doors 2 15 ...
Page 59: ...TM 55 1520 228 10 2 17 Figure 2 9 WSPS Configuration ...
Page 61: ...TM 55 1520 228 10 Change 11 2 19 FIGURE 2 10 HAS BEEN DELETED ...
Page 62: ...TM 55 1520 228 10 2 20 Change 11 Figure 2 11 Engine ...
Page 64: ...TM 55 1520 228 10 Figure 2 12 Overhead Console 2 22 Change 10 ...
Page 66: ......
Page 69: ...TM 55 1520 228 10 2 25 Figure 2 13 Instrument Panel and Console Typical A ...
Page 70: ...TM 55 1520 228 10 2 26 Change 11 Figure 2 14 Instrument Panel and Console Typical C ...
Page 75: ...TM 55 1520 228 10 Figure 2 15 Auxiliary Fuel System 2 29 ...
Page 84: ...TM 55 1520 228 10 Figure 2 17 Heater Control and Vent Pull Knobs 2 38 Change 12 ...
Page 92: ...TM 55 1520 228 10 Figure 2 18 1 AAU 32 A Altitude Encode Pneumatic Altimeter 2 46 Change 4 ...
Page 95: ...TM 55 1520 228 10 Change 11 2 47 Figure 2 19 Warning and Caution Panels ...
Page 98: ...TM 55 1520 228 10 Figure 2 20 Servicing Diagram Sheet 2of 2 2 50 Change 11 ...
Page 107: ...TM 55 1520 228 10 Figure 2 22 Gravity Refueling With Closed Circuit Receiver 2 59 ...
Page 109: ...TM 55 1520 228 10 Change 11 2 61 Figure 2 23 Refueling Receptacle ...
Page 116: ......
Page 133: ...TM 55 1520 228 10 Change 11 3 13 FIGURE 3 7 HAS BEEN DELETED ...
Page 146: ......
Page 152: ...TM 55 1520 228 10 FIGURE 3 15 HAS BEEN DELETED 3 30 Change 10 ...
Page 157: ...TM 55 1520 228 10 3 32 3 ...
Page 164: ......
Page 166: ......
Page 168: ...TM 55 1520 228 10 Figure 5 1 Instrument Markings A 5 2 Change 11 ...
Page 169: ......
Page 170: ...TM 55 1520 228 10 Figure 5 2 Instrument Markings Sheet 1 of 3 5 3 blank 5 4 Change 14 ...
Page 171: ...TM 55 1520 228 10 Change 11 5 5 Figure 5 2 Instrument Markings Sheet 2 of 3 ...
Page 175: ...TM 55 1520 228 10 Change 11 5 9 T63 A 720 Figure 5 3 Airspeed Operating Limits Chart ...
Page 182: ...TM 55 1520 228 10 6 4 Change 10 Figure 6 3 Cargo Space ...
Page 183: ...TM 55 1520 228 10 Change 11 6 5 Figure 6 4 Fuel Loading Chart ...
Page 184: ...TM 55 1520 228 10 6 6 Figure 6 5 Personnel Loading ...
Page 186: ......
Page 187: ......
Page 188: ......
Page 190: ......
Page 204: ...TM 55 1520 228 10 Figure 7 12 Torque Available Continuous Operation Chart Sheet 1 of 4 7 52 ...
Page 205: ...TM 55 1520 228 10 Figure 7 12 Torque Available Continuous Operation Chart Sheet 2 of 4 7 53 ...
Page 206: ...TM 55 1520 228 10 Figure 7 12 Torque Available Continuous Operation Chart Sheet 3 of 4 7 54 ...
Page 209: ......
Page 210: ......
Page 211: ...TM 55 1520 228 10 Change 10 7 59 Figure 7 13 Hover Chart Sheet 3 of 3 ...
Page 213: ......
Page 215: ...TM 55 1520 228 10 Figure 7 15 Cruise Chart Sheet 1 of 13 7 63 ...
Page 216: ...TM 55 1520 228 10 Figure 7 15 Cruise Chart Sheet 2 of 13 7 64 ...
Page 217: ...TM 55 1520 228 10 Figure 7 15 Cruise Chart Sheet 3 of 13 7 65 ...
Page 218: ...TM 55 1520 228 10 Figure 7 15 Cruise Chart Sheet 4 of 13 7 66 ...
Page 219: ...TM 55 1520 228 10 Figure 7 15 Cruise Chart Sheet 5 of 13 7 67 ...
Page 220: ...TM 55 1520 228 10 Figure 7 15 Cruise Chart Sheet 6 of 13 7 68 ...
Page 221: ...TM 55 1520 228 10 Figure 7 15 Cruise Chart Sheet 7 of 13 7 69 ...
Page 222: ...TM 55 1520 228 10 Figure 7 15 Cruise Chart Sheet 8 of 13 7 70 ...
Page 223: ...TM 55 1520 228 10 Figure 7 15 Cruise Chart Sheet 9 of 13 7 71 ...
Page 224: ...TM 55 1520 228 10 Figure 7 15 Cruise Chart Sheet 10 of 13 7 72 ...
Page 225: ...TM 55 1520 228 10 Figure 7 15 Cruise Chart Sheet 11 of 13 7 73 ...
Page 226: ...TM 55 1520 228 10 Figure 7 15 Cruise Chart Sheet 12 of 13 7 74 ...
Page 227: ...TM 55 1520 228 10 Figure 7 15 Cruise Chart Sheet 13 of 13 7 75 ...
Page 231: ...TM 55 1520 228 10 7 79 Figure 7 17 Climb Descent Chart C ...
Page 233: ......
Page 234: ......
Page 235: ......
Page 237: ...TM 55 1520 228 10 Figure 7 19 Idle Fuel Flow Chart 7 85 7 86 blank ...
Page 238: ......
Page 242: ...TM 55 1520 228 10 8 4 Change 10 Figure 8 1 Exterior Check Diagram ...
Page 256: ......
Page 259: ...Figure 9 1 Emergency Exits and Equipment Sheet 1 of 2 Change 14 9 3 TM 55 1520 228 10 ...
Page 260: ...Figure 9 1 Emergency Exits and Equipment Sheet 2 of 2 9 4 Change 14 TM 55 1520 228 10 ...
Page 261: ...Figure 9 2 Autorotational Glide Characteristics Chart Change 14 9 5 TM 55 1520 228 10 ...
Page 268: ...SECTION II MISSION EQUIPMENT NOT APPLICABLE 9 12 Change 14 TM 55 1520 228 10 ...
Page 270: ......
Page 282: ......
Page 284: ......
Page 286: ......
Page 292: ...PIN 014142 000 ...