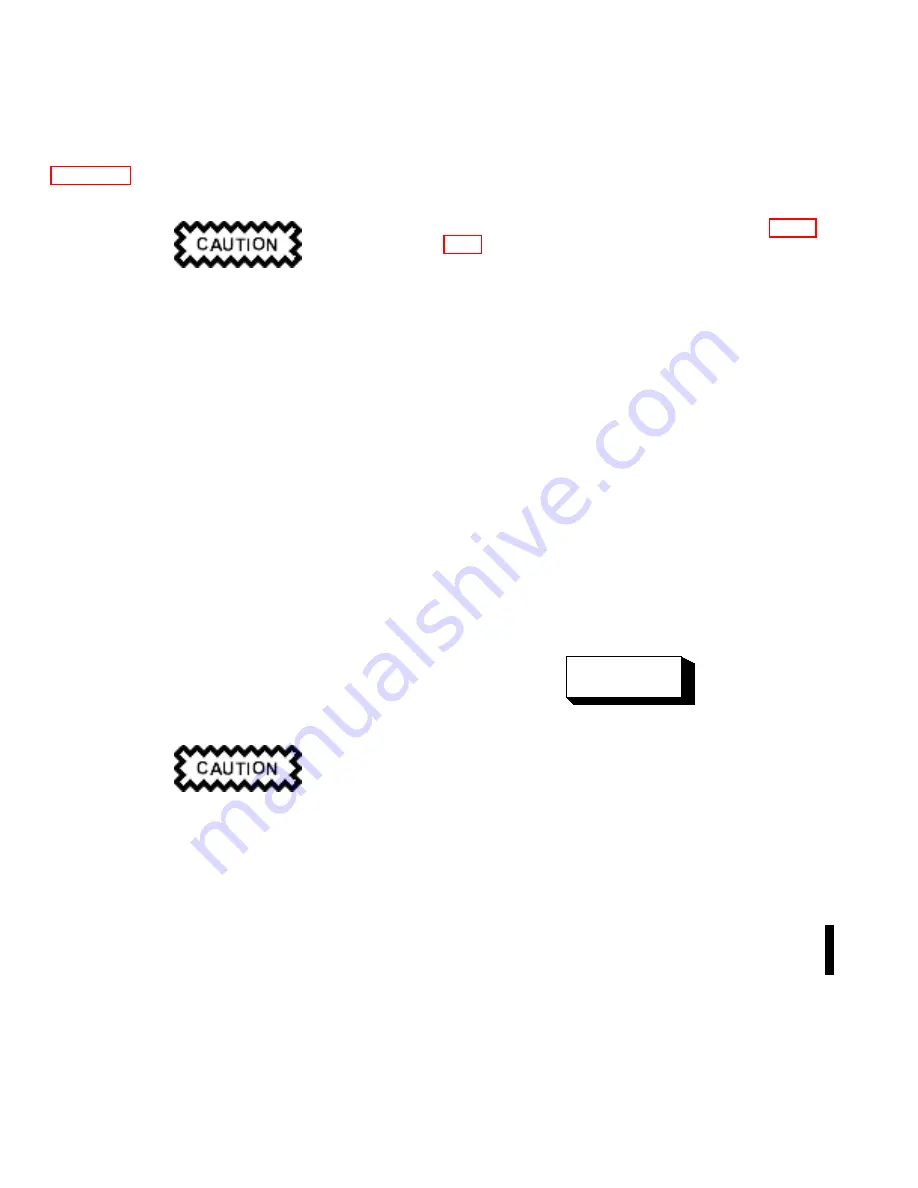
TM 55-1520-228-10
(2)
Ensure that gravity refueling port is
closed. If not, rotate inner sleeve counterclockwise until
gravity refueling port is closed and flange of sleeve is in
contact with rivet at base or receiving cylinder. Refer to
figure 2-23.
Ensure that servicing unit pressure is not above
125 PSI while refueling.
(3)
Insert fueling nozzle into receiver and ac-
tuate automatic nozzle lever to ON or FLOW position.
Pin at base of nozzle will momentarily indicate when fuel
flow stops.
(4)
Fuel flow will automatically shut off when
normal fuel level is reached. Just prior to normal shut off,
fuel flow may cycle several times as fuel level is reached.
Gage on servicing unit will indicate when flow is stopped.
(5)
When fuel flow has stopped, actuate lever
on nozzle to OFF, disconnect nozzle from receiver and
replace filler cap.
(6)
Disconnect fuel nozzle ground and rewind
hose assembly.
(7)
Disconnect servicing unit ground at heli-
copter.
(8)
Disconnect
servicing
unit
ground
at
grounding stake.
If helicopter is equipped with closed circuit
refueling system and fuel servicing unit is not
equipped with related nozzle for closed circuit
refuelling, a gravity system may be used pro-
viding the servicing nozzle does not exceed
1.75 inches outside diameter. To refuel utilizing
the gravity nozzle, it is necessary to position
the inner sleeve of receiver until slot is lined
up with fuel port in bottom of receiver. Position
nozzle into port in order to bypass closed cir-
cuit refueling system if caution is not used to
prevent damage to inner sleeve of receiver at
fuel port through improper use of nozzle.
d.
Gravity Refueling.
(1)
Ground the helicopter at the receptacle lo-
cated adjacent to the filler cap on the helicopter to the
filler-nozzle and remove filler cap.
(2)
Rotate inner sleeve clockwise until sleeve
clears port in bottom of fuel receiver. Refer to figure
2-23.
(3)
Position nozzle into port of fuel receiver.
(4)
Fill to specified level.
(5)
Remove nozzle and rotate inner sleeve
counterclockwise until gravity refueling port is closed
and flange of inner sleeve is in contact with rivet at base
of receiver cylinder.
(6)
Reinstall filler cap.
(7)
Disconnect fuel nozzle ground and rewind
hose.
(8)
Disconnect servicing unit ground at heli-
copter.
(9)
Disconnect
servicing
unit
ground
at
grounding stake.
2-78.
FUEL SYSTEM SERVICING. (RAPID (HOT)
REFUELING).
WARNING
When it is determined that rapid (hot) refuel-
ing is required (prescribed in FM 10–68), proper
grounding of aircraft must be accomplished.
a.
Precautions.
NOTE
Servicing personnel shall comply with all safety
precautions and procedures in FM 10–68.
NOTE
If the nozzles do not reduce the fuel pressure to
less than 25.5 PSIG, the receiver is designed to
shut off fuel flow.
(1)
Ground the helicopter at the receptacle lo-
cated adjacent to the filler cap on the helicopter to the
filler-nozzle before removing filler cap.
Change 12
Summary of Contents for OH-58A
Page 2: ......
Page 5: ......
Page 6: ......
Page 10: ......
Page 12: ......
Page 18: ......
Page 19: ......
Page 20: ......
Page 21: ......
Page 22: ......
Page 23: ......
Page 24: ......
Page 26: ......
Page 28: ......
Page 30: ......
Page 32: ......
Page 34: ......
Page 53: ...TM 55 1520 228 10 Change 13 2 11 Figure 2 5 Principal Dimensions Sheet 1 of 2 ...
Page 56: ...TM 55 1520 228 10 Figure 2 7 Float Gear Equipped Helicopter 2 14 ...
Page 57: ...TM 55 1520 228 10 Figure 2 8 Locking Devices for Doors 2 15 ...
Page 59: ...TM 55 1520 228 10 2 17 Figure 2 9 WSPS Configuration ...
Page 61: ...TM 55 1520 228 10 Change 11 2 19 FIGURE 2 10 HAS BEEN DELETED ...
Page 62: ...TM 55 1520 228 10 2 20 Change 11 Figure 2 11 Engine ...
Page 64: ...TM 55 1520 228 10 Figure 2 12 Overhead Console 2 22 Change 10 ...
Page 66: ......
Page 69: ...TM 55 1520 228 10 2 25 Figure 2 13 Instrument Panel and Console Typical A ...
Page 70: ...TM 55 1520 228 10 2 26 Change 11 Figure 2 14 Instrument Panel and Console Typical C ...
Page 75: ...TM 55 1520 228 10 Figure 2 15 Auxiliary Fuel System 2 29 ...
Page 84: ...TM 55 1520 228 10 Figure 2 17 Heater Control and Vent Pull Knobs 2 38 Change 12 ...
Page 92: ...TM 55 1520 228 10 Figure 2 18 1 AAU 32 A Altitude Encode Pneumatic Altimeter 2 46 Change 4 ...
Page 95: ...TM 55 1520 228 10 Change 11 2 47 Figure 2 19 Warning and Caution Panels ...
Page 98: ...TM 55 1520 228 10 Figure 2 20 Servicing Diagram Sheet 2of 2 2 50 Change 11 ...
Page 107: ...TM 55 1520 228 10 Figure 2 22 Gravity Refueling With Closed Circuit Receiver 2 59 ...
Page 109: ...TM 55 1520 228 10 Change 11 2 61 Figure 2 23 Refueling Receptacle ...
Page 116: ......
Page 133: ...TM 55 1520 228 10 Change 11 3 13 FIGURE 3 7 HAS BEEN DELETED ...
Page 146: ......
Page 152: ...TM 55 1520 228 10 FIGURE 3 15 HAS BEEN DELETED 3 30 Change 10 ...
Page 157: ...TM 55 1520 228 10 3 32 3 ...
Page 164: ......
Page 166: ......
Page 168: ...TM 55 1520 228 10 Figure 5 1 Instrument Markings A 5 2 Change 11 ...
Page 169: ......
Page 170: ...TM 55 1520 228 10 Figure 5 2 Instrument Markings Sheet 1 of 3 5 3 blank 5 4 Change 14 ...
Page 171: ...TM 55 1520 228 10 Change 11 5 5 Figure 5 2 Instrument Markings Sheet 2 of 3 ...
Page 175: ...TM 55 1520 228 10 Change 11 5 9 T63 A 720 Figure 5 3 Airspeed Operating Limits Chart ...
Page 182: ...TM 55 1520 228 10 6 4 Change 10 Figure 6 3 Cargo Space ...
Page 183: ...TM 55 1520 228 10 Change 11 6 5 Figure 6 4 Fuel Loading Chart ...
Page 184: ...TM 55 1520 228 10 6 6 Figure 6 5 Personnel Loading ...
Page 186: ......
Page 187: ......
Page 188: ......
Page 190: ......
Page 204: ...TM 55 1520 228 10 Figure 7 12 Torque Available Continuous Operation Chart Sheet 1 of 4 7 52 ...
Page 205: ...TM 55 1520 228 10 Figure 7 12 Torque Available Continuous Operation Chart Sheet 2 of 4 7 53 ...
Page 206: ...TM 55 1520 228 10 Figure 7 12 Torque Available Continuous Operation Chart Sheet 3 of 4 7 54 ...
Page 209: ......
Page 210: ......
Page 211: ...TM 55 1520 228 10 Change 10 7 59 Figure 7 13 Hover Chart Sheet 3 of 3 ...
Page 213: ......
Page 215: ...TM 55 1520 228 10 Figure 7 15 Cruise Chart Sheet 1 of 13 7 63 ...
Page 216: ...TM 55 1520 228 10 Figure 7 15 Cruise Chart Sheet 2 of 13 7 64 ...
Page 217: ...TM 55 1520 228 10 Figure 7 15 Cruise Chart Sheet 3 of 13 7 65 ...
Page 218: ...TM 55 1520 228 10 Figure 7 15 Cruise Chart Sheet 4 of 13 7 66 ...
Page 219: ...TM 55 1520 228 10 Figure 7 15 Cruise Chart Sheet 5 of 13 7 67 ...
Page 220: ...TM 55 1520 228 10 Figure 7 15 Cruise Chart Sheet 6 of 13 7 68 ...
Page 221: ...TM 55 1520 228 10 Figure 7 15 Cruise Chart Sheet 7 of 13 7 69 ...
Page 222: ...TM 55 1520 228 10 Figure 7 15 Cruise Chart Sheet 8 of 13 7 70 ...
Page 223: ...TM 55 1520 228 10 Figure 7 15 Cruise Chart Sheet 9 of 13 7 71 ...
Page 224: ...TM 55 1520 228 10 Figure 7 15 Cruise Chart Sheet 10 of 13 7 72 ...
Page 225: ...TM 55 1520 228 10 Figure 7 15 Cruise Chart Sheet 11 of 13 7 73 ...
Page 226: ...TM 55 1520 228 10 Figure 7 15 Cruise Chart Sheet 12 of 13 7 74 ...
Page 227: ...TM 55 1520 228 10 Figure 7 15 Cruise Chart Sheet 13 of 13 7 75 ...
Page 231: ...TM 55 1520 228 10 7 79 Figure 7 17 Climb Descent Chart C ...
Page 233: ......
Page 234: ......
Page 235: ......
Page 237: ...TM 55 1520 228 10 Figure 7 19 Idle Fuel Flow Chart 7 85 7 86 blank ...
Page 238: ......
Page 242: ...TM 55 1520 228 10 8 4 Change 10 Figure 8 1 Exterior Check Diagram ...
Page 256: ......
Page 259: ...Figure 9 1 Emergency Exits and Equipment Sheet 1 of 2 Change 14 9 3 TM 55 1520 228 10 ...
Page 260: ...Figure 9 1 Emergency Exits and Equipment Sheet 2 of 2 9 4 Change 14 TM 55 1520 228 10 ...
Page 261: ...Figure 9 2 Autorotational Glide Characteristics Chart Change 14 9 5 TM 55 1520 228 10 ...
Page 268: ...SECTION II MISSION EQUIPMENT NOT APPLICABLE 9 12 Change 14 TM 55 1520 228 10 ...
Page 270: ......
Page 282: ......
Page 284: ......
Page 286: ......
Page 292: ...PIN 014142 000 ...