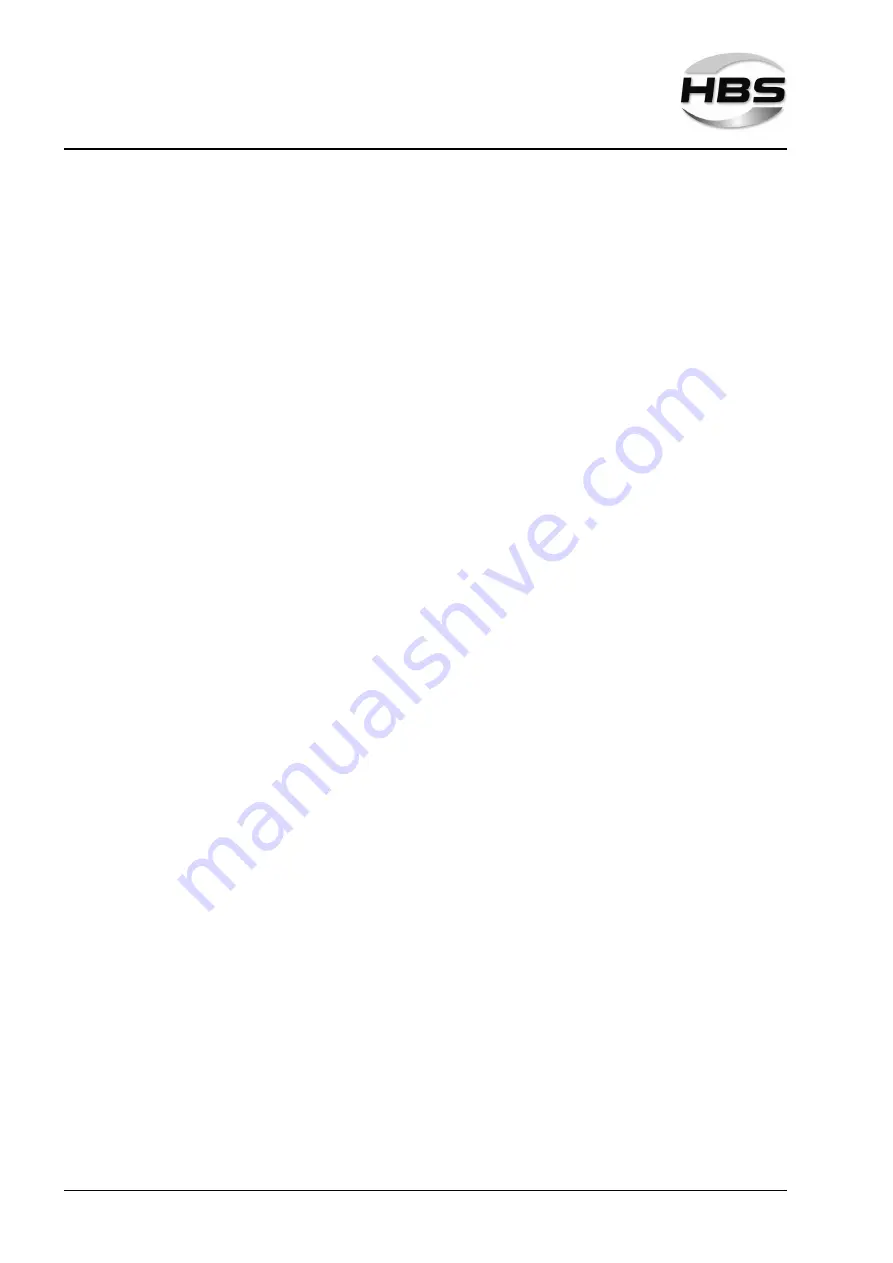
©HBS Bolzenschweiss-Systeme GmbH & Co. KG
All rights reserved – Reprinting, in whole or in part, only with the approval of the manufacturer
16
7 Warranty
7 Warranty
Please refer to the latest "General Terms and Conditions" for the scope of the
warranty.
The warranty does not cover faults caused by e.g.
– Normal wear,
– Improper handling,
– Failure to observe the operating manual,
– Failure to observe the safety precautions,
– Use for other than the intended purpose, or
– Transport damage.
The
warranty claim will be voided if modifications, changes or service and repair
work is carried out by unauthorised persons. We expressly point out that only
spare parts and accessories or components approved by us may be used. The
same applies analogously to installed units from our sub-suppliers.
Summary of Contents for 93-10-1552A
Page 63: ......