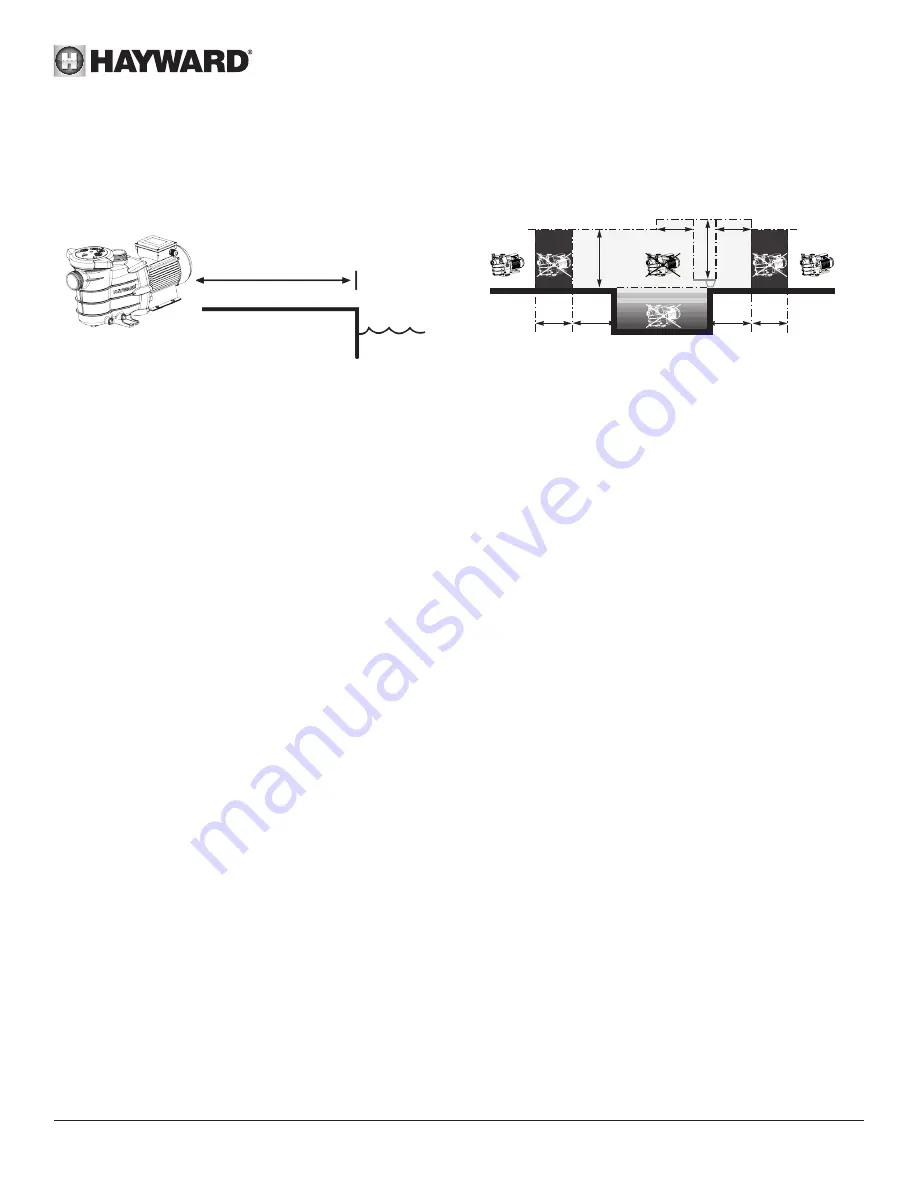
USE ONLY HAYWARD GENUINE REPLACEMENT PARTS
Page 3 of 5
Power-Flo II
Rev. B
GENERAL
Install the pump at the right distance from the base in to minimize the distance between the suction point and the pump so
as to avoid pointless and excessive load losses in the hydraulic circuit.
However, it is mandatory to allow a safety distance (3.5 m minimum) as required by the current installation standard (p 2).
ZONE 2
ZONE 2
ZONE 0
1,50 m
2,50 m
2,50 m
1,50 m
2,00 m
2,00 m
1,50 m
ZONE 1
1,50 m
OK
OK
3,5 m
ZONE 0
Install the pump in a ventilated and dry place. The motor requires air to flow freely around it to provide for natural ventilation.
The pump has to be installed, so that the plug and the wall socket outlet is easily visible and accessible.
The pump has to be installed, so that the external disconnect switch which is incorporated in the fixed wiring is easily visible
and accessible. The switch has to be located close to the pump.
The pump must be permanently mounted to a concrete base using lag screws suitable for concrete where pilot holes have
been drilled. Locking washers must be supplied to prevent loosening of the mounting lag screws over time. If the pump is
to be mounted to a wooden deck then lag screws suitable for wood must be used - with lock washers to prevent loosening
over time.
The acoustic level of the Hayward pumps is lower than 70 dB (A).
Necessary arrangements :
•
Connect the pump to ground
•
Fit a 30 mA residual current (RCD) device to protect people from electric shock caused by a possible break in the
electrical insulation.
•
Provide protection against short-circuiting (the definition of the rating will depend on the value indicated on the motor
name plate).
•
Provide a circuit separation device with a 3 mm opening on all the poles.
The single phase motors fitted to our pumps are provided with thermal protection. This protection operates on an overload
or in the event of abnormal heating of the motor coil and is reset automatically when the winding temperature drops.
If so required by regulations and whatever the motor type, in addition to the devices mentioned above, it is also necessary
to install a thermomagnetic protective device calibrated in accordance with the indications on the motor name-plate.
The table on page 42 indicates the various characteristics of the motors fitted to our pumps.
ELECTRICAL CONNECTION
Make sure that the power supply voltage required by the motor corresponds to that of the distribution network and that the
power supply cables matches the power and current of the pump.
All the electric connections of the pump and the possible change of power supply cable must be done by a qualified
professional so as to avoid all possible danger.
When making these electrical connections, refer to the diagram given under the lid of the motor terminal box.
Be sure to check the electric connections are tight and sealed before powering up. Replace all covers before operation.
The pre-wiring (test leads) that might be included on some of the pumps must be removed for final connection of the pump to the
electric power supply. This pre-equipment (test leads) is only used for works testing during the manufacturing phases.