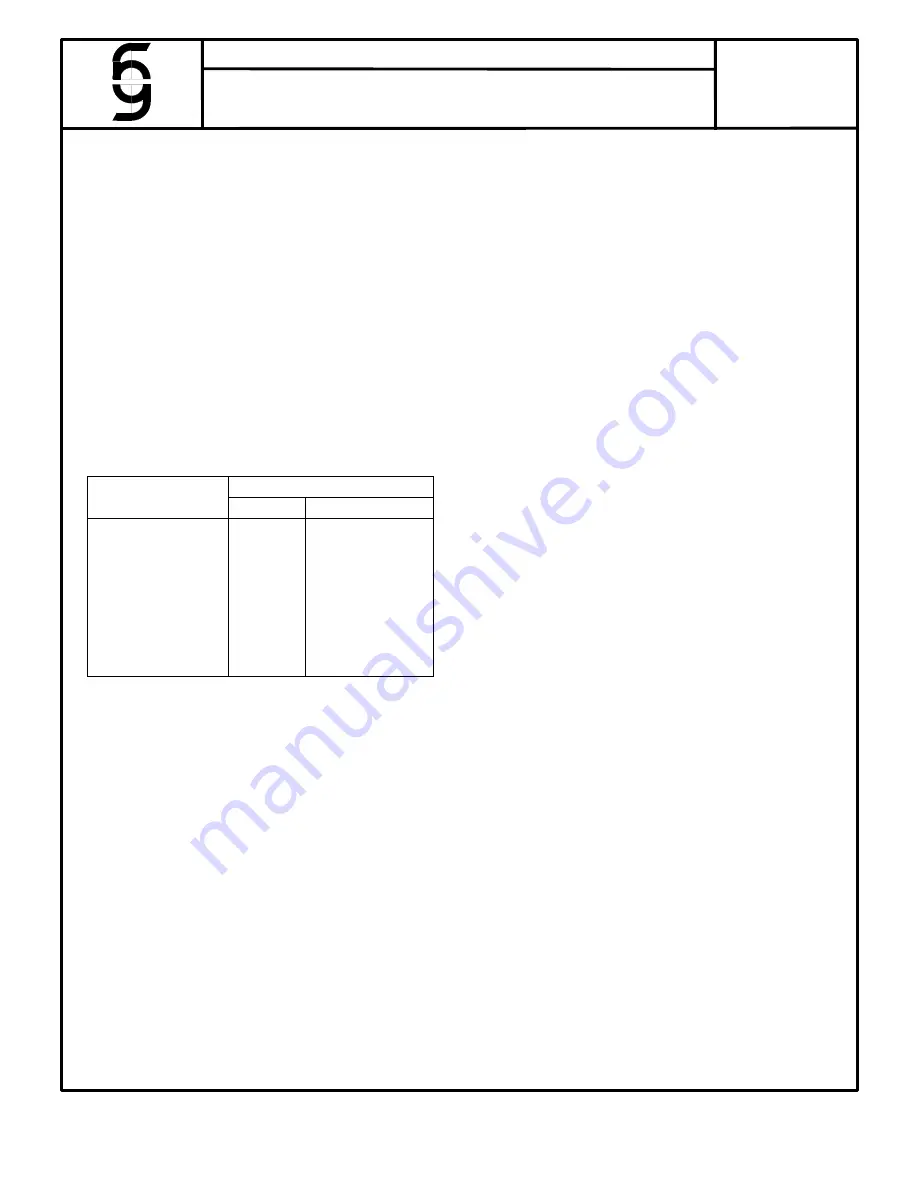
HAYWARD GORDON LTD
Page
8
Rev:
1
HRF Series Mixers
Date 11/99
Section: RF
Hayward Gordon produces a variety of impeller designs for a broad range of mixing applications.
The impeller assembly normally consists of two parts: the hub, which is fastened to the shaft by
means of a pinned key, and blades, which are bolted to the hub ears ( pg. 15 ).
Mixers are normally shipped with the hub(s) mounted on the mixer shaft and blades shipped
separately. Impellers which are designed to turn at speeds higher than 100 RPM will be match
marked at the factory - ensure that match marks are located and assembled accordingly.
In-tank fasteners are supplied either with lock washers or double nuts. Care should be taken to
see that locking devices are properly installed and bolts properly tightened.
It is recommended that all in-tank fasteners be rechecked for tightness after the first 1500
hours of operation and subsequently at each shutdown period.
Table III gives torque values to which all shaft and impeller bolts should be tightened.
TABLE III
Thread
Torque Values (ft.-lbs.)
Size
Dry
Lubricated
¼”-20UNC
5/16”-18 UNC
3/8”-16 UNC
½”-13 UNC
5/8”-11 UNC
¾”-10 UNC
7/8”-9 UNC
1”-8 UNC
6
12
20
55
110
180
260
350
4.5
9.5
15
40
85
135
200
270