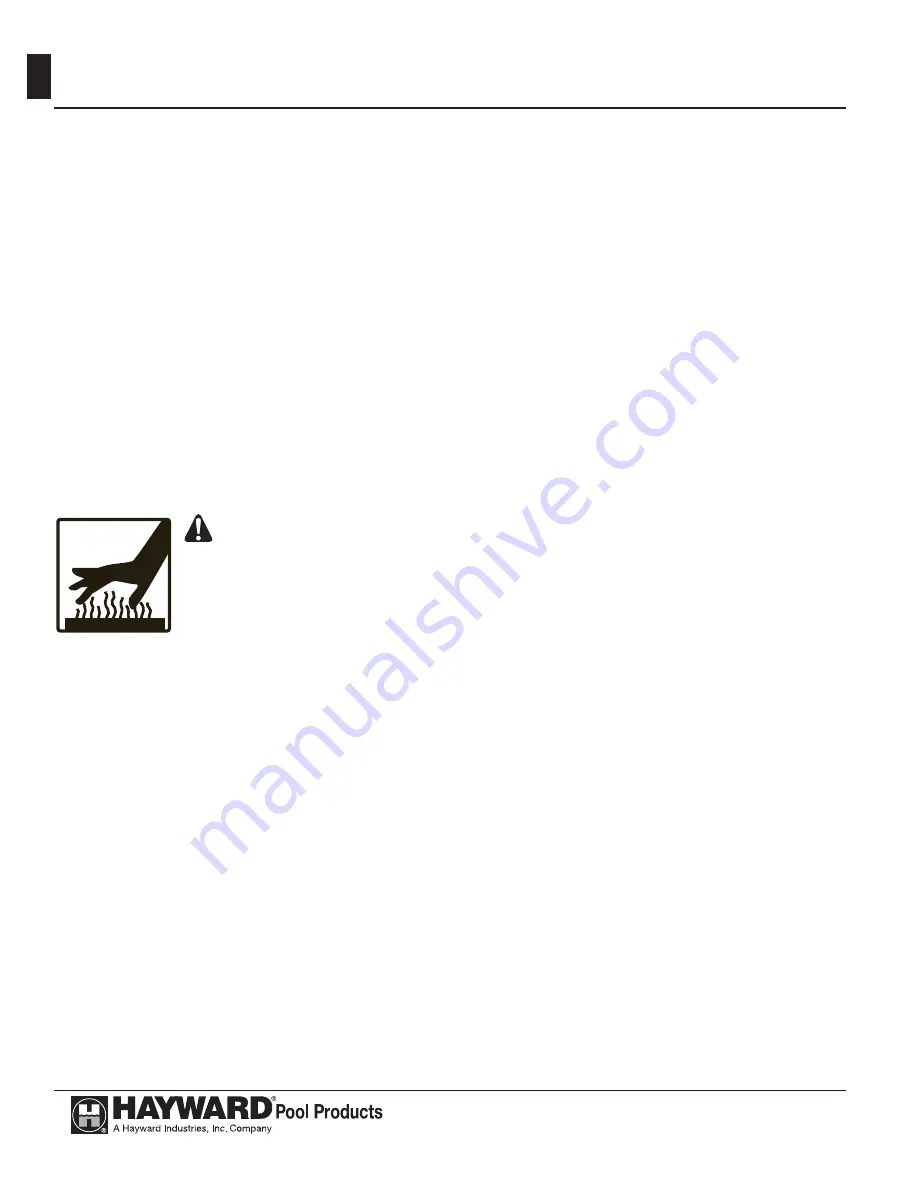
Pomona, CA Clemmons, NC Nashville, TN
Tel: 908-351-5400 www.haywardpool.com
USE ONLY HAYWARD GENUINE REPLACEMENT PARTS
8
ExTERNAL HEAT ExCHANGER INSPECTION AND CLEANING:
Remove the heater top and inspect the external surfaces of the heat exchanger for soot accumulation. If
soot has accumulated it must be removed by following the recommended procedure.
1. Turn pump, main gas valve, and heater power “OFF”.
. Remove the trim panels at each end of the heater. Each is secured with () screws.
. Remove upper end caps on both ends of the heater. Each cap is attached with () screws, located
inside the “slots at the top and sides of the part.
. Remove the louvered top panel. There are () screws at each end of the top panel, and () screws
in back.
5. Remove the rain shield. There are (1) screws on the top surface of this panel.
6. Remove the flue collector side panels on both ends of the heater. Each panel is secured with (2)
screws that are accessed from the outside of the heater.
7. Remove the front access panel. It is secured with () screws.
8. Remove the control box cover. It is secured with () screws.
9. Disconnect the water pressure switch leads at the switch, which is located on the water header.
10. Disconnect the limit leads at each limit, which are located on the underside of the water header.
11. Disconnect the thermistor lead from the ignition control board
inside the control box. Pull it out of
the control box and free of the heater chassis.
1. Lift and remove the heat exchanger. Place it on a clean surface.
WARNING:
BURN HAZARD
Do not use
a wire brush to remove soot from the
heat exchanger. This could cause a spark and ignite the gases trapped within the soot.
Using a soft-tipped brush such a paintbrush apply a degreaser to the entire heat
exchanger surface top and bottom. Allow the heat exchanger to sit for a period of time
to allow the degreaser to loosen the soot. Wash the heat exchanger using a garden hose
ensuring both the top and bottom surfaces are cleaned. Follow the steps above in reverse order to reinstall the
heat exchanger. Although the heat exchanger should be cleaned of soot and reinstalled, the fact that sooting
occurred should be investigated, as it may indicate other problems such as:
• Insufficient air supply
• Inadequate venting
• High or low gas pressure
• Blockage of burner tubes or orifices
• Blockage of blower inlet
• Low voltage supply causing blower to “spin” slower
• Improper heater location installation
• Incorrect gas supply pipe size
• Excessive water flow through heat exchanger
• LP tank below 0% full
COMBUSTION CHAMBER:
The combustion chamber is a single-piece casting. If damaged, the entire chamber must be replaced.
HEAT ExCHANGER REMOVAL:
Follow steps 1-1 under “External
heat exchanger inspection and cleaning” in this section.