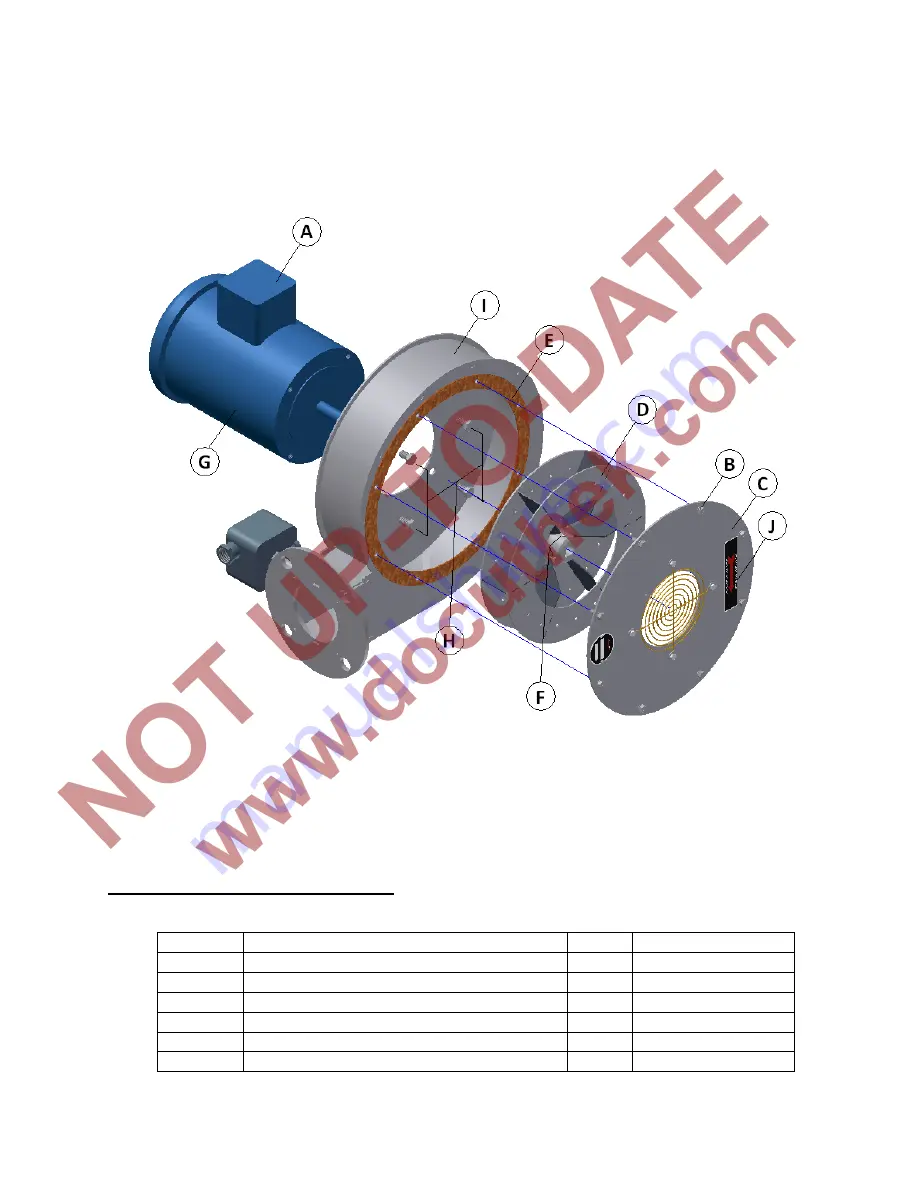
Page 14
PBG
-9
11. Prior to restarting the burner system refer to the following sections: Section H – Initial
Setup, Section I – Ignition, Section J – Operation, Section L – Maintenance.
Figure 4. Blower Assembly
M. RECOMMENDED SPARE PARTS
ITEM DESCRIPTION
QTY.
PART
NO.
1
Spark Igniter Assembly (If Applicable)
1
See Parts List
2
Flame Rod Assembly
1
See Parts List
3
UV Scanner (If Applicable)
1
84315205
4 Opticord
Adapter
1
74960437
5
GFK (NFPA Manifold)
1
See Parts List
6
OMG (If Applicable)
1
See Parts List