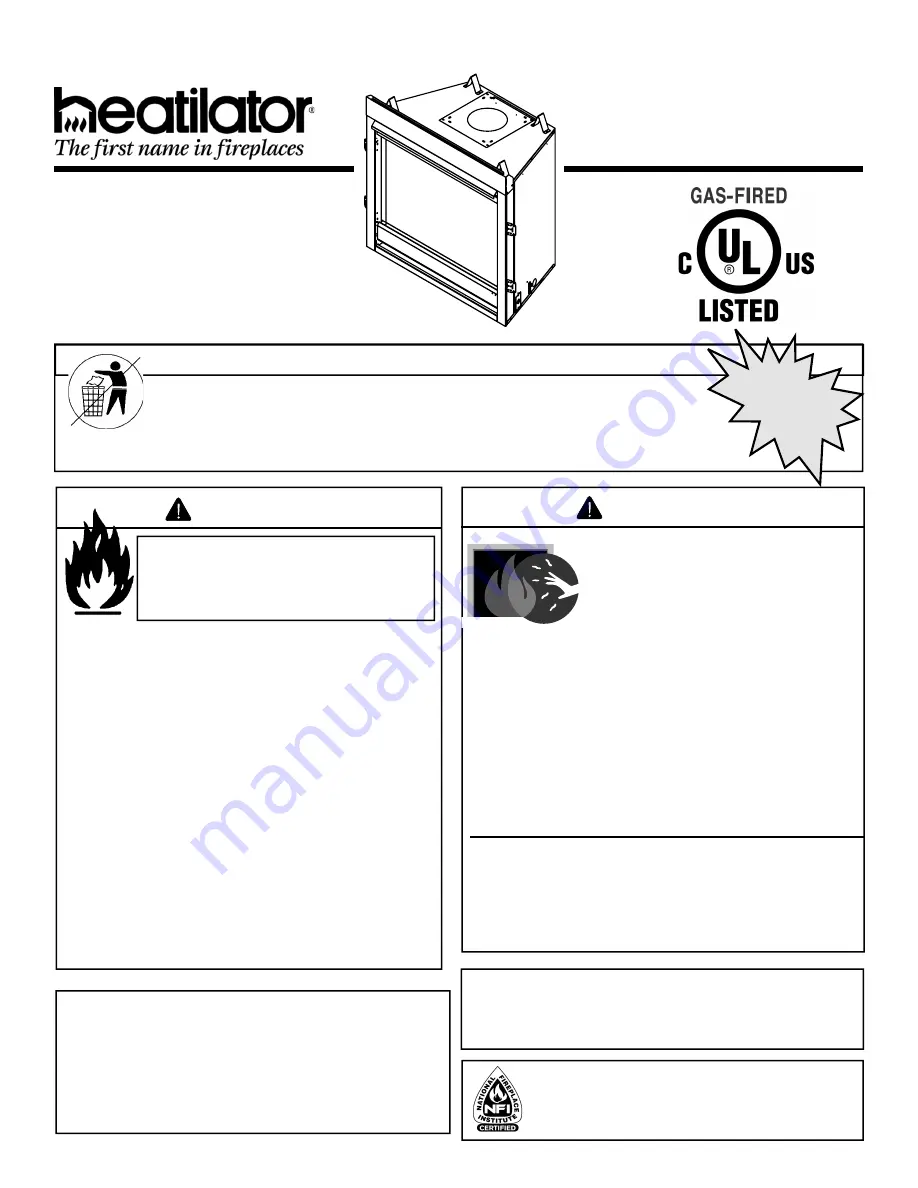
Heatilator • Caliber Mesh CD Series-SIT Valve • 4040-849 Rev H • 11/07
1
Owner’s Manual
Installation and Operation
Models:
CD4236MR
CD4842MR
CD4236MLR CD4842MLR
CD4236MIR
CD4842MIR
CD4236MILR CD4842MILR
Direct Vent Gas Appliance
This appliance may be installed as an OEM installation
in manufactured home (USA only) or mobile home and
must be installed in accordance with the manufacturer’s
instructions and the manufactured home construction and
safety standard,
Title 24 CFR, Part 3280
or
Standard for
Installation in Mobile Homes, CAN/CSA Z240MH.
This appliance is only for use with the type(s) of gas
indicated on the rating plate.
DO NOT DISCARD THIS MANUAL
CAUTION
• Important operating and
maintenance instructions
included.
•
Leave this manual with
party responsible for
use and operation.
•
Read, understand and follow
these instructions for safe
installation and operation.
DO
NOT
DISCARD
If the information in these instruc-
tions is not followed exactly, a
fi
re may result causing property
damage, personal injury, or death.
• Do not store or use gasoline or other
fl
am-
mable vapors and liquids in the vicinity of
this or any other appliance.
• What to do if you smell gas:
- Do not try to light any appliance.
- Do not touch any electrical switch. Do not
use any phone in your building.
- Immediately call your gas supplier from
a neighbor’s phone. Follow the gas
supplier’s instructions.
- If you cannot reach your gas supplier, call
the
fi
re department.
• Installation and service must be performed
by a quali
fi
ed installer, service agency, or
the gas supplier.
WARNING
Installation and service of this appliance should be performed
by quali
fi
ed personnel. Hearth & Home Technologies suggests
NFI certi
fi
ed or factory-trained professionals, or technicians
supervised by an NFI certi
fi
ed professional.
In the Commonwealth of Massachusetts installation must
be performed by a licensed plumber or gas
fi
tter;
See Table of Contents for location of additional
Commonwealth of Massachusetts requirements.
HOT SURFACES!
Glass and other surfaces are hot during
operation and cool down.
WARNING
• CAREFULLY SUPERVISE children in same room as
appliance.
• Alert children and adults to hazards of high
temperatures.
High temperatures may ignite clothing or other
fl
ammable materials.
• Keep clothing, furniture, draperies and other combustibles
away.
Hot glass will cause burns.
• Do not touch glass until it is cooled
• NEVER allow children to touch glass
• Keep children away
This appliance has been supplied with an integral
barrier to prevent direct contact with the
fi
xed glass
panel. Do NOT operate the appliance with the barrier
removed.
Contact your dealer or Hearth & Home Technologies if the
barrier is not present or help is needed to properly install one.
¨