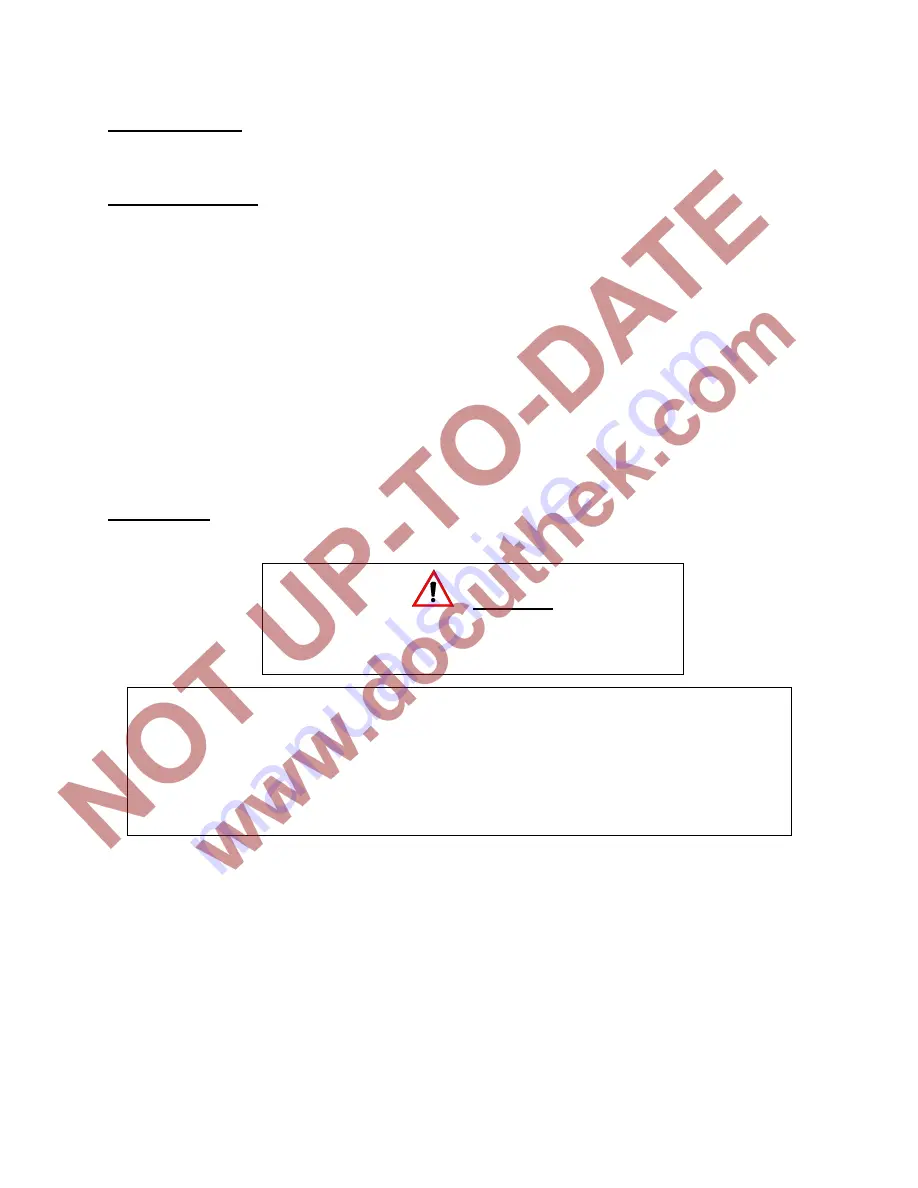
Page 6
IPG-9
WARNING
Adjustment of this equipment by unqualified personnel
can result in fire, explosion, severe personal injury, or
even death.
D. DIMENSIONS
See appropriate Dimension sheet for detailed dimensional information.
E. INSTALLATION
1. Ensure that all components of the factory assembled pilot are present and properly
connected.
The pilot unit consists of a low pressure gas regulator, air ball valve, gas ball
valve,
gas mixer, pilot nozzle assembly, union (threaded pilots only), and flexible pipe nipple.
2. Install the pilot assembly in the air and gas lines. The gas pressure regulator is used as a
zero
governor and is suitable for any mounting position without restriction.
a. Connect the air piping to the inlet side of the air ball valve. Low pressure air should be
supplied at a constant pressure ranging from 14 - 55 in.w.c. (3.5 - 13.7 kPa) at the inlet
of the ball valve.
b. Connect the gas piping to the inlet side of the gas ball valve. Low pressure gas should
be supplied at approximately 14 in.w.c. (3.5 kPa) at the inlet of the regulator. The
regulator is designed to operate from 13.9 - 27.7 in.w.c. (3.4 - 6.9 kPa); maximum
allowable inlet pressure is 27.7 in.w.c. (6.9 kPa).
c. Ensure that the air and gas ball valves are fully closed.
F. IGNITION
1. Be sure the spark plug is set as shown in Figure 1. Ideally, initial pilot set-up should be done
with the pilot outside of the burner.
2. Connect a 5000/6000 volt standard coil type ignition transformer to the spark plug on the
spark igniter using a high voltage ignition wire. Ensure that the spark plug’s wire electrode is
centered in the pilot nozzle.
NOTE
To reduce pressure losses, use adequate sized pipe and minimize elbows in the air and
gas lines to the pilot assembly. It is recommended that the air and gas supply be equal
to or greater than their respective pilot air and gas connection sizes. If the pilot is
installed at the end of a long run of pipe or will be operated in a dirty environment, it is
recommended that a sediment trap be installed in the pilot air line.