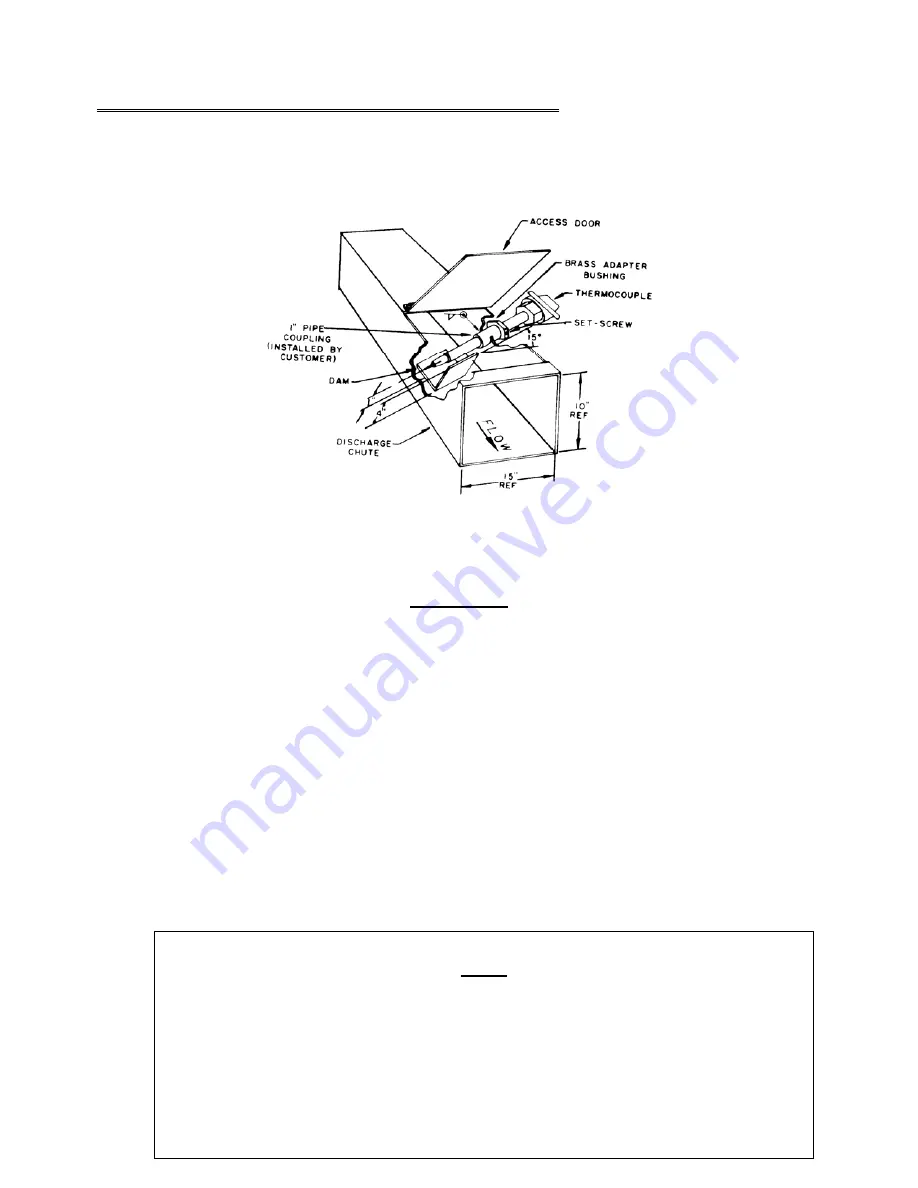
Page 18
BCS3000M-9
APPENDIX F: MATERIAL THERMOCOUPLE INSTALLATION
Install a Hauck Rapid Response Material Temperature Thermocouple in the material discharge
chute to sense the temperature of the material leaving the dryer. Wire the thermocouple to the
proper terminals in the panel.
Drawing showing the placement of the
thermocouple and "dam" in the dryer discharge chute.
IMPORTANT
A small clearance (1" maximum) should be provided under the thermocouple so material
will not be trapped between the thermocouple and the chute. Trapped material will cause a
heat loss path and the thermocouple will give erroneous readings.
The thermocouple should make good contact with the material but not be subject to severe
abrasion caused by high velocities. If the material is moving so fast that it bounces and
leaves air adjacent to the thermocouple, the temperature it senses will be lower than the
material. It may be necessary to place a dam in the chute so that the thermocouple is in a
relatively slow moving area next to the dam. The dam must only be wide enough and high
enough to create a localized area of build-up where the material loses velocity BUT DOES
NOT STOP FLOWING. The thermocouple must not be located in a stagnant zone or
erroneous temperature readings will result. Because of the large number of variables
involved, it is impossible to set down any exact size or location of the dam that will always
work. Field experimentation will be necessary if good results are to be obtained. It is
advisable to tack weld the dam in place so that it can be easily modified if it fails to perform
satisfactorily.
NOTE
During normal operation, the thermocouple should be rotated once a month to expose
a different area of its surface to the abrasive forces of the material. This procedure will
increase the effective life of the thermocouple. If excessive wear occurs, a protective
tube may be added to shield the shaft in the region of the high velocity flow.
Thermocouple cables must be separated from AC power and control wiring to
avoid interference and nuisance shutdowns. Observe polarity when making
thermocouple connections. Regardless of TC type, the red wire is always
negative.