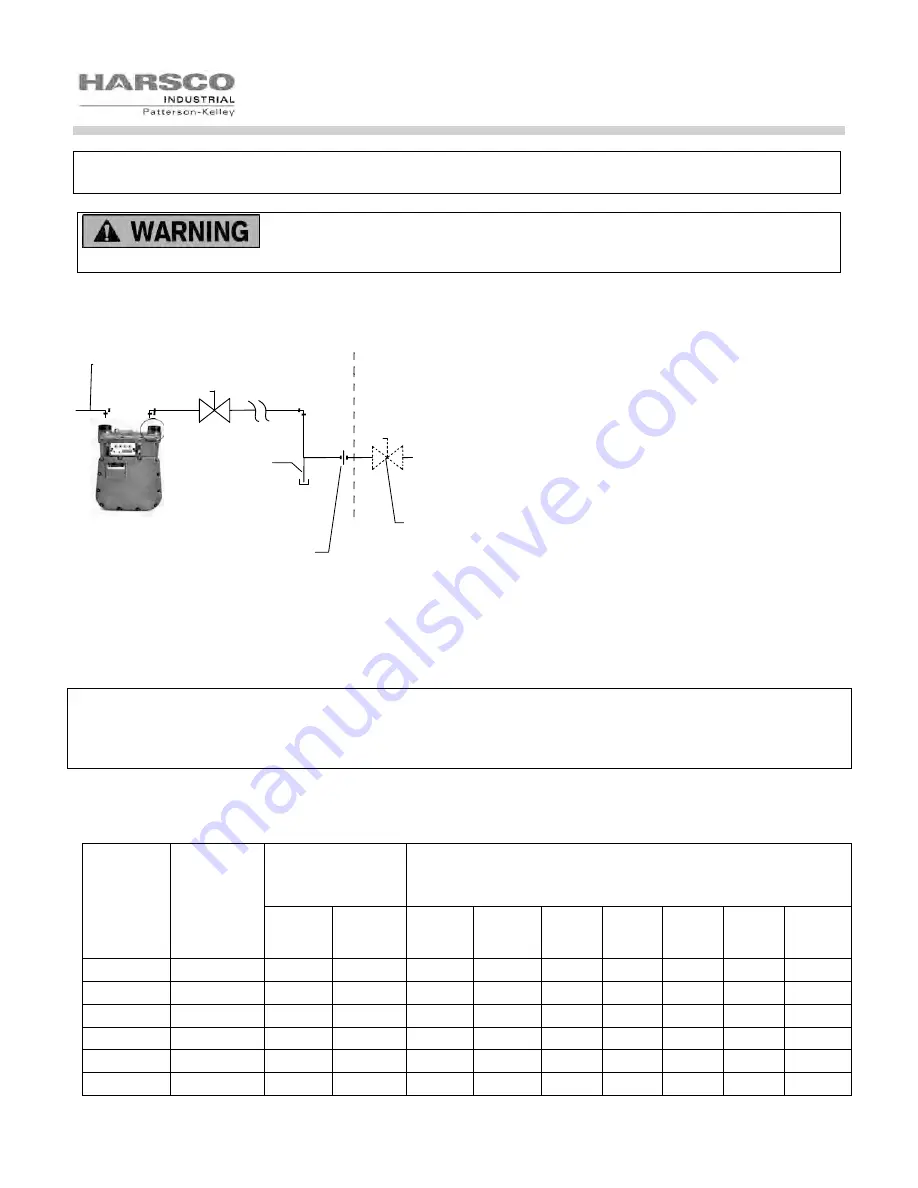
P-K THERMIFIC
®
Gas-Fired Boiler
27
NOTICE! The gas train components are certified to handle a maximum inlet pressure of 14" W.C. (1/2
psig.).
All threaded connections must be made using a pipe compound that is
resistant to the action of liquefied petroleum gases.
Do not use Teflon tape on gas line threads.
3.6.1 Gas Supply Piping by Installer
Gas Piping Schematic
Boiler Main Gas
Valve
Gas
Supply
Union
Drip Leg
Remote Gas
Shutoff
Install a sediment trap (drip leg) and a union connection ahead of the primary manual shutoff valve on
the boiler. Gas piping should be installed in accordance with National Fuel Gas Code, NFPA 54/ANSI
Z223.1, latest edition, and any other local codes which may apply in the U.S. In the Commonwealth of
Massachusetts, the gas cock must be a “T-handle type.” Gas piping should be installed in accordance
with CAN/CSA-B.149.1, latest edition in Canada.
NOTICE!
See chart below for required pipe size, based on overall length of pipe from meter plus
equivalent length of all fittings. Approximate sizing may be based on 1 cubic foot of natural gas per 1,000
Btu per hour input. For example, 900,000 Btu per hour requires about 900 cubic feet per hour. (See
Typical Boiler Operating Conditions, Section 4.3 for more information.)
Pipe Capacity for Natural Gas
Nominal
Iron Pipe
Size
(Inches)
Internal
Diameter
(Inches)
Equivalent Pipe
Length
Maximum Capacity in Cubic Feet of Natural Gas per Hour
Pressure Drop of 0.5 inch Water Column/Equivalent
Length of Pipe (in feet)
90º Ell
(Feet)
Tee
(Feet)
20
40
60
80
100
150
200
1-1/4
1.380
3.5
6.9
950
1-1/2
1.610
4.0
8.0
1,460
990
810
2
2.067
5.2
10.3 2,750 1,900 1,520 1,300 1,150 950
950
2-1/2
2.469
6.2
12.3 4,350 3,000 2,400 2,050 1,850 1,500 1,280
3
3.068
7.7
15.3 7,700 5,300 4,300 3,700 3,250 2,650 2,280
4
4.026
10.1
20.2 15,800
10,900
8,800 7,500 6,700 5,500 4,800
Summary of Contents for P-K THERMIFIC N700
Page 2: ...P K THERMIFIC Gas Fired Boiler 2...
Page 53: ...P K THERMIFIC Gas Fired Boiler 53 6 1 1 2 On Off Sealed Combustion Diagram 700 1000...
Page 54: ...P K THERMIFIC Gas Fired Boiler 54 6 1 1 3 On Off Sealed Combustion Diagram 1500 1700 2000...
Page 56: ...P K THERMIFIC Gas Fired Boiler 56 6 1 2 2 Lo Hi Lo Sealed Combustion Diagram 1500 1700 2000...
Page 58: ...P K THERMIFIC Gas Fired Boiler 58 6 1 3 2 Factory Installed Low Water Cut Off Diagram...