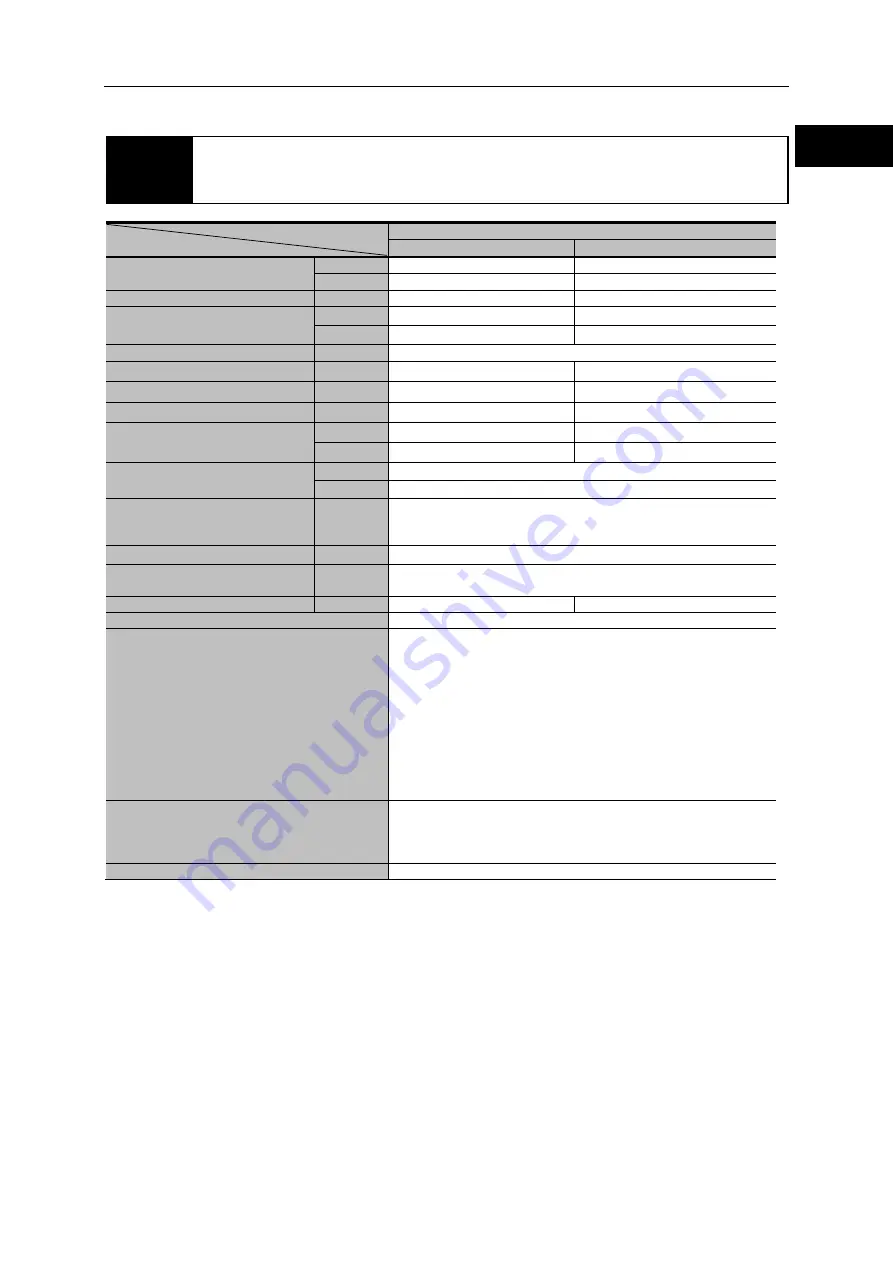
1-4 Specifications
4
付
11
10
9
8
7
6
5
4
3
2
1
O
ver
view
s
付
11
10
1-4
Specifications
Below is the specifications of the KDU Series motors.
Model
Item
KDU
-13SB
-13WB
Max. torque
Note 2
Nm
7.0
15.0
kgfm
0.7
1.5
Max. rotational speed
r/min
127
127
Torque constant
N m/A
3.1
6.5
kgfm/A
0.32
0.66
Input power supply
V
AC100/AC200
EMF constant
V/(r/min)
0.33
0.68
Line resistance
Ω
(20
℃
)
9.1
14.0
Line inductance
mH
19
35
Inertia
moment
(GD
2
/4)
kgm
2
0.0047
0.0065
(J)
kgfcms
2
0.048
0.066
Moment stiffness
Nm/rad
2.4
×
10
5
kgfm/rad
0.2
×
10
4
Motor position detector
pulse/rev
Incremental encoder
Square wave of Phases A and B:11,840,000
Pulse signal of Phase Z
Repeatability: Note 3
arc sec
±
0.5
Absolute positional accuracy:
Note 3
arc sec
10 (angular position correction): Note 4
Mass
kg
4.0
5.0
Protection structure
Totally enclosed self-cooled type (equivalent to IP40)
Environmental conditions
Service temperature: 10 to 30
℃
/Storage temperature: -10 to
60
℃ (Note 3)
Service/storage humidity: 20 to 80%RH (no condensation)
Resistance to vibration while transporting or mounting the
motor: 25 m/s2 (frequency: 10 to 400Hz)
Resistance to impact while transporting or mounting the
motor: 300 m/s2
No dust, metal powder, corrosive gas, inflammable gas, or oil
mist.
To be used indoors, no direct sunlight.
Altitude: less than1,000 m above sea level
Motor insulation
Insulation resistance: 100MΩ or more (by DC500V insulation
tester)
Dielectric strength: AC1,500V/1 min
Insulation class: B
Mounting direction
Output shaft facing up
Note 1: The table above shows the values for the output shaft.
Note 2: The values in the table are obtained when connected to the HA-770 Servo Driver
Note 3: The values for repeatability and absolute positional accuracy are measured with the mounting direction of
the output shaft facing up, and in an environment at a temperature of 23±0.3
℃
, with 50
%
humidity. Refer to
the "Notices for maintaining accuracy" on the next page when you use the motor.
Note 4: These values are after the angular position of the servo driver is corrected.
In order to enable angular position correction, it is always necessary to execute the originating operation by
the servo driver.