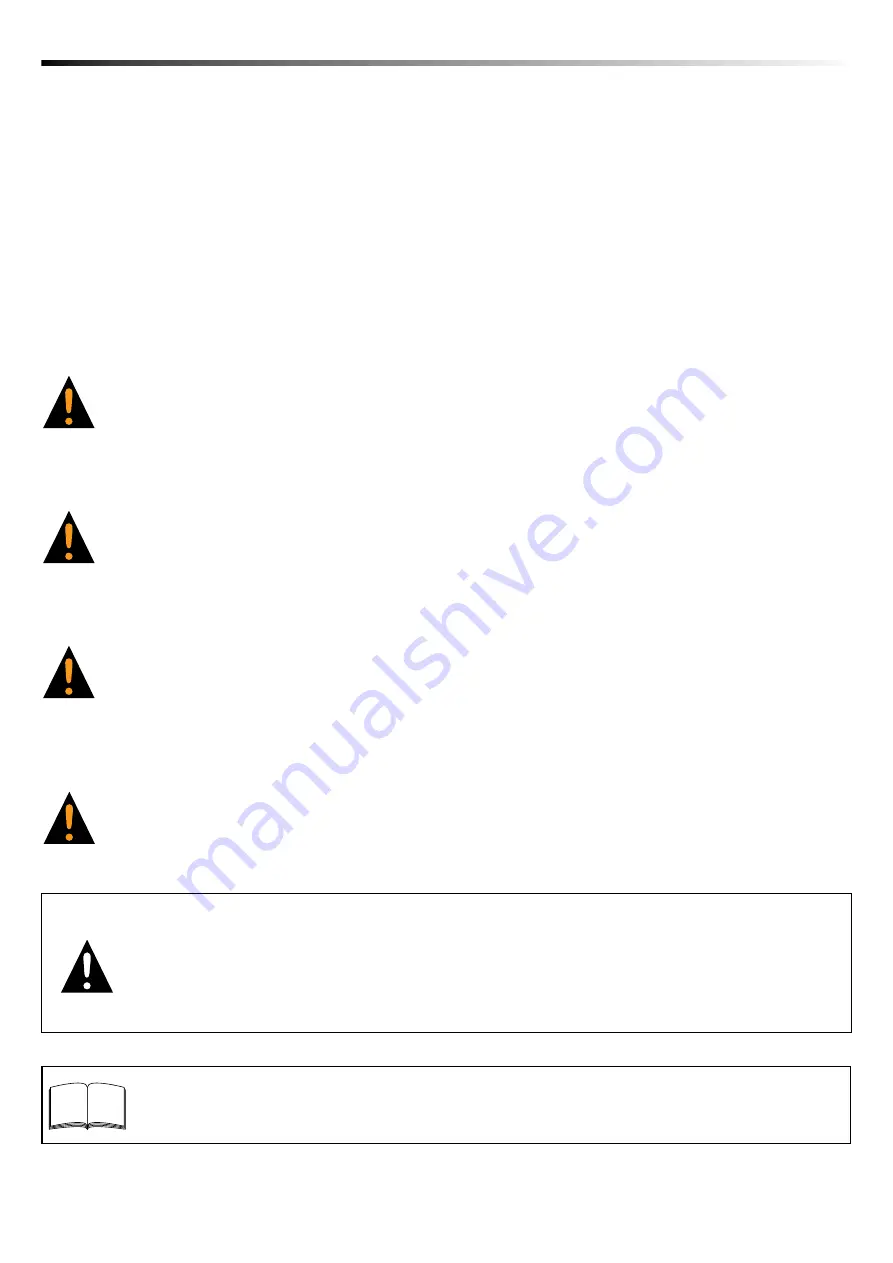
3
Riggers Winch 500
01/03/19
Safety Precautions
Please read these instructions carefully before operating equipment.
Keep these instructions in a safe place for future reference.
i
This product, as supplied by Harken
®
, is considered to be applicable to general lifting operations.
Should this product be incorporated into systems for lifting persons, it becomes “partly completed
machinery” and, when appropriate additional safety devices are added, must be certified for its
intended application. Such systems are classified as “machinery for lifting persons” and would
require separate CE marking.
Service Manual
You can download the Service Manual from www.harkenindustrial.com/manuals. This manual is for use only by
specialized personnel. Installation, disassembling and reassembling by personnel who are not experts may cause serious
damage to property or injury to users and those in the vicinity of the product. Harken
®
accepts no responsibility for
damage or harm caused by not observing the safety requirements and instructions in the service manual. See limited
warranty, general warnings, and instructions at www.harkenindustrial.com/manuals.
Introduction
This manual gives technical information on installation and service. If you do not understand an instruction, contact
Harken
®
.
WARNING! Strictly follow all instructions to avoid potential hazards that may kill or hurt you and others.
See www.harkenindustrial.com/manuals for general warnings and instructions.
DANGER! This indication alerts you to imminent hazards that will kill or seriously injure you and others
if you don't follow instructions. The message will tell you how to reduce the chance of injury.
WARNING! This indication alerts you to potential hazards that may kill or seriously injure you and others
if you don't follow instructions. The message will tell you how to reduce the chance of injury.
CAUTION! This indication alerts you to potential hazards that may hurt you and others if you do not fol-
low instructions. The message will tell you how to reduce the chance of injury.
Summary of Contents for 500
Page 2: ...2 Riggers Winch 500 01 03 19...
Page 23: ...23 Riggers Winch 500 01 03 19...