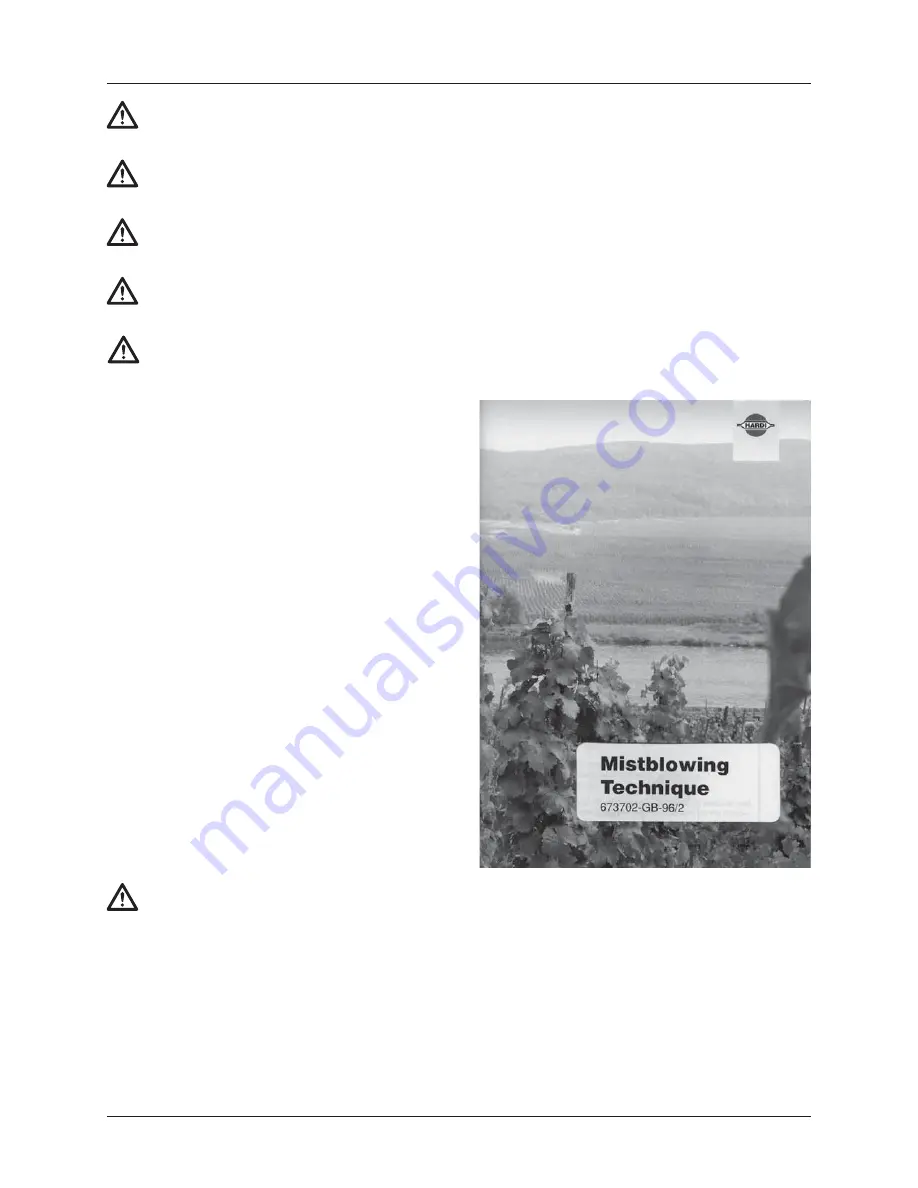
2 - Safe
t
y
not
e
s
2.2
Keep away from the air inlet and outlet while the fan is on. Some objects (small stones, etc.) may be expelled by
the fan.
Do not attempt to enter the tank.
The safety and efficiency of this machine depends entirely
on the care it receives. The first important step is to read
carefully and pay attention to this instruction manual which
contains essential information on the efficient use and
maintenance of this high quality product.
As this instruction manual includes all the HARDI® ZENIT
axial, pneumatic and hydropneumatic models, please pay
special attention to the paragraphs dealing with the model
you have acquired.
This manual should be read along with that of “Mistblowing
Technique” (provided with the equipment) so that you can
obtain the best possible results.
This product line is very versatile due to the large range of optional extras available and their possible combina-
tions. The most commonly used technical data for air flow, power consumption and directions, is included in this
manual. Please contact your nearest HARDI® dealer if you need additional information.
Tractor driver’s seat is the intended working place during operation.
If any portion of this instruction book remains unclear after reading it, contact your HARDI® dealer for further
explanation before using the equipment.
No persons are allowed in the operations area of the sprayer.
Summary of Contents for ZENIT
Page 1: ...ZENIT Instruction book 67302603 Version 1 01 US 02 2008 ...
Page 2: ......
Page 4: ......
Page 8: ...Table of contents TOC 4 Table of contents TOC 4 ...
Page 10: ...1 Welcome 1 2 ...
Page 14: ...2 Safety notes 2 4 ...
Page 32: ...4 Sprayer setup 4 6 ...
Page 44: ...5 Operation 5 12 ...
Page 63: ......