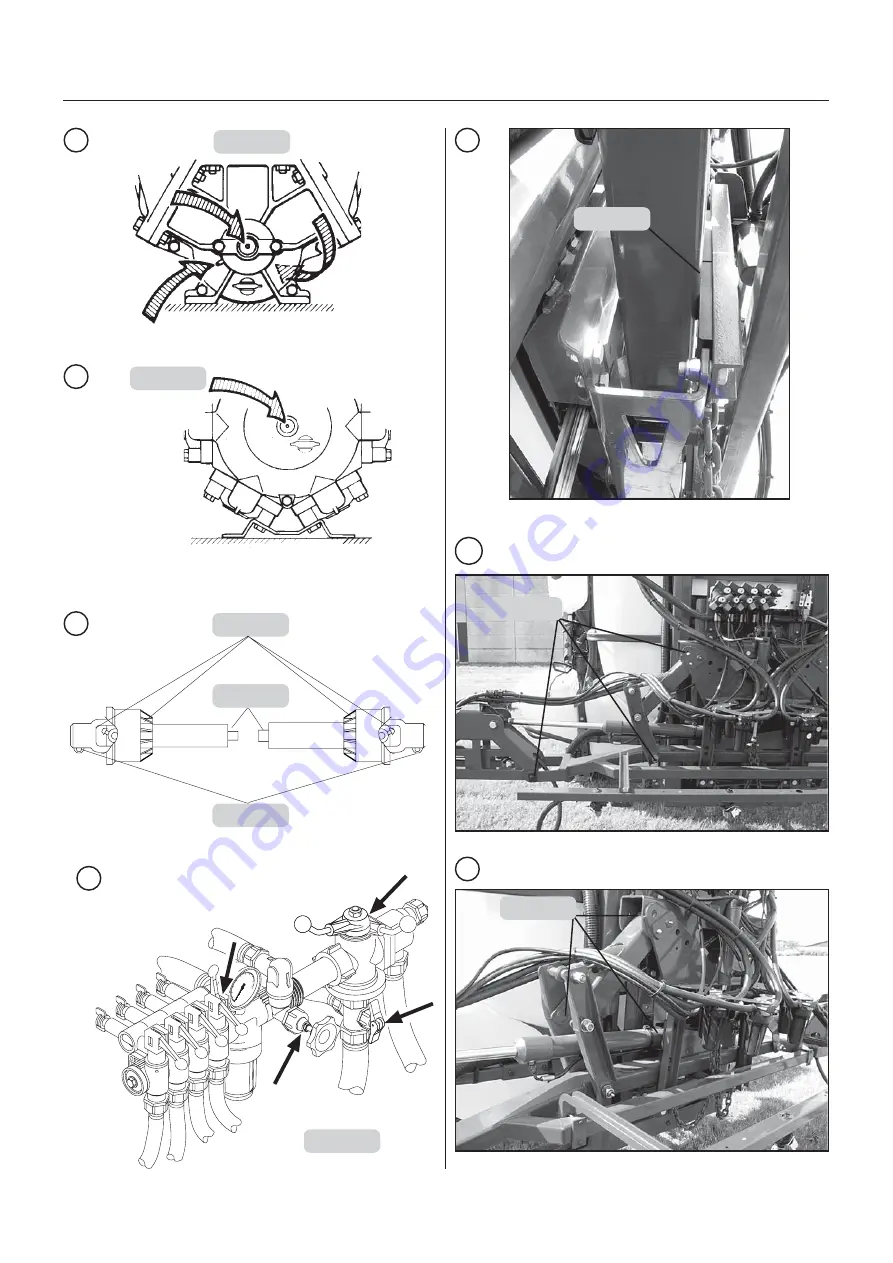
31
GB 13 00 MA
Maintenance
T212-0023
A - 10h
A - 10h
A - 10h
A - 10h
A - 10h
B - 50h
B - 50h
B - 50h
B - 50h
B - 50h
C - 50h
C - 50h
C - 50h
C - 50h
C - 50h
T226-0001
2
1
A - 50h
A - 50h
A - 50h
A - 50h
A - 50h
1
A - 50h
A - 50h
A - 50h
A - 50h
A - 50h
C - 20h
C - 20h
C - 20h
C - 20h
C - 20h
3
Models with BK control unit only
4
D - 50h
D - 50h
D - 50h
D - 50h
D - 50h
T212-0029
5
B - 50h
B - 50h
B - 50h
B - 50h
B - 50h
5
T212-0024
C - 50h
C - 50h
C - 50h
C - 50h
C - 50h
Summary of Contents for MASTER HVZ Series
Page 2: ...2 ...