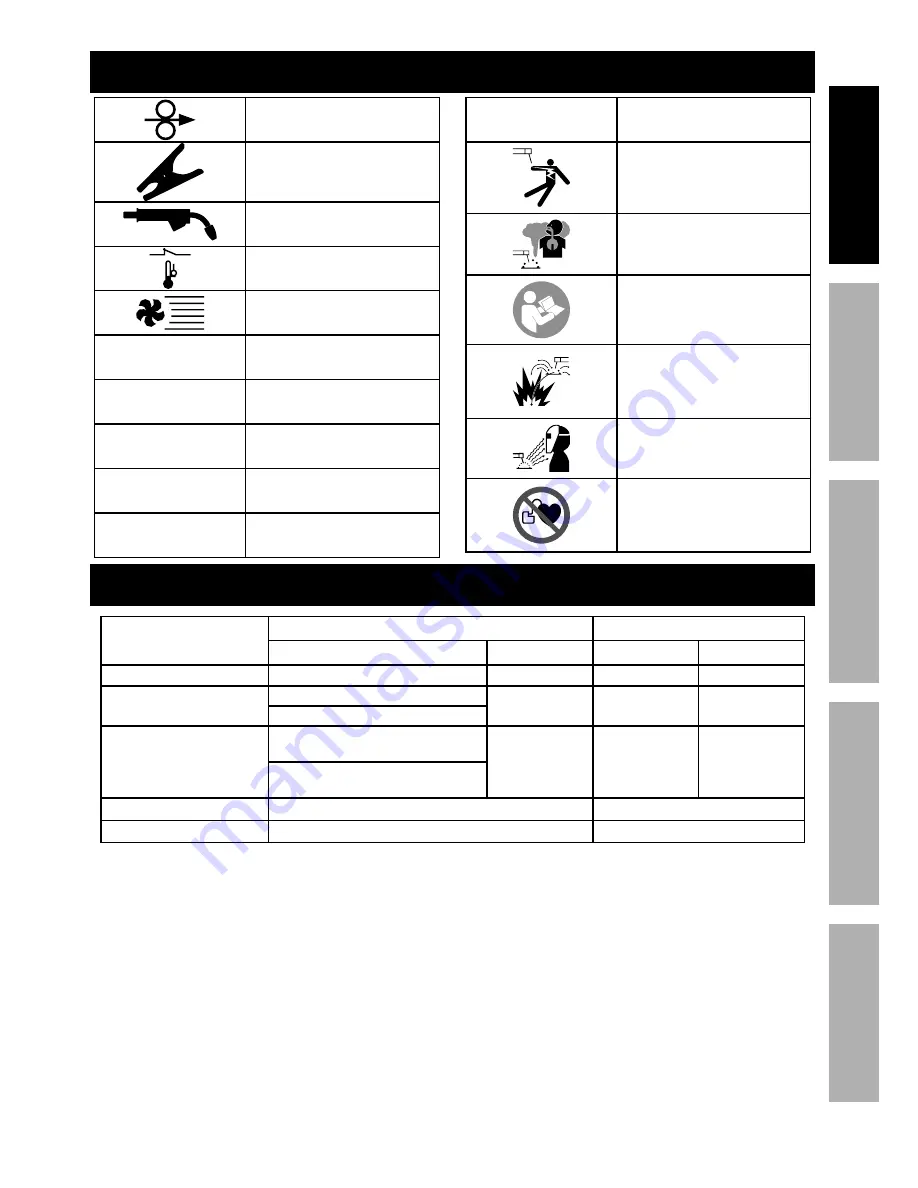
Page 7
For technical questions, please call 1-888-380-0318.
Item 63619
S
AFET
y
M
AINTENAN
c
E
B
ASI
c W
EL
d
IN
g
W
EL
d
IN
g T
Ip
S
SETUP
S
AFET
y
M
AINTENAN
c
E
B
ASI
c W
EL
d
IN
g
W
EL
d
IN
g T
Ip
S
SETUP
Symbology
Wire Feed (Speed)
Workpiece Ground Cable
Torch Cable
Overheat Shutdown Indicator
Cooling Fan
VAc
Volts Alternating Current
A
Amperes
OcV
Open Circuit Voltage
KVA
Kilovolt Amperes
(Volts / 1000 * Amperes)
IpM
Inches Per Minute
AWg
American Wire Gauge
Electric Shock Hazard.
Do not touch energized parts.
Inhalation Hazard.
Keep head out of fumes
and use proper ventilation.
Read manual before
setup and/or use.
Fire Hazard.
Keep flammable materials
away during welding. Spatter
can cause accidental fires.
Arc Ray Hazard.
Wear welding helmet with
properly rated filter lens.
Pacemaker Hazard.
Welding processes may
interfere with pacemakers.
Consult doctor before use.
Specifications
TIG
Stick
120VAC / 60Hz
240VAC / 60Hz 120VAC / 60Hz 240VAC / 60Hz
Power Input at Output
21.4A at 115A
21A at 200A
21A at 80A
24A at 170A
Welding Current Range
15A: 10A - 115A
10A - 200A
10A - 80A
10A - 170A
20A: 10A - 130A
Rated Duty Cycles
15A:
35% @ 115A
100% @ 63A
25% @ 200A
100% @ 100A
20% @ 80A
100% @ 50A
20% @ 170A
100% @ 75A
20A:
25% @ 120A(AC)/130A(DC)
100% @ 63A
Maximum OCV
13.5VDC (with VRD)
13.5VDC (with VRD)
Weldable Materials
Mild Steel, Stainless Steel, Aluminum, Chrome Moly
Mild Steel, Stainless Steel