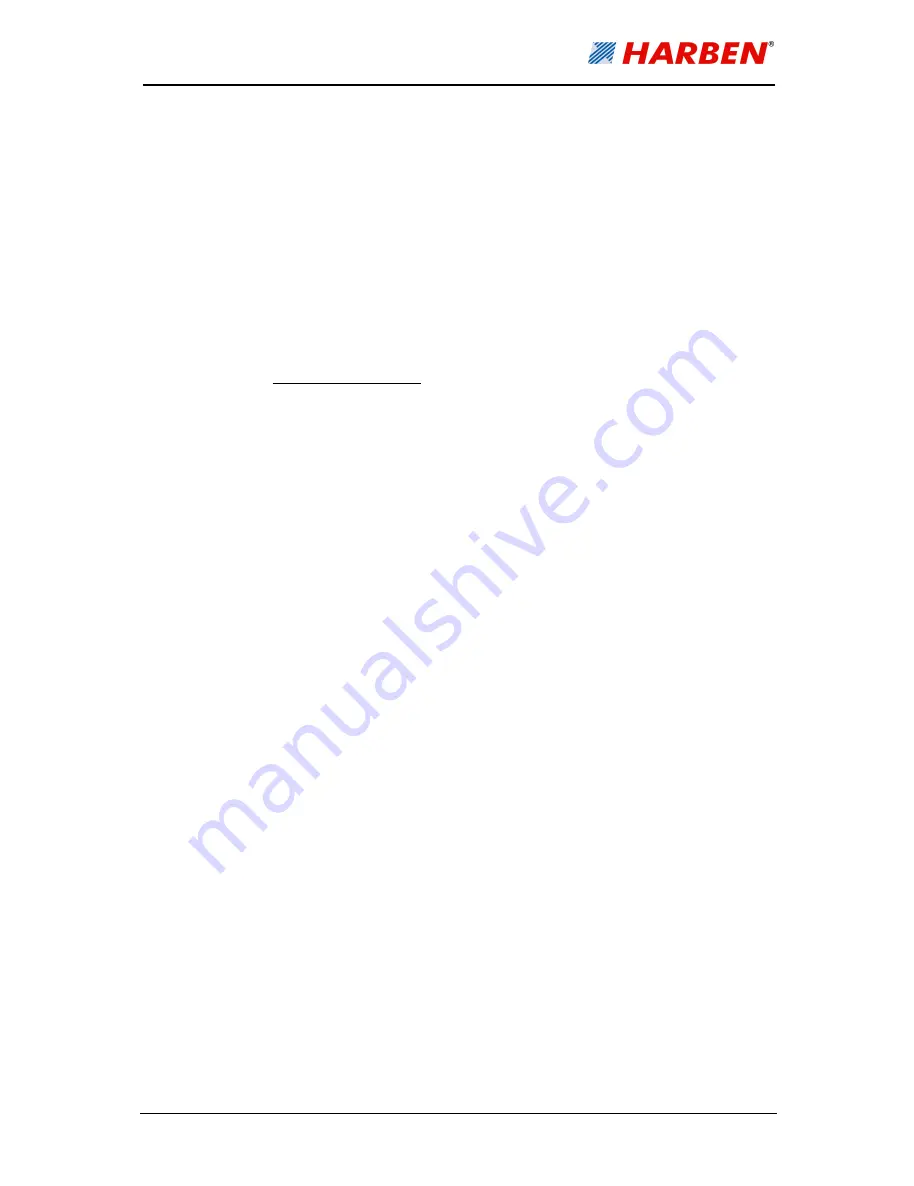
45
In Order to Make a Warranty Claim
1. You must be the original purchaser of the machine in which the part(s) were originally
installed.
2. You must notify us or our authorized service agent that you wish to make a warranty claim.
When requested you must return the faulty part(s) clearly labelled and carriage paid along
with the unit/pump serial number and any other information that we may reasonable request.
3. All components must have been installed and maintained in accordance with good industry
practice and any specific recommendations we made, including those in our maintenance
schedule that is supplied with your machine.
4. We will replace, at the customers cost, any part(s) returned for warranty inspection. When
our inspection has been completed we will advise if the parts(s) are covered by our warranty
policy and if they are we will credit your account for the cost of the new part(s), minus taxes
and shipping charges.
5. Our warranty does not cover travel charges, down time, or consequential losses.
6. No part(s) will be considered for replacement under warranty if it is subject to any of the
following reasons for exclusion.
• Used for a purpose for which it is not designed
• Applied to a use which has not been approved by Harben
• Subject to misuse, negligence, lack of maintenance or accident
• Repaired or altered in any way which, in our judgement, may adversely affect its performance
and reliability
• Considered as fair wear and tear
All manuals and user guides at all-guides.com
Summary of Contents for 4018
Page 10: ...8 Figure 2 1 DPK 750 Manual Primary Components All manuals and user guides at all guides com...
Page 11: ...9 Figure 2 2 DPK 375 Manual Primary Components All manuals and user guides at all guides com...
Page 12: ...10 Figure 2 3 DPK 750 Remote Primary Components All manuals and user guides at all guides com...
Page 40: ...38 8 3 2 Radio Wiring Diagram All manuals and user guides at all guides com...
Page 44: ...42 Service Documents 11 1 Service Checklist All manuals and user guides at all guides com...
Page 45: ...43 11 2 Service Logbook All manuals and user guides at all guides com...
Page 49: ...47 This page is left blank on purpose All manuals and user guides at all guides com...