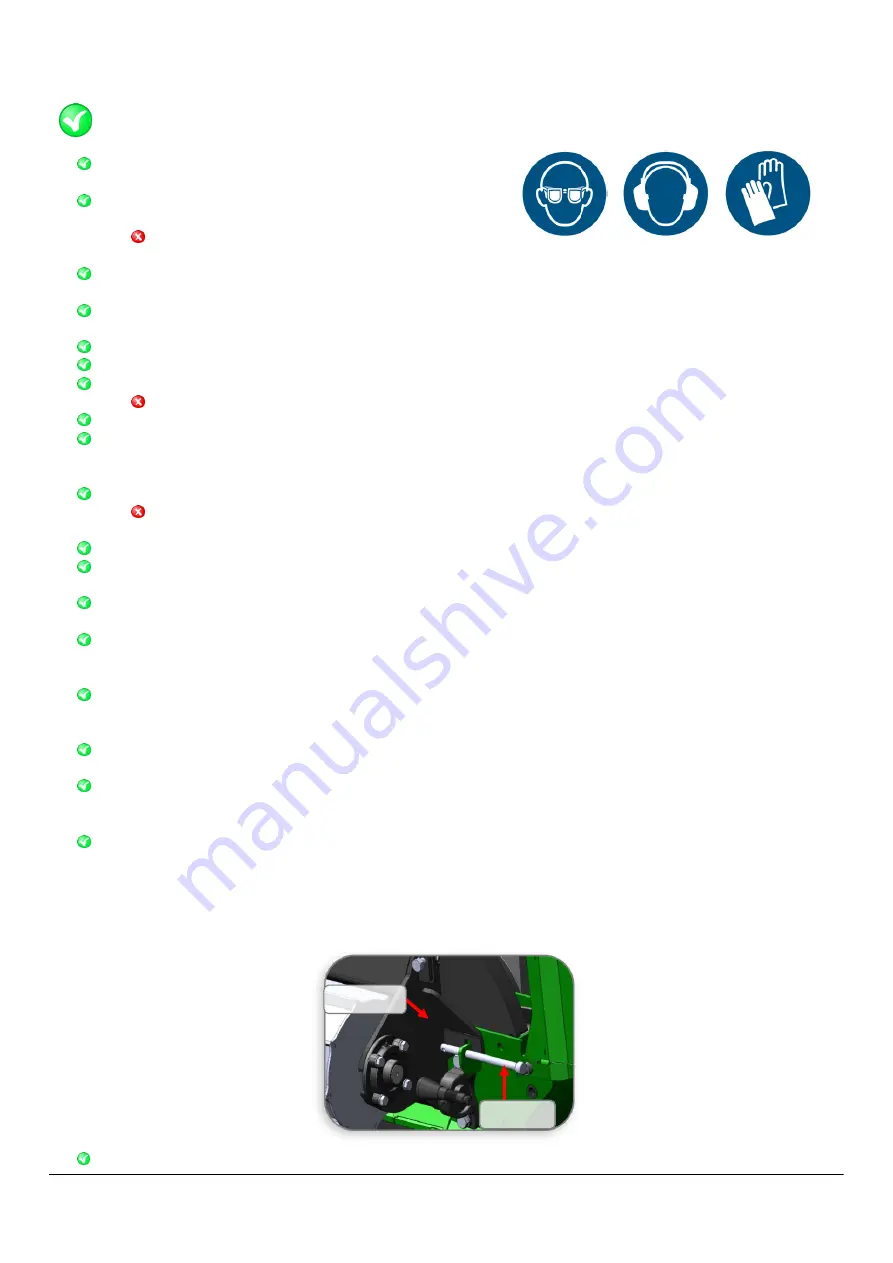
Hansa C60 RX O&M Manual
– OM-015 Revision E 23/10/2019
© Hansa Chippers 2019
6
Safe operating procedure
Wear safety equipment:
Safety glasses and hearing protection
must be worn at all times
Wear work gloves:
The wearing of work gloves is optional but
highly recommended - ensure that the gloves fit tightly
Do NOT
wear loose fitting gloves or gloves with long cuffs
Loose gloves may get snagged by branches, which could result in the operator being pulled into the chipper
Tie long hair up
Long hair could be snagged by a branch and may be pulled into chipper
Wear clothes that sit tightly
Avoid scarves and any items that can get caught in the chipper or snagged on branches
Place the chipper on even ground and direct outlet chute onto soft ground
Ensure exhaust is pointing away from the working area and downwind from the operator and onlookers
Keep proper balance and footing at all times and stand at the same level as the chipper
Do NOT
climb onto the feed table to push material into the feed roller
Ensure the chipper is positioned so that there is a minimum inlet table height of 600 mm off the ground
Keep your face and body away from the inlet chute. Stand to the side of the inlet table while feeding material into the
chipper
Standing to the side gives better access to the control bar and helps in keeping clear from flying debris
Feed only freshly cut material into the chipper
Do NOT
feed in materials covered in gravel, stones and dirt as this can rebound, injure the operator and damage
the machinery
Prune to a size that suits the chipper
’s capabilities
Pre-cut side branches
T
he branch will ‘self
-
feed’ more ef
ficiently
Keep the engine clean of debris and other accumulations
This prevents damage to the engine or possible fire
Feed limbs and branches through butt end first, leaving the bushy head on
This helps guide the limb down the inlet chute
It reduces spinning and the occurrence of ejection of small pieces back up the inlet chute
Feed soft materials intermittently with branches
The wood chips tend to clean out any soft residue left in the chipper
The chipper can clog up with soft, wet or fibrous materials
Keep well clear of the outlet chute discharge area, even when the chipper is not currently processing material
High velocity, sharp discharge can cause serious injury
Keep the outlet free of blockage
If blockage occurs, turn the engine off and wait for rotor to stop spinning. Open the outlet chute and remove
material until the outlet chute is clear
Keep the feed roller free of blockage
If blockage occurs, turn the engine off and wait for rotor to stop spinning. Remove the feed roller guard by
unhooking the four rubber latches. Unhook the springs from the base of the chassis. Lift the swing arm up and
insert the rotor pin (located underneath the control panel) into the tab on the housing to lock the swing arm in
place (as per the diagram below). You may now safely clear the blockage. Remove the rotor pin, lower the feed
roller, reposition the springs, then replace the guard
Turn off the engine whenever you leave the work area
DO:
Rotor pin
Swing arm