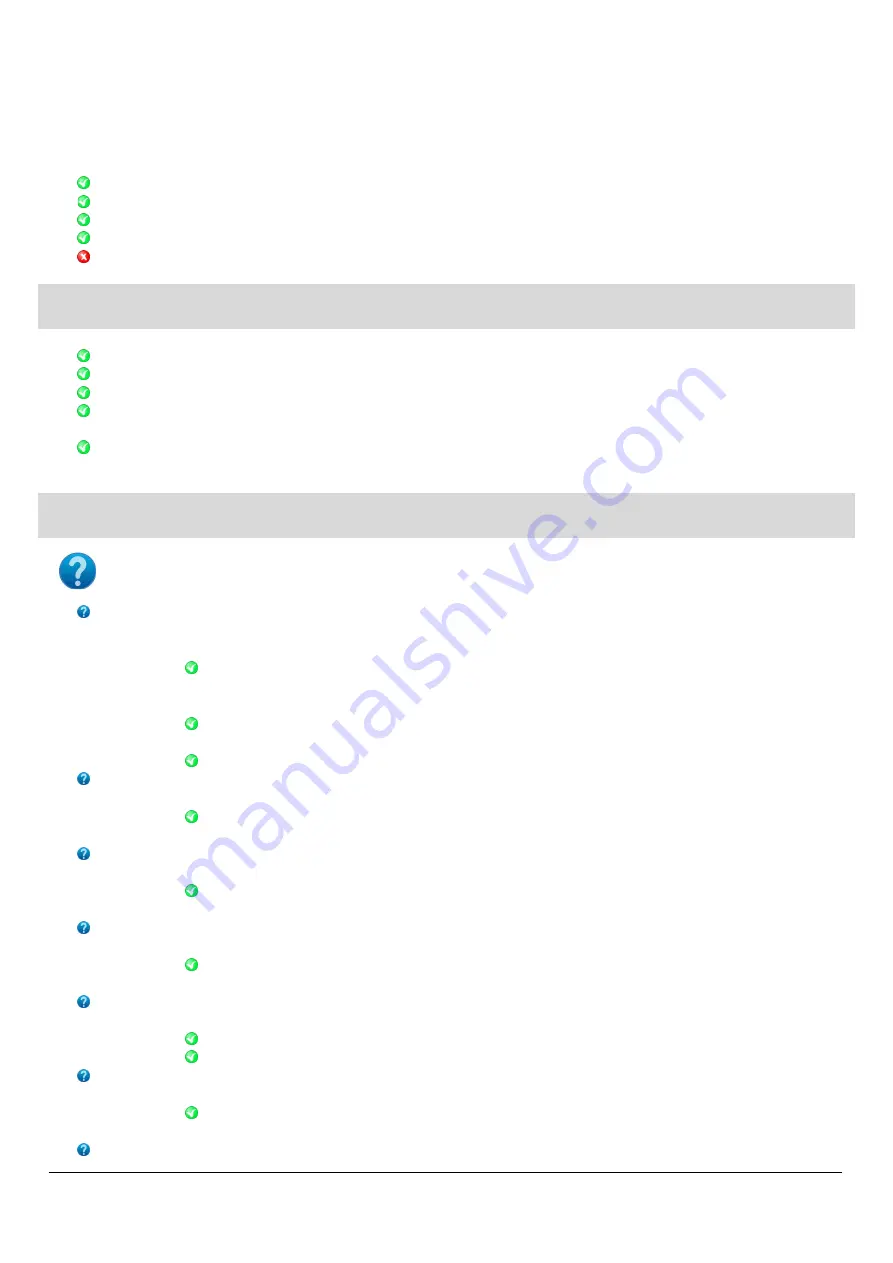
Hansa C16c O&M Manual – OM-020 Revision B 24/06/2019
© Hansa Chippers 2019
10
Emergency stop
The emergency stop acts as an immediate kill switch to the engine. It does not stop the cutting rotor from spinning. The cutting
rotor will continue to spin for some time due to its rotational inertia. To engage the emergency stop, push the red button. To
disengage the emergency stop, twist the red button clockwise until it releases outwards.
Use it when foreign matter such as sand, stones or metal enter the inlet chute
Use it in response to an immediate hazard/danger to an operator or onlooker
After the cutting rotor comes to a halt, follow the regular shutdown procedure in addition to using the emergency stop
Inspect the machine before resetting the emergency stop
Under normal conditions,
Do NOT
use the emergency stop in place of the regular shutdown procedure
Storage
Always allow the chipper to cool before storing
Store the chipper out of the reach of children
Store the chipper where fuel vapor will not reach an open flame or spark
Switch fuel lever to off position
For extended storage periods, run the unit dry of fuel
Store the chipper out of the rain
Water can rust the steel body of the chipper
Troubleshooting
What to do if:
The chipper won’t start
•
The engine oil level might be too low
The chipper is fitted with oil alert and will not start if the oil level is too low
Check the oil level and top up if required
•
The chipper is placed on a slope
The chipper is fitted with oil alert and will not start if the oil is not level
Move the chipper to level ground
•
The emergency stop is still engaged
Ensure emergency stop is disengaged before starting the chipper
Belt drive engagement will not work
•
The inlet chute or housing might be blocked
Turn engine off, disconnect the spark plug wire, ensure cutting rotor has completely stopped, remove
debris, restart engine, then attempt to re-engage the belt drive
The chipper slows down and stalls
•
The chipper is clogged up
Turn the engine off, disconnect the spark plug wire, ensure cutting rotor has completely stopped,
remove debris, then close and lock the outlet chute
Discharge slows down
•
The chipper is clogged up
Turn the engine off, disconnect the spark plug wire, ensure cutting rotor has completely stopped,
remove debris, then close and lock the outlet chute
The chipper is slowing down
•
The chipper can’t process the amount of material fed into it
Feed the material in slower
Reduce material volume
The chipper will not self-feed
•
The knives and/or anvil might be blunt
Inspect and sharpen or replace knives and/or anvil as required. Ensure correct clearances between
knives and anvil
The material is ejected in long strips