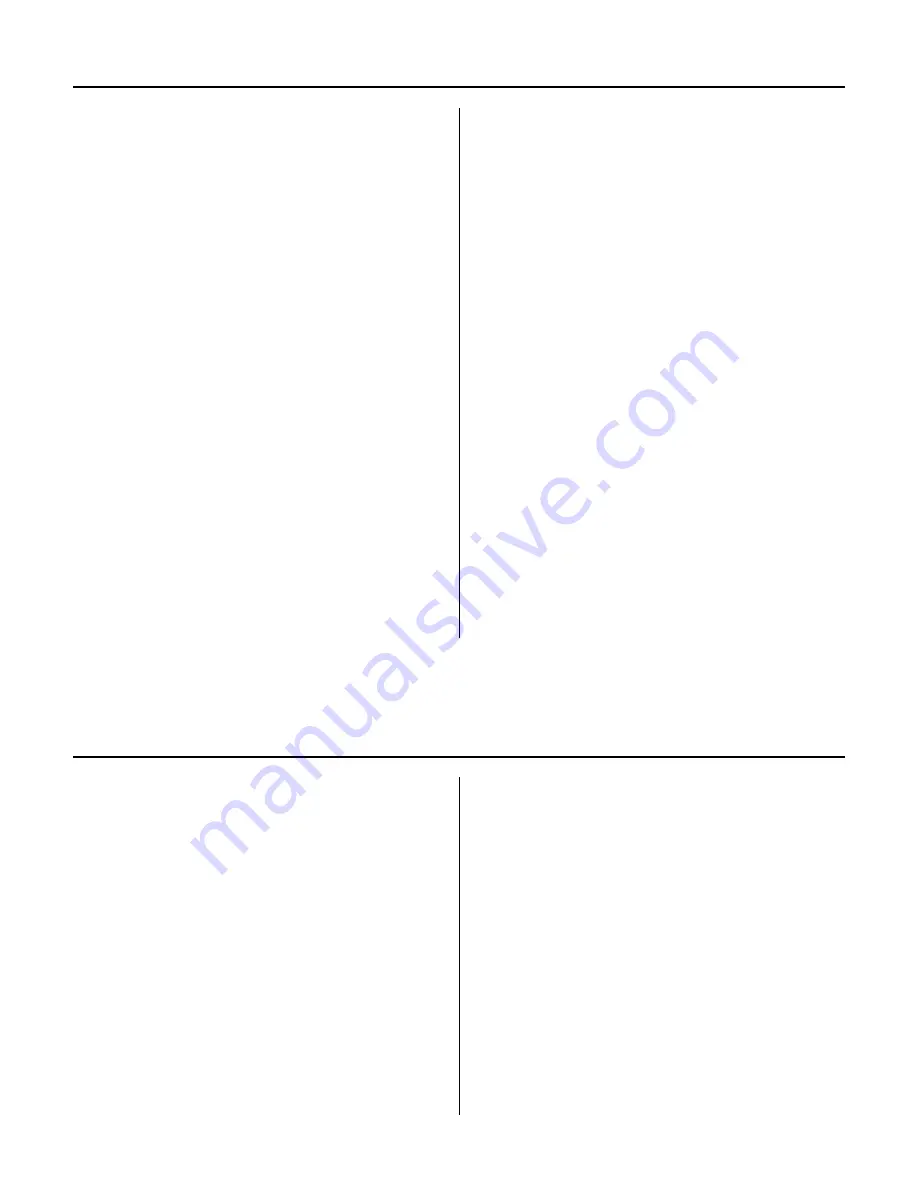
41
Range Test Your Radio
.
Step 1
Before.going.to.the.field,.be.sure.that.your.batteries.
are.fully.charged,.per.the.instructions.included.with.
your.radio..Charge.both.the.transmitter.and.receiver.
pack.for.your.airplane..Use.the.recommended.charger.
supplied.with.your.particular.radio.system,.following.the.
instructions.provided.with.the.radio..In.most.cases.the.
radio.should.be.charged.the.night.before.going.out.flying.
.
Step 2
Before.each.flying.session,.be.sure.to.range.check..
your.radio..See.your.radio.manual.for.the.recommended.
range.and.instructions.for.your.radio.system..Each..
radio.manufacturer.specifies.different.procedures.for..
their.radio.systems..Next,.start.the.engine..With.the..
model.securely.anchored,.check.the.range.again..The.
range.test.should.not.be.significantly.affected..If.it.is,..
don’t.attempt.to.fly!.Have.your.radio.equipment.checked.
out.by.the.manufacturer.
Note
:.Keep.loose.items.that.can.get.entangled.
in.the.propeller.away.from.the.prop..These.
include.loose.clothing,.or.other.objects.
such.as.pencils.and.screwdrivers..Especially.
keep.your.hands.away.from.the.propeller.
.
Step 3
Double-check.that.all.controls.(aileron,.elevator,.rudder.
and.throttle).move.in.the.correct.direction.
.
Step 4
Check.the.radio.installation.and.make.sure.all.the..
control.surfaces.are.moving.correctly.(i.e..the.correct.
direction.and.with.the.recommended.throws)..Test..
run.the.engine.and.make.sure.it.transitions.smoothly..
from.idle.to.full.throttle.and.back..Also.ensure.the..
engine.is.tuned.according.to.the.manufacturer’s.
instructions,.and.it.will.run.consistently.and.constantly..
at.full.throttle.when.adjusted.
Check.all.the.control.horns,.servo.horns,.and.clevises.to.
make.sure.they.are.secure.and.in.good.condition..Replace.
any.items.that.would.be.considered.questionable..Failure.
of.any.of.these.components.in.flight.would.mean.the.loss.
of.your.aircraft.
Before.each.flying.session,.range-check.your.radio..This.
is.accomplished.by.turning.on.your.transmitter.with.the.
antenna.collapsed..Turn.on.the.radio.in.your.airplane..
With.your.airplane.on.the.ground,.you.should.be.able.
to.walk.30.paces.away.from.your.airplane.and.still.have.
complete.control.of.all.functions..If.not,.don’t.attempt.
to.fly!.Have.your.radio.equipment.checked.out.by.the.
manufacturer.
Preflight
Range Testing the Radio
Summary of Contents for P-51D 1.50 ARF
Page 44: ...44 Building Notes ...
Page 45: ...45 Page left blank intentionally ...
Page 47: ...47 Flying Notes ...