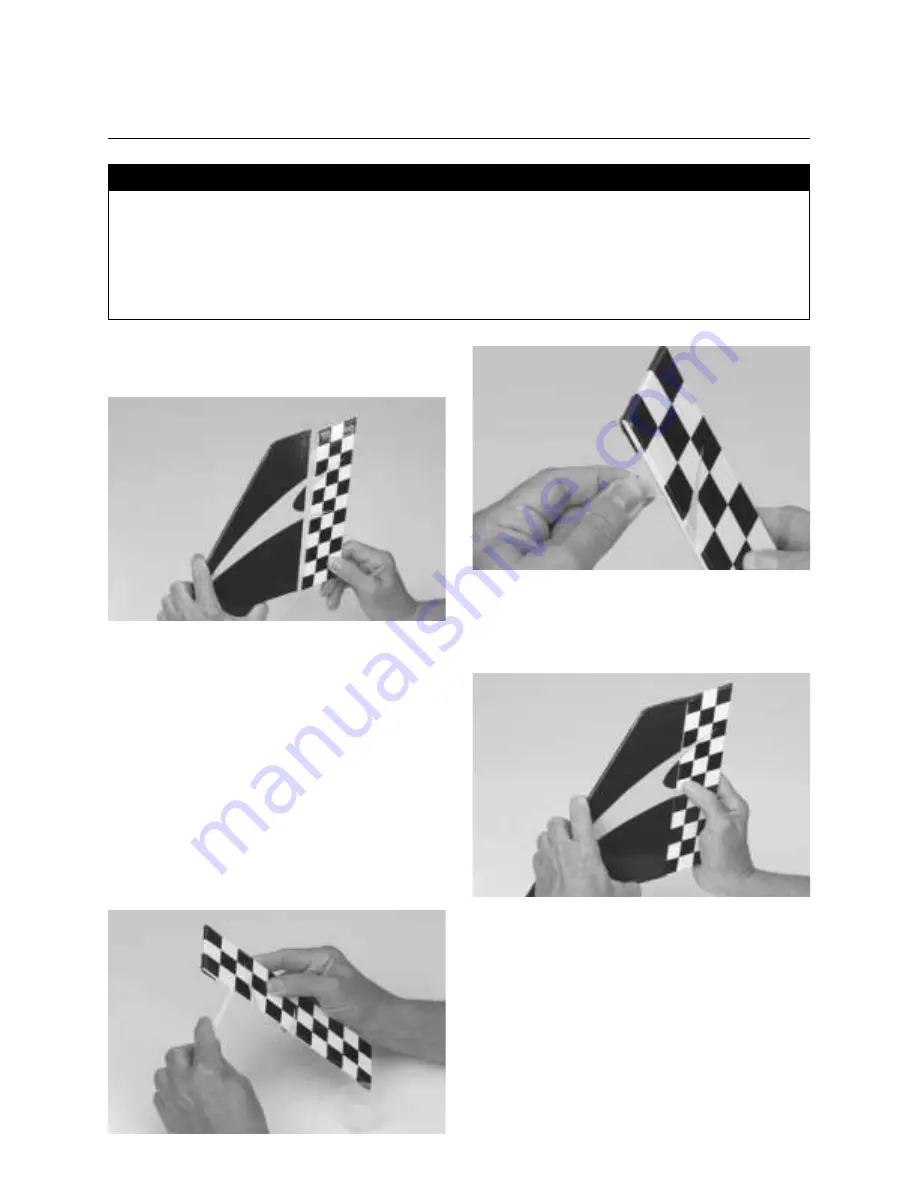
21
Section 6: Hinging the Vertical and Horizontal
Stabilizers
1.
Carefully remove the rudder from the vertical stabilizer by
pulling straight out with even pressure.
2.
Remove the three hinges from the rudder and flex them along
the hinge line so they move freely.
3.
Mix a small amount, approximately 1/4 oz., of 30-minute
epoxy. Using either a mixing stick, scrap of wood or epoxy brush,
sparingly apply the epoxy inside each hinge slot on the rudder.
Additionally, apply a small amount of epoxy to the top and
bottom one-half of each hinge.
It’s necessary to roughen the surface of the hinges with
sandpaper so the epoxy will adhere better to the hinge.
Insert the hinges into the rudder until the hinge line is even with
the leading edge of the rudder.
4.
Apply epoxy to the remaining half of each hinge and into the
hinge slots in the vertical stabilizer as well. Replace the rudder
onto the vertical stabilizer.
• Horizontal stabilizer with elevator
• Vertical stabilizer with rudder
• 30-minute epoxy
• Mixing stick
• Epoxy brush
• Paper towels
• Rubbing alcohol
• Sandpaper (medium)
Parts Needed
Tools and Adhesives Needed
Summary of Contents for Hangar 9 Solo
Page 58: ...58 NOTES ...
Page 59: ...59 NOTES ...
Page 60: ... Copyright 1998 Horizon Hobby Distributors Inc ...