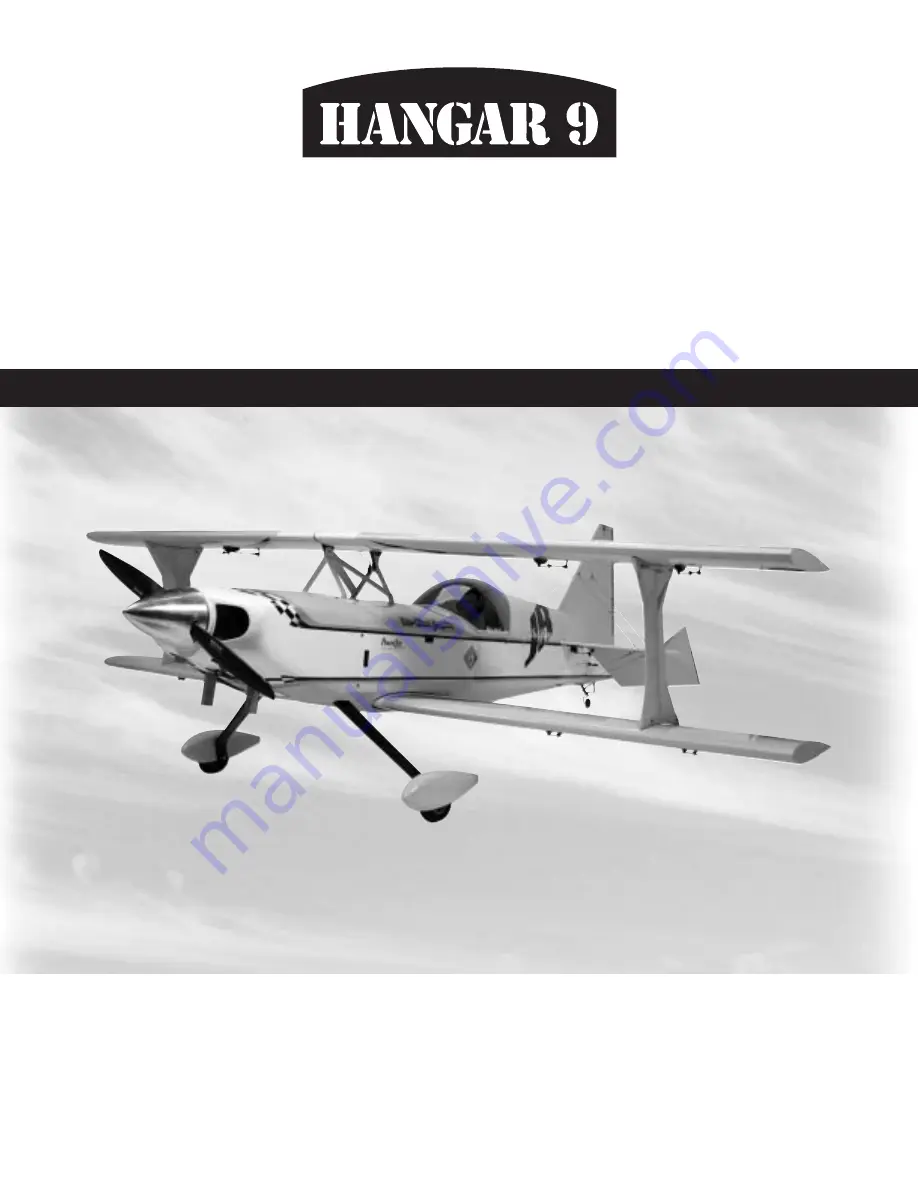
WE GET PEOPLE FLYING
TM
®
Specifications
Wingspan ..........................................................................................100 in (2540 mm)
Length ................................................................................................110 in (2794 mm)
Wing Area.........................................................................................3310 sq in (213.5 sq dm)
Weight ...............................................................................................40–44 lb (18–20 kg)
Engine.................................................................................................150–200cc gas engine
Radio ..................................................................................................6-channel w/15 servos
ASSEMBLY MANUAL
46%
TOC Ultimate 10-300