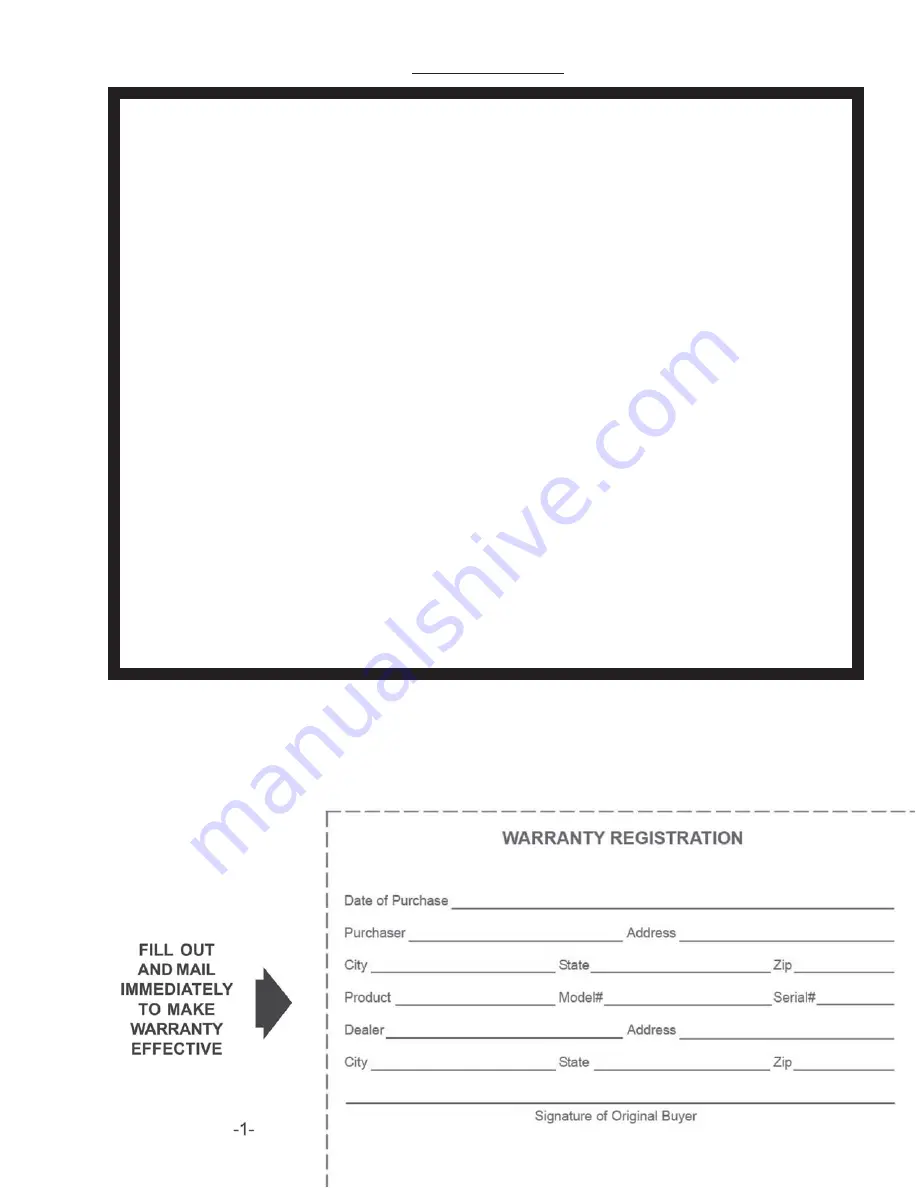
TM3/04
H&S MANUFACTURING CO., INC. WARRANTY
H&S Manufacturing Co., Inc. (“H&S”) warrants this product to be free from defect in material and workmanship. Except as
noted below, this warranty term is 120 days from the date of delivery of the product to the original purchaser by and authorized
H&S dealer. Under this warranty H&S will repair or replace, at it’s option, any covered part which is found to be defective in
material or workmanship during the applicable warranty term. In no case will the covered repair cost of a part or parts exceed
the replacement cost of that part. Warranty service must be performed by H&S or a dealer authorized by H&S to sell and/or
service the product involved, which will use only new or remanufactured parts or components furnished by H&S. This warranty
includes approved parts and labor to fix the product but does not include, and the purchaser is responsible for; any service call
and/or transportation of the product to and from the dealer’s place of business, for any premium charged for overtime labor
requested by the purchaser, and for any service work not directly related to any defect covered under this warranty. This
warranty includes only those components of the product manufactured by H&S. Warranty for any component not manufactured
by H&S including, but not limited to engines, batteries, tires, rims, hydraulic motors, pumps etc., are covered by the warranty if
any provided separately by their respective manufacturers.
This warranty in all its parts, is extended solely to the original purchaser of the product, is terminated upon any subsequent
transfer or sale from or by the original purchaser and extends no third party benefits or rights whatsoever.
This warranty does not include: (1) Any product that has been altered or modified in ways not approved by H&S; (2)
Depreciation or damage caused by normal wear, misuse, improper or insufficient maintenance, improper operation, accident or
failure to follow the product Operator Manual recommendations and product decal recommendations; (3) Normal maintenance
parts and service; (4) Repairs made with parts other than those available from H&S or performed by anyone other than H&S or
a dealer authorized by H&S to sell and/or service the product involved.
To secure warranty service the purchaser must report the product defect to a dealer authorized by H&S to sell and/or service
the product involved within the applicable warranty term together with evidence of the warranty start date and make the product
available to that dealer within a reasonable period of time.
THERE ARE NO WARRANTIES WHICH EXTEND BEYOND THE DESCRIPTION ON THE FACE OF THIS WARRANTY. H&S and the
companies affiliated with it makes no warranties, representations, or promises, express or implied, as to the quality or
performance or freedom from defect of its products other than these set forth above and NO IMPLIED WARRANTY OF
MERCHANTABILITY, FITNESS OR FITNESS FOR A PARTICULAR PURPOSE IS MADE. IN NO EVENT WILL THE DEALER, H&S
OR ANY COMPANY AFFILIATED WITH H&S BE LIABLE FOR INCIDENTAL OR CONSEQUENTIAL DAMAGES. The ONLY
REMEDY the purchaser has in connection with the breach of performance of any warranty on H&S products are those set
forth above.
The selling dealer has no authority to make any representations or promise on behalf of H&S, or to modify the terms or
limitations of this warranty in any way.
WARRANTY
Summary of Contents for TWM12
Page 4: ......
Page 6: ...Intentionally Left Blank 4...
Page 8: ...Intentionally Left Blank 6...
Page 11: ...SAFETY DECALS 9...
Page 13: ...11...
Page 27: ...LUBRICATION GUIDE 10 9 2 1 1 1 2 9 10 1 25 5 6 6 6 7 7...
Page 28: ...LUBRICATION GUIDE 1 10 9 9 5 2 10 2 26 3 3 7 7 HYDRAULIC BRAKE OPTION 3...
Page 35: ...33 SERVICE NOTES...
Page 36: ...34 SERVICE NOTES...
Page 37: ......