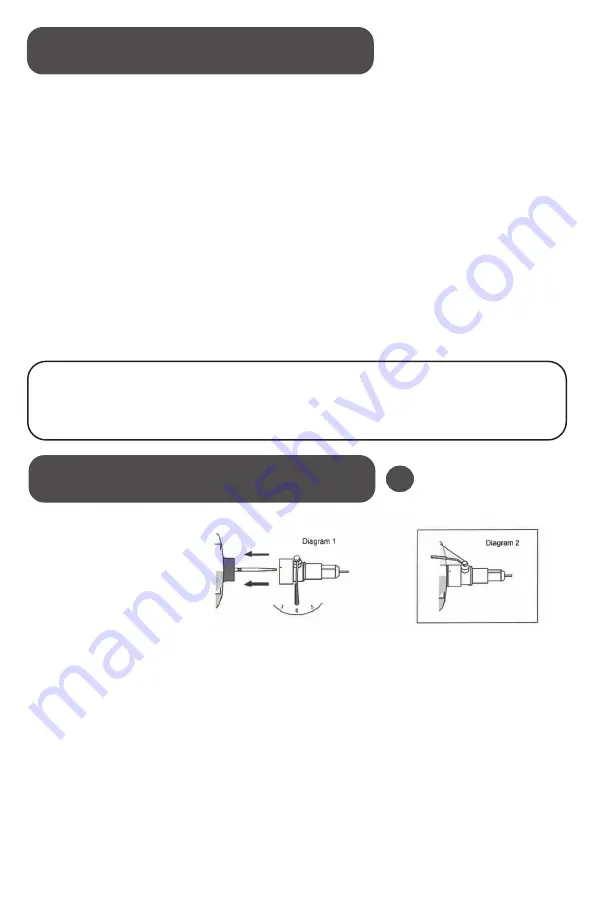
4
General Care and Maintenance
For all Models
CLEAN COLLETS EVERY 30 DAYS
1.
With lathe switch OFF and clutch handle straight down,
(collets open) unscrew outer collet with collet wrench.
Unscrew counter-clockwise.
2.
Remove both inner and outer collets
3.
Thoroughly clean collet, you may use solvent to clean
collets, however, you must remove all traces of solvent
before replacing. Thoroughly clean collet body hole by
using pipe cleaner or small cloth on end of instrument.
Do not use any solvents in this hole. Put a thin film of
grease on outside of both collets. (This purpose of this
cleaning is to lubricate and prevent rust. Failure to clean
and grease will cause collets to slip and stick.)
4.
Replace collets, with collet wrench, screwing clockwise.
REPLACING WORN COLLETS
When tools (chucks) burrs, etc. Begin to slip, collets should
be replaced. When replacing collets, always use the
shortest possible stop that will still allow the tools to slip
into the master collet.
HOW TO REMOVE A STUCK COLLET
A collet may get rusty or dirty and stick if it is not cleaned
and greased regularly, or it may stick if collet is closed
without a tool in the collet. Open collet by moving handle
straight down (collet open). Put collet wrench in collet and
tap lightly on the end of the collet wrench and at the same
time attempt to unscrew the collet. If this does not loosen
the collet, with the handle in the same position, remove
the four screws that hold the chuck on the adapter and
remove chuck. Caution: be sure not to move the handle
during this procedure.
See instructions under removing
chuck from lathe page 3.
Grasp the steel clutch plate to
keep it from turning while you remove the collet.
CARE AND MAINTENANCE
Your Red Wing polishing motor has been fitted with ball bearings. No further lubrication is necessary during the life
of your motor. Occasionally remove the motor’s cord set from its electrical source and wipe the unit clean with a
clean, soft cloth. DO NOT use abrasive or liquid cleaners. Read, fully, the safety instructions.
Chuck/Changer Comes Installed
on models 16B and 16B-1.
Kit available for purchase
separately SKU:16
Adjusting the Chuck/Changer Tension to Collets
1.
Remove the plug which connects the lathe from the
electrical source.
2.
Move the activating handle on the Chuck/Changer to
the six o’clock (open collet position as seen in diagram 1
3.
Loosen the top set screw and the two lower set screws,
which are found on the 2-1 /2” adapter, which hold the
Chuck/Changer onto the lathe.
4.
Place your left hand on the left hand side of the lathe
and your right hand on the nose section of the Chuck/
Changer, and push the Chuck/Changer in toward the
lathe
as far as it will go. It will move approximately
1 /32-1 /16 of an inch inward toward the lathe.
5.
Holding the Chuck/Changer in your right hand, move the
activating handle clockwise to the 9:30- 10:00 o’clock
position. The Chuck/Changer will move outward, slightly.
Tighten the three set screws on the adapter which were
previously loosened, holding the Chuck/Changer in
NOTE:
If you have another person available to assist you in this short procedure, ask them to tighten the set screws. If
you do not, make certain that you hold the Chuck/ Changer inward toward the lathe when you tighten the set screws
on the adapter. This should alleviate the squeaking-grinding noise you are hearing by the lathe Chuck/ Changer
combination and place proper tension on collets.
REMEMBER:
Clean collets every 30 days.
For all Models
The alignment of the Chuck/
Changer to the clutch will alleviate
slipping clutch noise prob lems
and tension collets. Please
follow the instructions, below, to
alleviate these problems
.
i