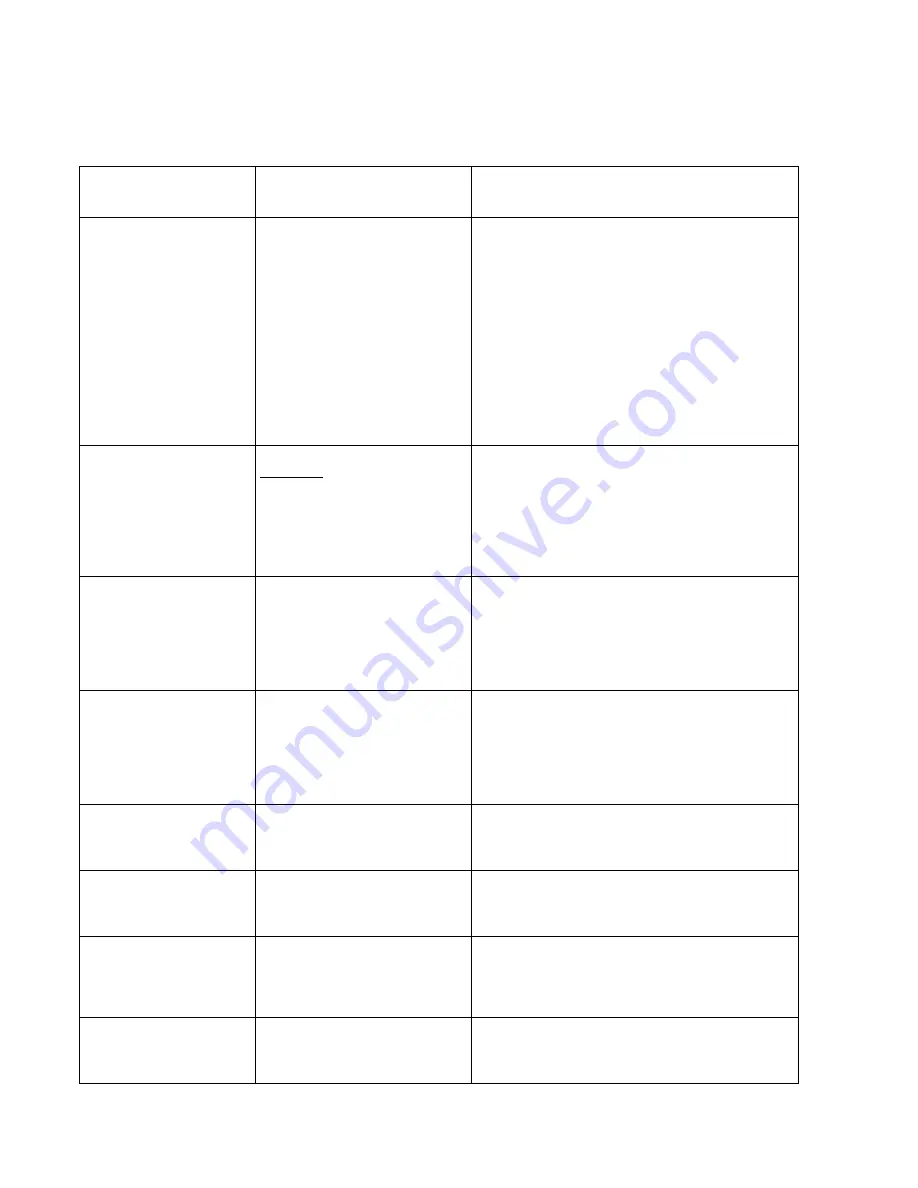
HAMWORTHY HEATING LTD
12
WEYMOUTH
500001112/C
8.0
FAULT FINDING
General fault finding is shown in Figure 18. If the Weymouth unit still does not operate satisfactorily, consult
Hamworthy Heating for assistance.
Figure 18. Fault Finding Guide.
Fault
Possible Causes
Action
Pump will not run
Unit up to pressure
No power to the unit
Isolator fuse blown
Cold Fill Pressure switch set
incorrectly
Cold fill pressure switch wired
incorrectly.
Pump seized or faulty
None
Check at source
Replace fuse in isolator. Note! Investigate cause of
blown fuse before restarting the unit
Adjust pressure switches (see section 7)
Check wiring against figure 25
Service or replace pump (see section 10)
Pump runs but will not build
up pressure
Pump isolating valve closed
(Advanced only)
Pump not primed
No water in tank
Pump non return valve jammed
Open valve (see fig 21)
Prime pump (see section 7.6)
Check water level and investigate if necessary
Check valve
Pump cuts in and out
rapidly (hunting)
Pressure switches set incorrectly
Non return valve not sealing
correctly
System Leak
Adjust pressure switches (see section 7)
Clean valve seat or replace valve if necessary (see
section 10.7)
Trace leak and ensure system is sound
Pump runs continuously
Cold fill pressure switch set
incorrectly
Cold fill pressure switch faulty
System leak
Adjust pressure switches (see section 7) *
Replace faulty switch (see section 10.5)
Trace leak and ensure system is sound
Pump cuts out at wrong
pressure
Cold fill pressure switch set
incorrectly
Cold fill pressure switch faulty
Adjust pressure switches (see section 7)
Replace faulty switch (see section 10.5)
Maximum system working
pressure too high
Cold fill pressure switch set
incorrectly
Cold fill pressure switch faulty
Adjust pressure switches (see section 7)
Replace faulty switch (see section 10.5)
Boiler switches off un-
expectedly
Hi or lo pressure switches set
incorrectly
Hi or lo pressure switches &
circuits wired incorrectly
Adjust pressure switches (see section 7)
Check wiring with Wiring diagram in appendix
System pressure runs
consistently at cold fill
pressure
Small system leak
Trace leak and ensure system is sound.