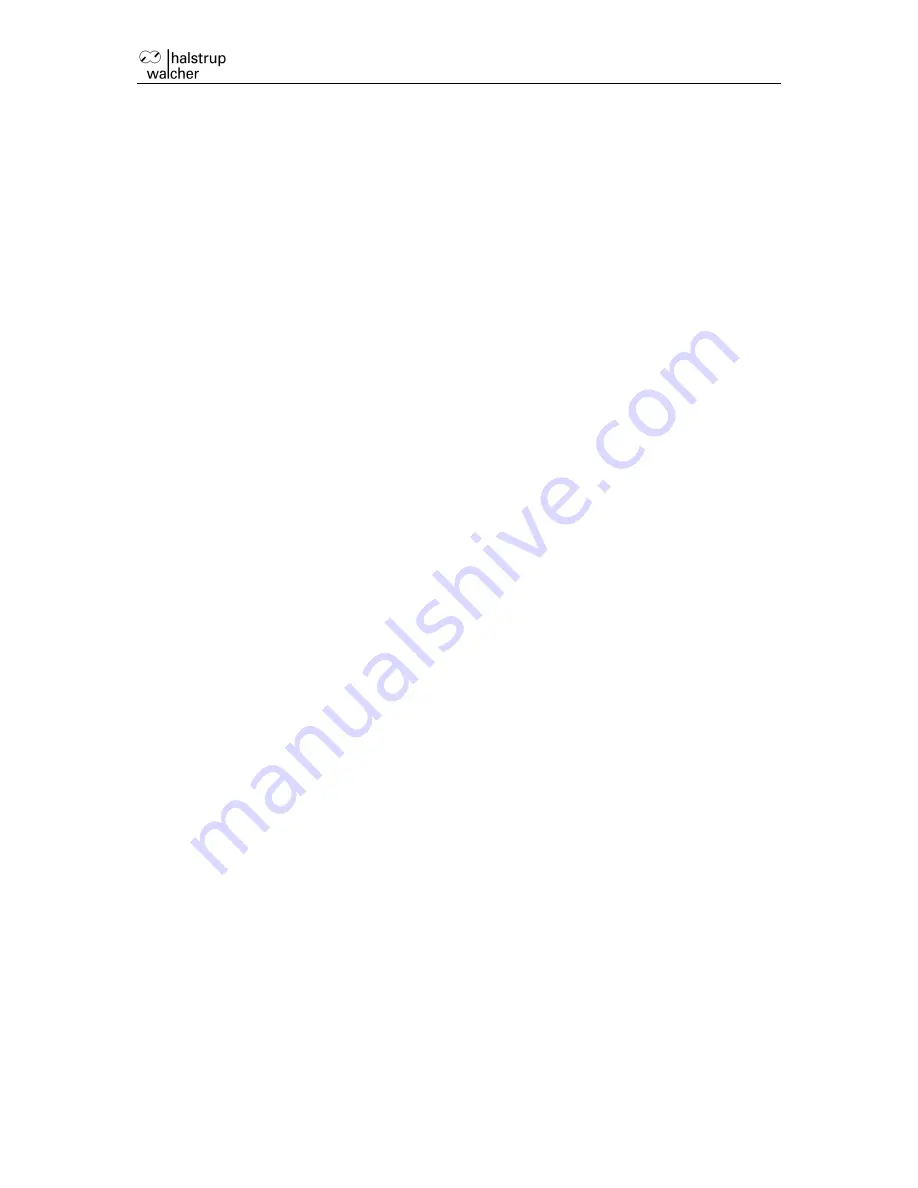
Instruction Manual PSx3xxC
23
3 Sequence of positioning
a) Positioning run
-
The drive must be set to CANopen ‘operational mode’ before it can be controlled
using PDOs.
- Transfer target value (PDO with control word = 0014h and target value, or target
value to SDO #2001): drive begins run
- Abort run by resetting the release bit (transmit PDO with control word = 0000h or
transmit SDO #2024 with value 0000h).
- If a new target value is transferred during a positioning run, the device will
immediately proceed to the new target. There will be no interruption if the direction of
rotation does not need to be altered.
- If a manual run is transmitted during a positioning run, the positioning run will be
aborted (speed will be reduced to that of a manual run) and the device proceeds with
the manual run.
The following sequence of steps is also possible:
Starting situation:
- release has not been set
- Target value has already been transferred (in case of PDO transfer the release in the
control word was not set already)
Set release: drive begins run
b) Positioning run without loop
The sequence corresponds to that of a positioning run with loop; in addition to setting
the release, however, bit 6 in the control word also has to be set to execute the run
without loop.
c) Manual run
- start manual run (transmit PDO with control word = 0011h resp. 0012h or transmit
SDO #2024 with value 0011h resp. 0012h): device begins to run
- End manual run by clearing the manual run command (transmit PDO with control
word = 0010h or transmit SDO #2024 with value 0010h) or by deasserting release
(transmit PDO with control word = 0000h or transmit SDO #2024 with value 0000h).
- Transferring a target value during a manual run will end the manual run and the
device will immediately move on to the transmitted position.
4 Specials
a) Speed, acceleration and deceleration
The initial reference loop and the manual run are performed at the maximum speed
specified in SDO #2013; positioning runs are performed at the maximum speed
specified in SDO #2012. When the run is counterclockwise, additionally the maximum
speed in SDO #2020 applies, when the run is clockwise, the one in SDO #2021
applies. For all runs the maximum acceleration in SDO #201C and the maximum
deceleration in SDO #201D apply. At the end of each run the maximum deceleration
Summary of Contents for PS*3**C series
Page 32: ...Instruction Manual PSx3xxC 32 ...