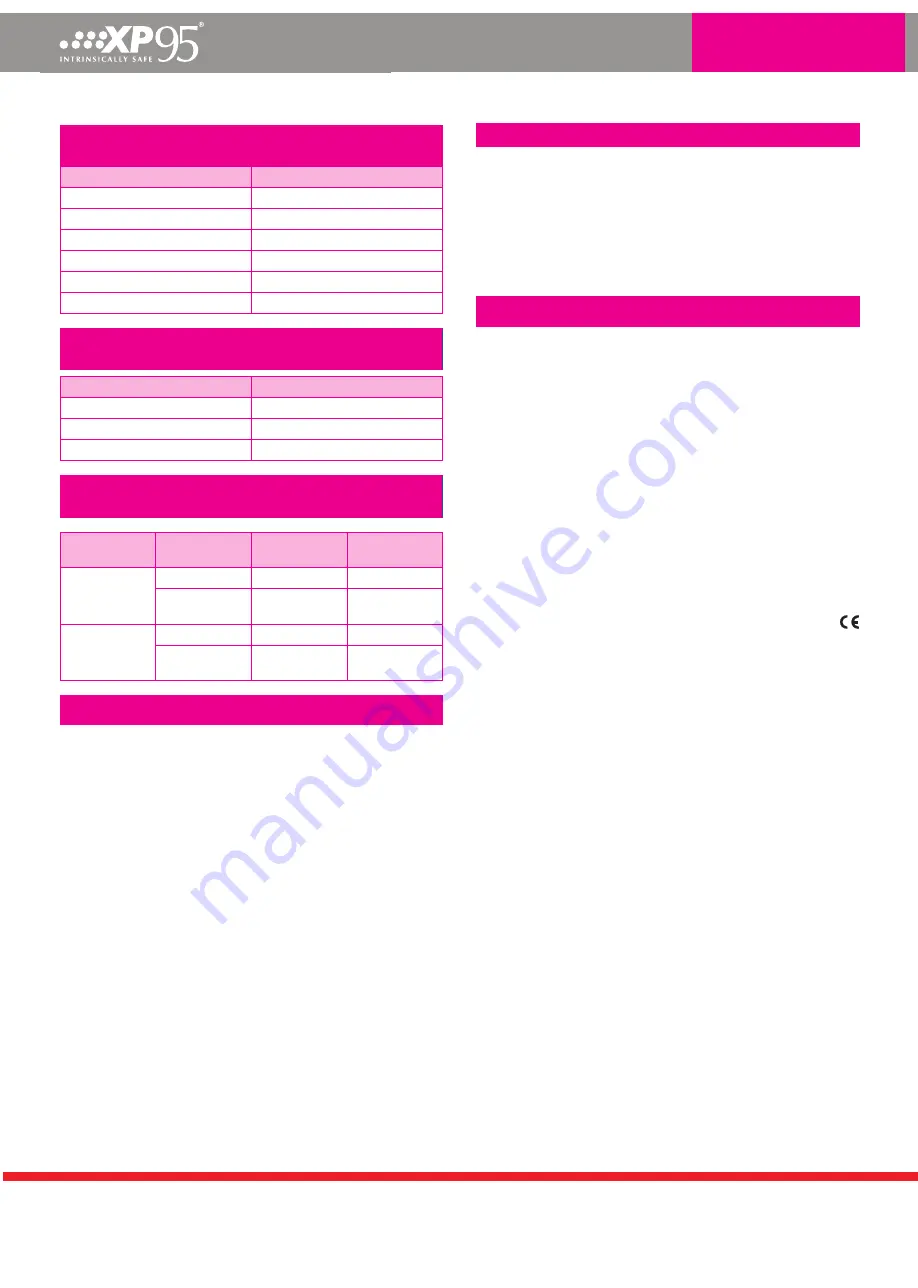
Intrinsically safe
PP1095/2021/Issue 6
Page 6 of 8
Table 5: Maximum loading 28 V/300 Ω single channel
barrier
Max. No of LEDs illuminated
Max. (Total) device load (mA)
0
8.0
1
7.0
2
6.0
3
5.0
4
4.0
5
3.0
Table 6: Maximum loading 28 V Galvanic Isolator Single
Channel Barrier
Max. No of LEDs illuminated
Max. (Total) device load (mA)
0
4.0
1
3.0
2
2.0
Table 7: Loading of the fire loop from a Translator and
Barrier pair
Characteristic
Zener Barrier
Galvanic
Barrier
Min Loading
Current (mA)
1
5
Capacitance
(nF)
1
90
Max Loading
Current (mA)
10
10
Capacitance
(nF)
80
170
Using Galvanically Isolated Barriers
Whilst the cable parameters in Table 4 specify the allowable limits
for energy storage in the Hazardous area wiring these values do
not generally allow reliable XP95 protocol transmission. This is
particularly true when using Galvanically Isolated Barriers. Due
to their design, these barriers present a relatively high capacitive
load on the main fire loop. Therefore, the main fire loop capacitive
loading and the I.S. spur capacitive loading must be carefully
considered when designing a fire system.
The maximum impedance allowed on the I.S. spur is 15 ohms and
80nF, which is typical of 500m of FP200 cable.
The maximum capacitive load that can be tolerated on the fire loop
will be defined by the Control Panel manufacturer. The capacitive
load of the IS zone includes 90nF for the galvanic barrier and the
total cable capacitance (80nF maximum). This should be added to
the main fire loop capacitance and compared with the fire panel
specification.
Additionally, a galvanic barrier will add 5mA to the system load
which should be added to the loop loading calculations.
The loop calculations for each I.S spur often use the maximum
load of 10mA and 200nF as the equivalent load on the fire main
loop. Any calculation must ensure that the translator has at least
19V at the translator input.
Servicing
Servicing of I.S. fire detectors may be carried out only by a
BASEEFA authorised body. In practical terms this means that
Apollo XP95 I.S. fire detectors may be serviced only by Apollo at its
factory. Servicing of the fire protection system should be carried
out as recommended by the code of practice BS 5839-1 or other
local regulations in force. For more information on servicing Apollo
detectors, please refer to the care, service and maintenance guide,
PP2055.
Approvals
XP95 I.S. detectors have been approved by LPCB to EN54 and the
XP95 I.S. Manual Call Point, Part No 55100-940, is LPCB approved
to EN54-11. These products have also been approved for marine
use by the following bodies:
• American Bureau of Shipping
• Bureau Veritas
• DNV GL
• Lloyds Register of Shipping
• China Classification Society
• Korean Register of Shipping
Details of approvals held are available on request.
The product certification technical files for the XP95 I.S. range are
held by BASEEFA in accordance with the requirements of the ATEX
Directive 2014/34/EU. All detectors and manual call points are
marked.