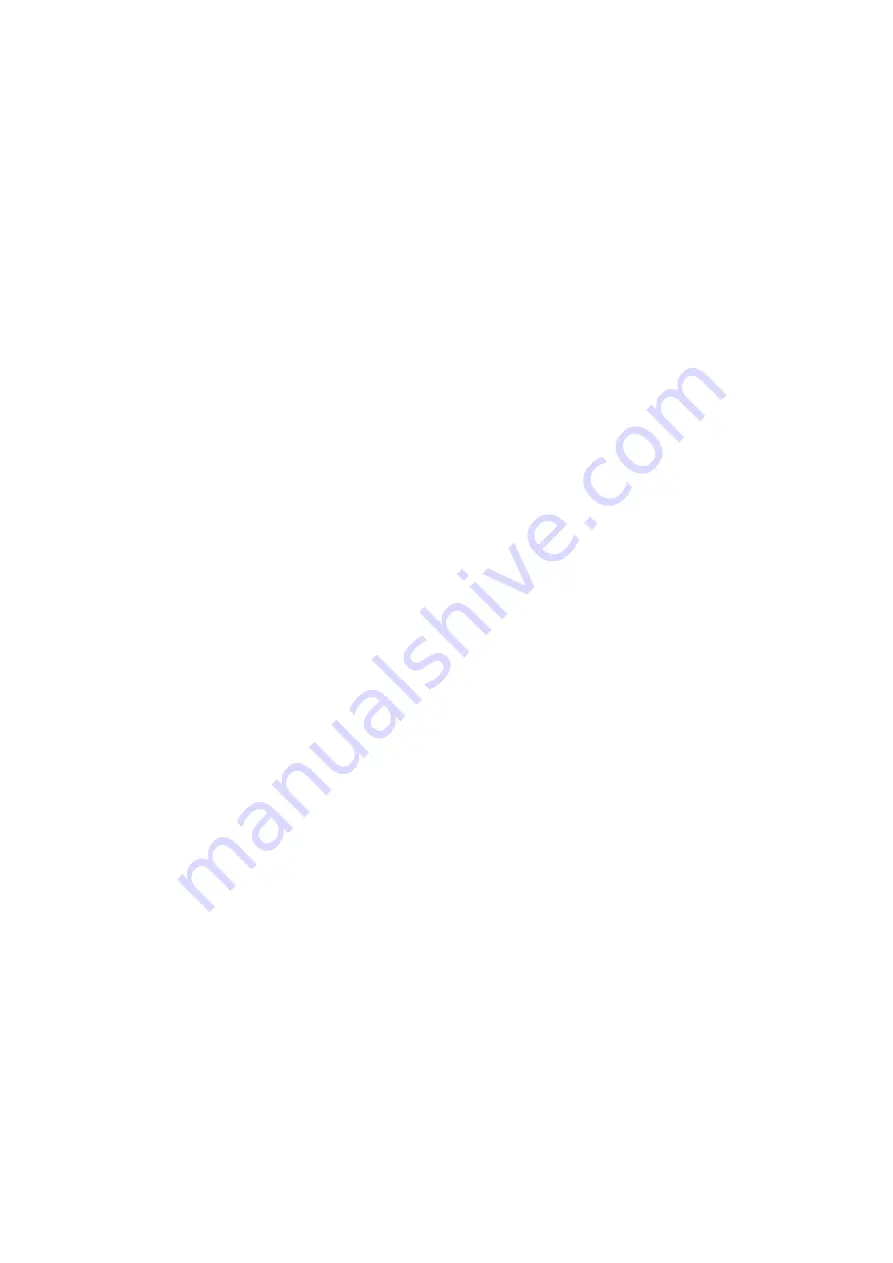
16
FIRST MONTH or 20 HOURS then
EVERY 200 HOURS RUNNING TIME OR EVERY 12 MONTHS
Whichever is the sooner
Drain the engine oil – this should be carried out while the engine is WARM:
1) Remove the drain plug (located on the side of the sump) and drain out the old oil.
2) Refit the sump plug securely and then refill the sump with fresh oil – See list of
RECOMMENDED LUBRICANTS.
3) Refill until the oil level is at the correct-reading mark on the dipstick. This will take
approximately 2.0 litres, excluding the filter.
4) Renew the screw-on filter cartridge (oil capacity 0.6 litres).
5) Clean the spark plugs and, if necessary, adjust the gaps – the correct gap setting is 0.6 to
0.7mm.
Note:
Adjust the gap by bending the overhead electrode – NEVER the centre
electrode.
6) Clean the spark-plug seating surfaces in the cylinder head, taking care that foreign matter
does not enter the engine cylinder bores.
GENERAL CHECKS
1) Tightness of ALL pipe connections.
2) Electrolyte level in the battery – top-up if necessary.
WARNING: DO NOT SMOKE OR ALLOW A NAKED FLAME NEAR THE
BATTERY WHEN EITHER CHECKING OR CHARGING IT –
EXPLOSIVE GASES CAN BE RELEASED.
3) Check the inlet and exhaust-valve clearances with the engine COLD and adjust as
necessary.
Gauges
Do not clean the glass surfaces of the gauges with abrasive or solvent cleaners. These will cloud the
glass surface, use a mild detergent and water.
Tests and Fault-Tracing Charts
The following pages contain the important MONTHLY PUMP TEST and the FAULT-TRACING
CHARTS for both the Pump and the Engine.