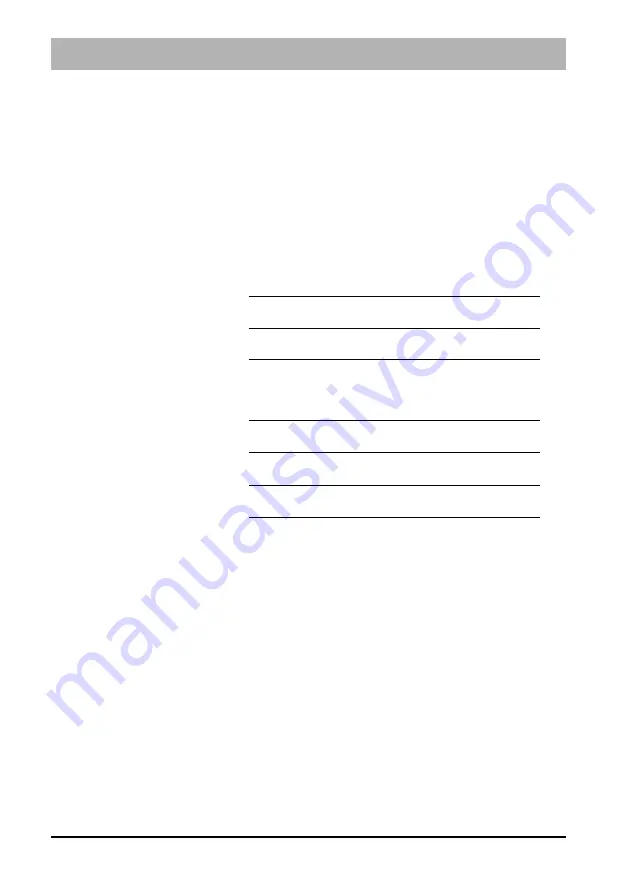
4
00-7177-00.fm
Acceptance of the machine
Inspect the machine immediately on delivery for signs of transport damage.
You will be compensated for transport damage provided you immediately have
the damage confirmed by the transport company and send in the damage
report together with the consignment note to us.
Machine data
Your machine is described clearly by the following data. Please always quote
these data in correspondence or when making a telephone query to your
authorised Hako dealer or our company.
•
Machine type
•
Manufacturing no.
•
Start-up on:
Your nearest authorised Hako dealer:
•
Address:
•
Telephone:
Introduction