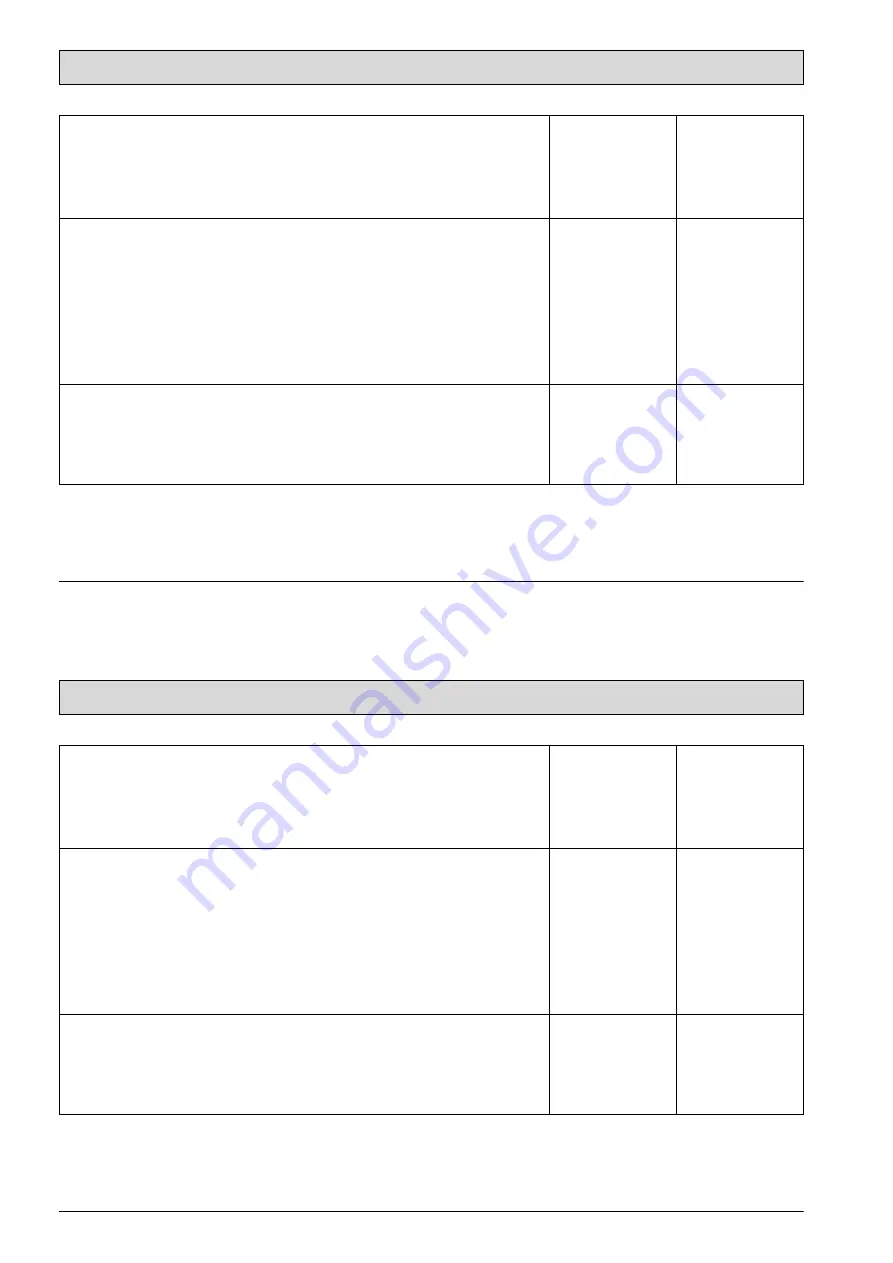
34
Technical Data
Chassis/Brakes
Tires, front/rear
23x8.50-12 4PR
Rims, front/rear
7.00-JAx12
Tire pressure, front/rear
bar
1.5/2.0
Wheel bolt tightening torque
Nm
86
Suction and sweeping system
Suction turbine speed
rpm
2120
Suction turbine diameter
mm
505
Max. intake air volume
m
3
/h
2800
Suction pipe diameter
mm
180
Suction nozzle width
mm
440
Circular brush diameter
mm
720
Circular brush speed
rpm
90
Dust particle filter system
Fine particle filter (serial) filtration efficiency
%
V
Metal filters (option):
- Preliminary filter (coarse fabric filling) packing density
- Main filter (fine fabric filling) packing density
kg/m
3
kg/m
3
220
220
34
Technical Data
Chassis/Brakes
Tires, front/rear
23x8.50-12 4PR
Rims, front/rear
7.00-JAx12
Tire pressure, front/rear
bar
1.5/2.0
Wheel bolt tightening torque
Nm
86
Suction and sweeping system
Suction turbine speed
rpm
2120
Suction turbine diameter
mm
505
Max. intake air volume
m
3
/h
2800
Suction pipe diameter
mm
180
Suction nozzle width
mm
440
Circular brush diameter
mm
720
Circular brush speed
rpm
90
Dust particle filter system
Fine particle filter (serial) filtration efficiency
%
V
Metal filters (option):
- Preliminary filter (coarse fabric filling) packing density
- Main filter (fine fabric filling) packing density
kg/m
3
kg/m
3
220
220