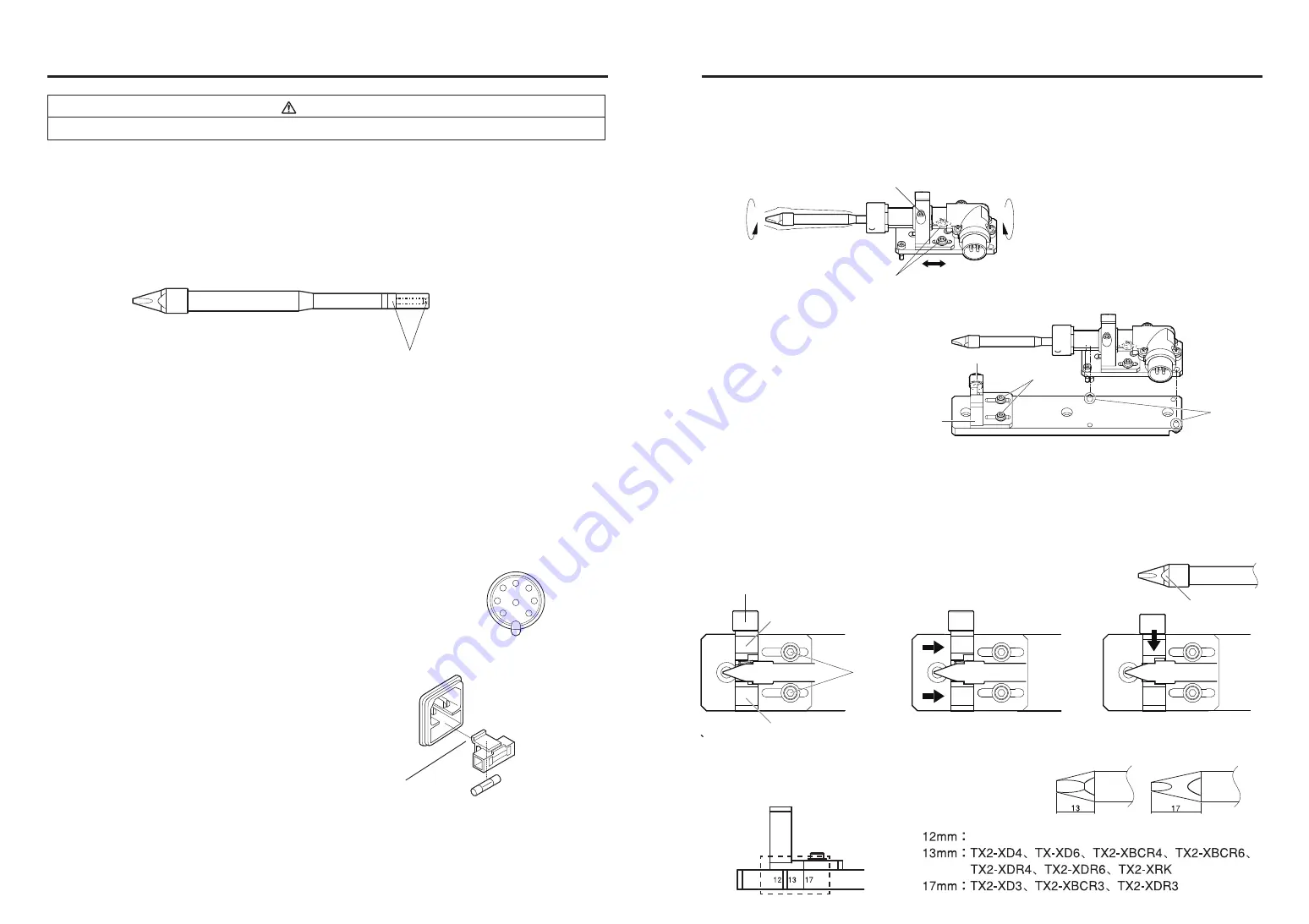
6
17
2. Loosen the following screws
①
and
②
and place the HAKKO FU-6002
on the tip adjustment jig unit with the positioning pins aligned.
3. Align the D-cut face of the tip with the pocket in the fixed side.
Move the tip adjustment jig until the tip is fully inserted as shown in the following figure.
This position will be the reference point. Retighten the two screws
①.
To prevent the upward movement and misalignment of the tip, tighten the screw
②
while pressing
the tip from the top.
Do not move the jig except for the one on the movable side and except for the time
when the type of workpiece is changed. After the reference point has been set,
remove the HAKKO FU-6002 from the tip adjustment jig unit.
●
How to position the tip
1. To turn the shaft of the tip, loosen the positioning screw
①
.
To move the soldering iron in the longitudinal direction, loosen the positioning screw
②
.
Tighten the screws after determining the tip position balancing with your work object.
D-cut face
Movable side
Fixed side
Screw
②
Screw
①
9. CHECKING PROCEDURE
■
Check for a broken heater or sensor
Verify the electrical integrity of the heater and sensor.
Measure the resistance of the heater and sensor while at room temperature (15℃ to 25℃; 59℉ to
77℉). It should be 3.
4Ω±10
%
. If the resistance exceeds these limits, replace it.
■
Check the grounding line
1. Unplug the iron cable from the station.
2. Measure the resistance between the pin 2 and tip with the iron cable connected to
the HAKKO FU-6002.
3. If the value exceeds 2Ω (at room temperature), perform the tip maintenance in page 15.
If the value still does not decrease, check the connection cord for breakage.
■
Check the iron cable for breakage
Measure the resistance of the pin.
Pin 1 to Pin 3
-
3.0 to 3.8Ω
If the resistance exceeds these limits, replace the iron cable.
Contact your HAKKO representative.
■
Replace the fuse
1. Unplug the power cord from the power receptacle.
2. Remove the fuse holder.
3. Replace the fuse.
4. Put the fuse holder back in place.
Measure the resistance across this position
1
4
7
2
8
5
6
3
Unless otherwise directed, carry out these procedures with power switch OFF and the power UNPLUGGED.
WARNING
①
For shaft turning
②
For longitudinal adjustment
positioning pin
Jig base
Tip adjustment jig
Screw
①
Loosen
Screw
②
Loosen
※ There are marking on the side of the tip adjustment jig unit.
The tip ends are classified into 12 mm, 13 mm and 17 mm. While referring to this marking,
adjust the position of the jig fixture.