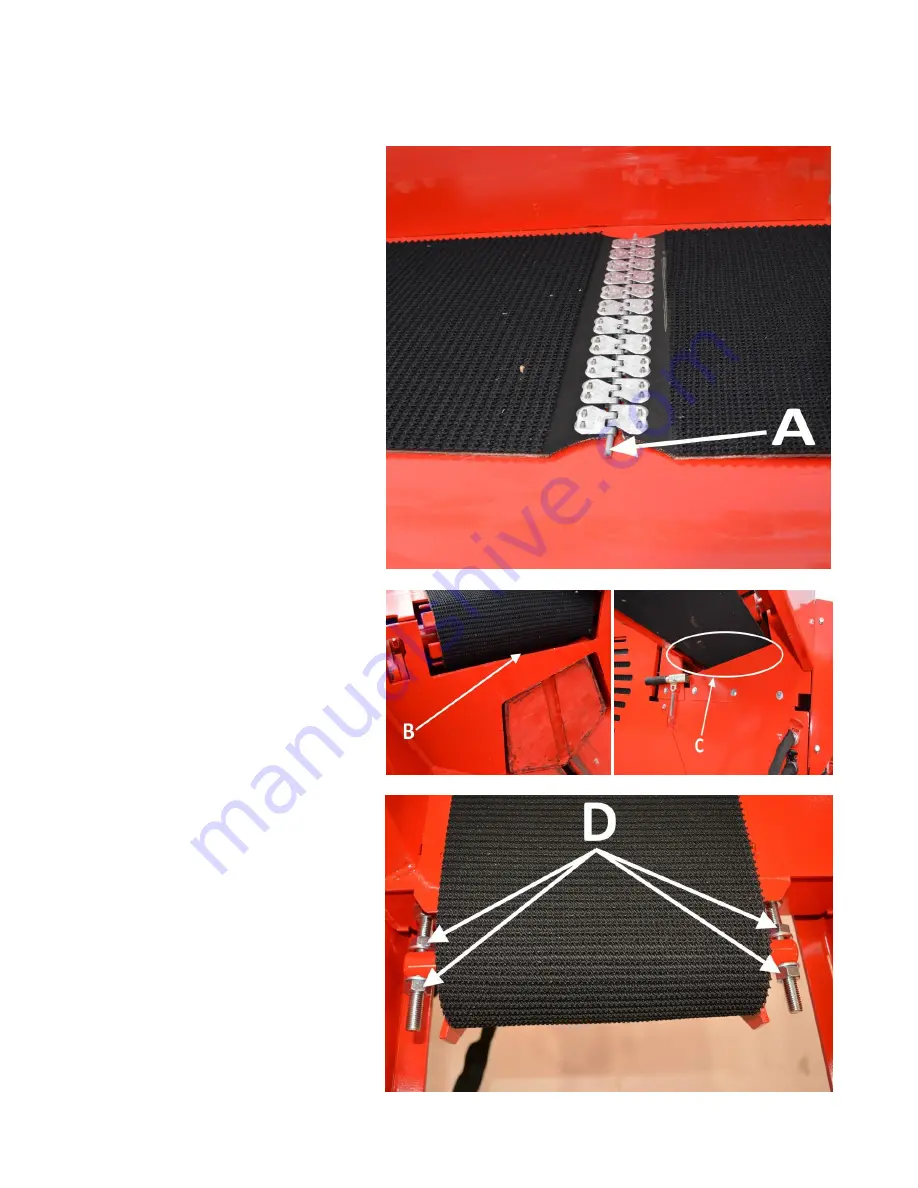
34 / 47
Hakki Pilke 50 Pro
Translation
Version 1-2018
5.4.
Conveyor maintenance
5.4.1.
Replacing and tensioning the in-feed conveyor belt
Replace the in-feed conveyor belt as
follows:
1.
Shut the machine down and
disconnect it from its power
sources.
2.
Raise and lock the in-feed
conveyor into the transport
position. (See Section 3.1.1.)
3.
Move the belt joint to a
suitable height.
4.
Disconnect the joint by using,
for example, pliers to pull out
pin A (Figure 31) holding the
joint together.
5.
Remove the old belt.
6.
Slide the new belt under the
table through opening B at
the side of the in-feed
conveyor's drive roller until
you can pull the belt out from
the other end C.
7.
Lead the rest of the belt
under the log press, around
the rear roller and, finally,
behind the conveyor.
8.
Connect the joint by inserting
pin A into the joint.
9.
Turn the conveyor back to the
operating
position
and
tension the belt.
10.
Finally, adjust the belt to the
correct tension and to run
straight with the help of the
adjustment nuts D.
The belt is at the correct
tension when its middle
section is raised approx. 5 cm
when the conveyor is in the
operating
position.
An
excessively tight belt may be
damaged more easily, and it
places unnecessary strain on
the bearings of the conveyor.
Figure 31.
Figure 32. Figure 33.
Figure 34.