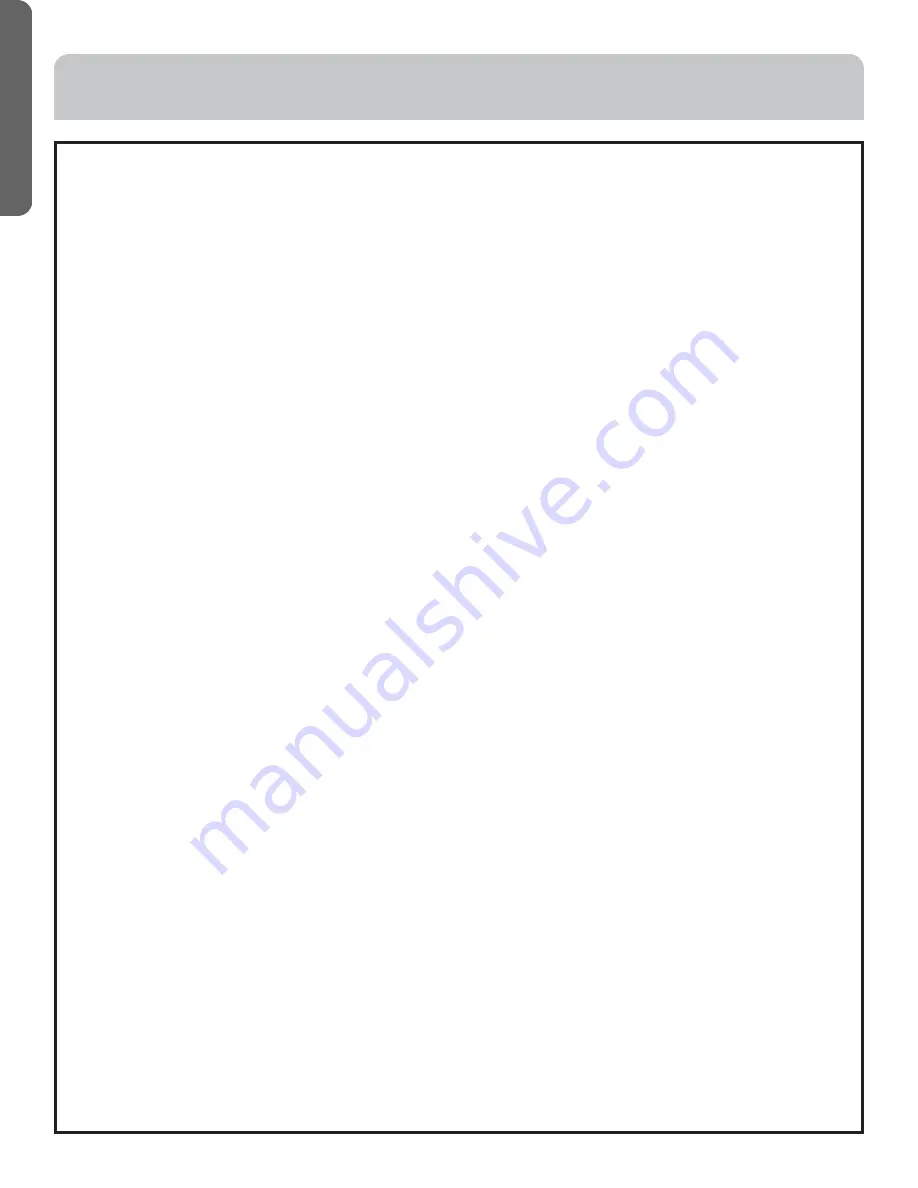
32
31-5000755 Rev. 0
ENGLISH
TEST RUN AND FAULT CODE
Before RUN TEST
• Connect unit to the power supply of the outdoor units to energize the heater of the compressor. Power the system
on for 12 hours prior to start up to protect the compressor.
• Check if the connections of the drainpipe and wire connection lines are correct.
• Run the drain line below the outlet of the unit. Insulate the condensate drain piping to prevent condensation. Install
drain piping with proper slope away from the indoor units.
• Checkup of Installation
• Check if the main voltage is correct
• Check for any leaks at the piping joints
• Check if the connection of the main power for the indoor & outdoor units are correct
• Check if the serial numbers of the terminals are matched properly
• Check if the installation place meets the requirement
• Check if there is too much noise
• Check if the connecting line is fastened
• Check if the refrigerant and condensation lines are insulated
• Check if the water is drained to the outside
• Check if the indoor units are positioned
RUN TEST
• Equipment installers should test-run all equipment. Test procedures are listed in the installation manual. Take the
testing procedures according to the manual and check if the temperature regulator works properly.
• When the machine fails to start due to the room temperature, the following procedures can be taken to do the
compulsive running. The function is not provided for the type with remote control.
• Set the YR-E16B and QACT17A wired controller to cooling/heating mode, press "ON/OFF" button for 10 seconds to
enter into the compulsive cooling/heating mode. Press "ON/OFF" button again to quit the compulsive running and
stop the operation of the system.
Fault Remedies
• When any fault appears, consult the fault code of line control or the number of LED flashes on the control panel of the
indoor units/health lamp of receiving window of remote control. Refer to the below table lookup fault descriptions.