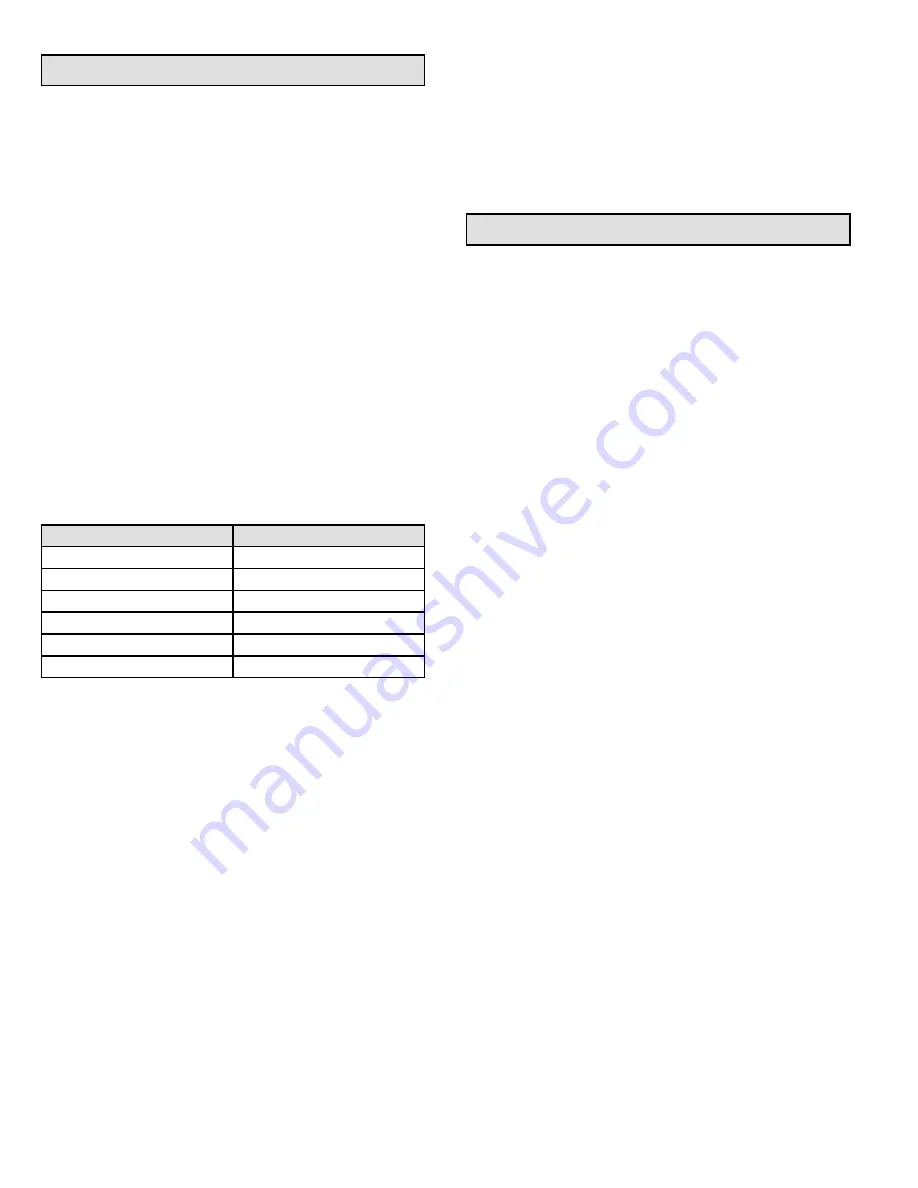
507919-01
Page 2 of 21
Issue 1946
1. Always wear proper personal protection equipment.
2. Always disconnect electrical power before removing
panel or servicing equipment.
3. Keep hands and clothing away from moving parts.
4. Handle refrigerant with caution; refer to proper MSDS
from refrigerant supplier.
5. Use care when lifting, avoid contact with sharp edges.
Installation
NOTE:
In some cases, noise in the living area has been
traced to gas pulsations from improper installation of
equipment.
• Locate unit away from windows, patios, decks, etc.
where unit operation sounds may disturb customer.
• Leave some slack between structure and unit to
absorb vibration.
• Place a sound-absorbing material, such as Isomode,
under the unit if it will be installed in a location or
position that will transmit sound or vibration to the
living area or adjacent buildings.
• Install the unit high enough above the ground or roof to
allow adequate drainage of defrost water and prevent
ice buildup.
• In heavy snow areas, do not locate the unit where
drifting snow will occur. The unit base should be
elevated above the depth of average snows.
NOTE:
Elevation of the unit may be accomplished
by constructing a frame using suitable materials. If a
support frame is constructed, it must not block drain
holes in unit base.
• When installed in areas where low ambient
temperatures exist, locate unit so winter prevailing
winds do not blow directly into outdoor coil.
• Locate unit away from overhanging roof lines which
would allow water or ice to drop on, or in front of, coil
or into unit.
When outdoor unit is connected to factory-approved indoor
unit, outdoor unit contains system refrigerant charge for
operation with matching indoor unit when connected by 15
ft. of field-supplied tubing. For proper unit operation, check
refrigerant charge using charging information located on
control box cover.
Outdoor Section
Zoning ordinances may govern the minimum distance the
condensing unit can be installed from the property line.
Install on a Solid, Level Mounting Pad
The outdoor section is to be installed on a solid foundation.
This foundation should extend a minimum of 2” (inches)
beyond the sides of the outdoor section. To reduce the
possibility of noise transmission, the foundation slab
General
Read this entire instruction manual, as well as the
instructions supplied in separate equipment, before
starting the installation. Observe and follow all warnings,
cautions, instructional labels, and tags. Failure to comply
with these instructions could result in an unsafe condition
and/or premature component failure.
These instructions are intended as a general guide only
for use by qualified personnel and do not supersede any
national or local codes in any way. The installation must
comply with all provincial, state, and local codes as well as
the National Electrical Code (U.S.) or Canadian Electrical
Code (Canada). Compliance should be determined prior
to installation.
This unit uses R-410A, which is an ozone-friendly HFC
refrigerant. The unit must be installed with a matching
indoor coil and line set. A filter drier approved for use with
R-410A is installed in the unit.
When servicing or repairing HVAC components, ensure
the fasteners are appropriately tightened. Table 1 shows
torque values for fasteners.
Fastener
Torque
Stem Caps
8 ft. lbs.
Service Port Caps
8 ft. lbs.
Sheet Metal Screws
16 in. lbs.
#8 Machine Screws
16 in. lbs.
#10 Machine Screws
28 in. lbs.
Compressor Bolts
90 in. lbs.
Table 1. Torque Table
Inspection of Shipment
Upon receipt of equipment, carefully inspect it for possible
shipping damage. If damage is found, it should be noted
on the carrier’s freight bill. Take special care to examine
the unit inside the carton if the carton is damaged. Any
concealed damage discovered should be reported to the
last carrier immediately, preferably in writing, and should
include a request for inspection by the carrier’s agent.
If any damages are discovered and reported to the carrier
DO NOT INSTALL THE UNIT
, as claim may be denied.
Check the unit rating plate to confirm specifications are as
ordered.
Safety Precautions
Follow all safety codes. Wear safety glasses and work
gloves. Use quenching cloth for brazing operations.
Have fire extinguisher available. Read these instructions
thoroughly and follow all warning or cautions attached to
the unit.